عنصر آهن و کاربردهای آن — از صفر تا صد

آهن بعد از آلومینیوم، بیشترین فلز موجود در پوسته زمین است. سنگ معدن آهن معمولا به صورت اکسید وجود دارد که با فرآیندهای کاهشی و به کمک کربن (کُک) در دمای بالا و کوره بلند به آهن تبدیل میشود. بیش از 98 درصد از این آهن تولیدی را حتی قبل از سرد شدن به فولاد تبدیل میکنند. مقدار کمی هم در تولید «چدن» (Cast iron) و «فرفورژه» (Wrought Iron) بکار میگیرند. این عنصر که با نماد و با عدد اتمی 26 در گروه هشت از جدول تناوبی عناصر وجود دارد، از گذشته و دوران باستان مورد توجه بوده است. البته تعداد اشیا کشف شده از دوران کهن نسبت به اشیا ساخته شده با طلا یا نقره کمتر است چراکه این فلز بیشتر دچار خوردگی میشود.
در سال 1774، شیمیدان فرانسوی، آنتوان لاوازیه از واکنش بخار آب با آهن در داخل یک لامپ آهنی برای تولید هیدروژن استفاده کرد. این آزمایش سبب اثبات پایستگی جرم و تبدیل علم شیمی از یک دانش کیفی به یک دانش کمی شد.
موارد استفاده از آهن
همانطور که گفته شد، مقادیر کمی از این فلز در ساخت چدن بکار میرود. چدن در حدود 92 درصد از آهن خالص ساخته شده است. مابقی در حدود ۲-5 درصد کربن، ۱-3 درصد سیلیکون و مقادیری منگنز، فسفر و گوگرد را تشکیل میدهند. در گذشته از آن در رادیاتورهای حرارتی، اجاقهای قدیمی، پوشش سقفها، موانع و چراغهای شهری استفاده میشد. البته به علت شکنندگی و تمایل آن به خوردگی، چدن با دیگر مواد جایگزین شد.
فرفورژه (گلنرده) حاوی کمتر از 0/15 درصد کربن است که به کمک فرآیند کاهش سنگ آهن در حالت جامد بدست میآید. از آنجایی که فرفوژه قابلیت چکشخواری و خم شدن داشت، از آن در طراحی نردهها، دروازهها، مبلمان باغهای قدیمی و محصولات دکوری دیگر استفاده میشد. امروزه از فولاد در تهیه این نوع از محصولات استفاده میشود.
آهن، بیشترین استفاده را در میان فلزات دارد و بیش از 90 درصد فلزات تولیدی در جهان را شامل میشود. قیمت کم و مقاومت بالای آن از عوامل رونق آن بوده است. این فلز در ساخت ابزارآلات، ریلهای راهآهن، خودروها، میلگرد و بسیاری سازههای جادهای کاربرد دارد. از آنجایی که آهن خالص همانند طلا نرم است، معمولا آن را به صوت آلیاژی از عناصر مختلف بکار میبرند.
آلوتروپها و خواص فیزیکی و شیمیایی آهن
حداقل چهار آلوتروپ از این فلز با نمادهای ، ، و شناخته شده است. آلوتروپهای آلفا، گاما و دلتا در فشار معمول حضور دارند. خواص فیزیکی آهن در فشارهای بسیار زیاد نیز مورد مطالعه قرار گرفته است. در فشار ، آهن آلفا به آلوتروپ آهن «اپسیلون» تبدیل میشود.
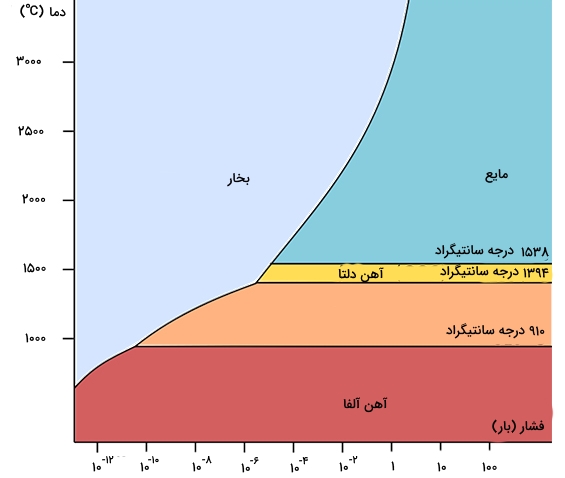
خواص مغناطیسی آهن
پایینتر از «نقطه کوری» (Curie Point)، یعنی کمتر از 770 درجه سانتیگراد، آهن آلفا از حالت پارامغناطیس به فرومغناطیس تغییر میکند. اسپین دو الکترون جفتنشده در هر اتم با اسپین اتمهای مجاور همتراز و سبب ایجاد یک میدان مغناطیسی میشوند. در غیاب یک منبع خارجی میدان مغناطیسی، اتمها به طور خود به خودی در «دامنههای مغناطیسی» (Magnetic Domain) با فاصله معین ده میکرومتری از هم قرار میگیرند به گونهای که اتمها در هر دامنه مغناطیسی، اسپین موازی دارند، اما دامنههای مختلف، اسپین متفاوتی خواهند داشت به همین دلیل، قطعهای از آهن، میدان مغناطیسی ندارد.
ترکیبات شیمیایی آهن
آهن خواصی همچون فلزات واسطه از خود نشان میدهد به این معنی که اعداد اکسایش متفاوتی دارد. آرایش الکترونی آهن به صورت زیر است:
در این آرایش، اوربیتالهای و از لحاظ انرژی به یکدیگر بسیار نزدیک هستند و در نتیجه برای رسیدن به پایداری گاز نجیب قبل خود، تعداد متفاوتی الکترون از دست میدهند. البته در بیشتر موارد، این فلز ترکیباتی با عدد اکسایش و تشکیل میدهد که به ترتیب به نامهای آهن (II) و آهن (III) موسوماند.
برخلاف دیگر فلزات، آهن با جیوه تشکیل آمالگام (ملغمه) نمیدهد. در نتیجه، برای نگهداری و فروش جیوه، استفاده از ظروف آهنی مرسوم است.
اگرچه از این فلز بیشتر در مهندسی مواد استفاده میشود اما ترکیبات آن در صنایع دیگر نیز مورد استفاده قرار میگیرند. به عنوان مثال از کاتالیزورهای آهنی در فرآیند هابر و تولید آمونیاک استفاده میشود. همچنین از این فلز در «فرآیند فیشر-تروپش» (Fischer-Tropsch Process) برای تبدیل مونواکسید کربن به سوختهای هیدروکربنی بهره میگیرند. پودر آهن در یک محلول اسیدی در کاهش نیتروبنزن به آنیلین کاربرد دارد. تصویر زیر که به فرآیند «کاهش بشان» (Bechamp Reduction) موسوم است حالت کلی تبدیل ترکیبات نیتروژنی آروماتیک را به آنیلین نشان میدهد:
اکسیدها و هیدروکسیدهای آهن
این فلز ترکیبات متفاوتی از اکسید و هیدروکسید تشکیل میدهد. معمولترین نوع این ترکیبات، اکسید آهن (II و III) با فرمول و آهن (III) اکسید با فرمول است. البته آهن (II) اکسید هم وجود دارد که در دمای اتاق پایدار نیست. معروفترین سولفید آهن با نام «پیریت» شناخته میشود که جلای طلایی رنگ دارد و در متون فارسی به آن مارقشیشا میگویند. این ماده یک ترکیب با آهن (IV) نیست بلکه درواقع یک آهن (II) پلیسولفید حاوی یونهای و در یک «ساختار آشفته» (Distorted Structure) است.
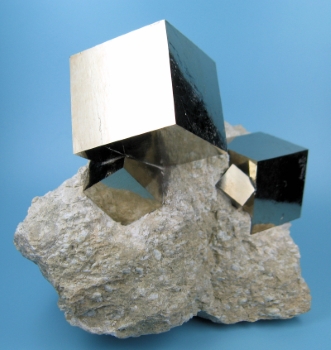
هالیدهای آهن
هالیدهای دوتایی فریک و فروس دو نوع از شناختهشدهترین هالیدهای آهن هستند. هالیدهای فروس از طریق واکنش با «اسیدهای هیدروهالیک» (Hydrohalic Acid)، نمکهای آبدار تولید میکنند:
این عنصر با فلوئور، کلر و برم واکنش و تشکیل کلرید آهن میدهد:
البته آهن (III) یدید از این قانون تبعیت نمیکند. به علت قدرت اکسندگی و کاهندگی شدید ، این ترکیب ناپایدار است:
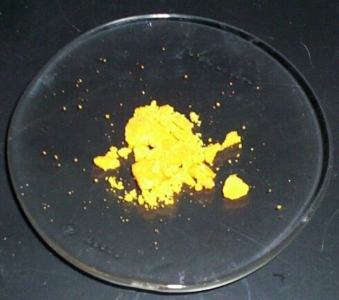
آهن و محلولها
«پتانسیل اکسید و احیا» (پتانسیل استاندارد کاهش) در یک محلول اسیدی برای یونهای معمول آهن در زیر آورده شده است:
محلول قرمز-بنفش فِرات (VI) با ساختار چهاروجهی و فرمول ، اکسندهای قوی است. این آنیون، نیتروژن و آمونیاک را در دمای اتاق اکسید میکند. این ماده حتی قابلیت اکسید کردن آب را در محلولهای خنثی یا اسیدی دارد که واکنش آن در زیر آورده شده است:
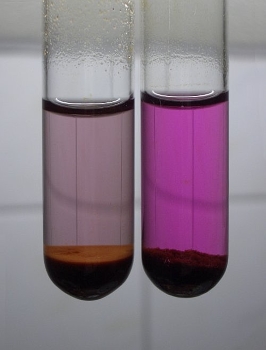
تولید سالانه آهن
اقتصاد رو به رشد چین با تولید غیر منتظره این فلز و فولاد همراه بود. تقریبا نیمی از آهن تولیدی در جهان توسط چین ساخته میشود. جدول زیر، تولید سالانه این فلز را در دنیا نشان میدهد.
کل دنیا | 1180 میلیون تن |
چین | 710 میلیون تن |
ژاپن | 84 میلیون تن |
هند | 54 میلیون تن |
روسیه | 51 میلیون تن |
کره | 47 میلیون تن |
برزیل | 30 میلیون تن |
آلمان | 28 میلیون تن |
آمریکا | 26 میلیون تن |
تولید آهن
آهن از طریق واکنشهای ردوکس (اکسید و احیا) از سنگ آهن به تولید میرسد. درحالیکه «کوره بلند» (Blast Furnace)، فرآیند اصلی در کاهش سنگ آهن را شامل میشود، اما فناوریهای دیگری نیز برای تولید آهن در مقیاس کمتر مورد استفاده قرار میگیرند. البته دسترسی به منابع گاز طبیعی و زغالسنگ، در تولید این فلز موثر است. تولید آهن شامل دو مرحله است: آمادهسازی مواد خام و کاهش اکسید آهن به آهن.
آمادهسازی مواد خام برای تولید آهن
آهن یکی از فراوانترین عناصر بر روی زمین است و سنگ معدن آن معمولا حاوی اکسیژن، سیلیکون، منگنز، فسفر و گوگرد است. مواد معدنی اصلی در سنگ آهن شامل «هماتیت» و «مگنتیت» میشوند.
بیشتر سنگ معدنها دارای 60 درصد آهن هستند که در کورههای بلند مورد استفاده قرار میگیرند. سنگ معدنهایی که کمتر از این مقدار آهن داشته باشند را ابتدا پودر میکنند و غلظت آهن در دانههای حاصل را به کمک فرآیند «فلوتاسیون» (Flotation) افزایش میدهند. بعد از این مرحله، دانهها را به گلولههایی تبدیل میکنند و با حرارت دادن در کوره، دانهبندی مناسب را ایجاد میکنند. این عملیات در نزدیکی معادن صورت میگیرد که موجب کاهش فاصله انتقال ضایعات خواهد بود.
از کُک به دو منظور استفاده میشود. این جامد متخلخل، هم کربن مورد نیاز برای واکنشهای کاهشی را تامین میکند و هم به عنوان سوخت رایج کورهها از آن بهره میگیرند. برای تولید آن، زغالسنگ را تا دمای 1200 کلوین در غیاب اکسیژن و به مدت ۲۰ ساعت حرارت میدهند. رسوب حاصل حاوی کک خواهد بود و ترکیبات فرار نیز از آن جدا میشوند. مواد دیگری همچون گاز زغالسنگ (حاوی مونواکسید کربن و هیدروژن)، قیر و بنزن نیز از این روش بدست خواهند آمد. گاز زغالسنگ در محل به عنوان سوخت، مورد استفاده قرار میگیرد.
به اکسیژن برای سوزاندن سوخت و همچنین انجام واکنشهای کوره نیاز است. برای اینکه دمای کوره کاهش پیدا نکند، اکسیژن از طریق لولههایی به داخل کوره دمیده میشود. بسیاری از کورههای امروزی از هوای غنی شده با اکسیژن استفاده میکنند تا واکنشهای داخل کوره به طور کامل انجام شوند.
در برخی کورهها، روغن یا گاز طبیعی به همراه هوای گرم به داخل کوره تزریق میشوند. این کار، کاهش مصرف ۴۰ درصدی کک را به همراه خواهد داشت و وابستگی به زغالسنگ را کاهش میدهد که همین امر در کاهش تولید «محصولات جانبی» (by-Product) در کورههای کک خواهد بود. در حقیقت، هر قدر این محصولات جانبی کمتر تولید شوند بهتر خواهد بود زیرا فروش آنها دشوار است. به عنوان یک راه جایگزین، زغالسنگ پودر شده را به طور مستقیم به کوره وارد میکنند که با این روش، دیگر نیازی به استفاده از کورههای کک نخواهد بود. برخی کارخانجات هم از ضایعات پلاستیک و چوب به عنوان سوخت استفاده میکنند.
کاهش اکسید آهن به آهن
کورههای بلند بخشی از سازههای بزرگ مهندسی هستند. قسمتی از آنها شامل یک استوانه (سیلندر) فولادی با ارتفاع 30 متر است که با آجرهای نسوز پوشیده شدهاند. این کورهها همچنین توسط آب خنک میشوند. از نکات مثبت در این کورهها، قطر ۱۸ متری آنها است. این کورهها به طور معمول تا ۱۵ سال و تحت فشار ۵ اتمسفر و دمای 1726 درجه سانتیگراد نیز به کار خود ادامه میدهند. میزان تولید آهن مذاب از این کورههای بلند به 10 هزار تن در روز میرسد یعنی در طول عمر خود حدود 50 میلیون تن از این فلز تولید میکنند.
کورههای بلند از سنگ آهن با خلوص بالا یا پودر آهن شامل کک و سنگ آهن استفاده میکنند. در کورههای جدیدتر، جرم هر جزء و مدت زمان اضافه شدن آن به کوره توسط کامپیوترها کنترل میشود که این کار را به طور خودکار و با در نظر گرفتن شرایط کوره انجام میدهند. این اجزا را هر 10-15 دقیقه به بالای کوره اضافه میکنند. فشاری در حدود 1/7 اتمسفر در کوره اعمال میشود تا سوختن کک و دیگر سوختها بازده بهتری داشته باشند.
هوای غنی از اکسیژن از پایین به داخل کوره دمیده میشود. با بالا رفتن گازها در کوره، واکنشها نیز انجام میشوند. کک با اکسیژن موجود در کوره واکنش میدهد و تولید کاهندهای به نام مونو اکسید کربن میکند:
اگر از روغن یا گاز طبیعی استفاده شود، این هیدروکربنها کاهنده دیگری با نام هیدروژن تولید میکنند:
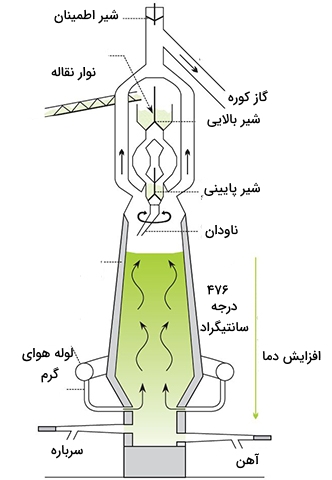
دما در قسمتهای مختلف کوره تغییر میکند و مقدار ثابتی ندارد. بیشترین دما در پایین آن و کمترین دما در بالای کوره دیده میشود. بنابراین، واکنشهای متفاوتی در بخشهای مختلف کوره انجام خواهند شد. در نزدیکی بالای کوره و در دمای 476 درجه سانتیگراد - که دمایی کمتر از نقطه ذوب این فلز است - ترکیبات آهن (III) به آهن (II) کاهش مییابند. این کاهش، به کمک عوامل کاهنده همچون مونواکسید کربن و هیدروژن صورت میگیرد. به طور مثال، به کاهش پیدا میکند. در پایین کوره که دما بیشتر است، واکنش کاهش آهن به طور کامل انجام میشود. واکنشهای کلی برای کاهش آهن در زیر آورده شدهاند:
آهن مذاب در انتهای کوره جمع خواهد شد. به هنگام جمع شدن آهن مذاب و حرکت آن از بالا به پایین، مواد دیگری همچون کربن، فسفر، گوگرد و سایر عناصر مانند منیزیم، سیلیکون، کک و آهک به آن جذب میشوند. در مناطقی از کوره که دما به بیش از 876 درجه سانتیگراد میرسد، آهک به کلسیم اکسید تبدیل خواهد شد:
از آنجایی که کلسیم اکسید یک باز است، با ناخالصیهای اسیدی سنگ معدن واکنش میدهد و سرباره آلومینوسیلیکات را تشکیل میدهد. این فرآیند، همچنین سبب جذب بیشتر گوگرد موجود در مواد خام میشود. این سرباره مذاب از بالا به پایین کوره حرکت میکند و لایهای را در بالای آهن مذاب تشکیل میدهد. آهن مذاب با خلوص 90-95 درصد به همراه سرباره از پایین کوره خارج میشود. به طور معمول، آهن مذاب را مستقیم در ظرفهای 300 تنی به خط تولید فولاد منتقل میکنند.
با خروج سرباره و سرد کردن آن، این ماده با فرآوری به سیمان و محصولات عایق تبدیل خواهد شد. همچنین از آن میتوان در راهسازی استفاده کرد. گازی که در بالای کورهها جمع میشود حاوی نیتروژن، مونو اکسید کربن، دیاکسید کربن، بخار آب و گرد و غبار است. بعد از جداسازی گرد و غبار، مخلوط گاز حاصل با گاز طبیعی را برای گرم کردن آجرهای نسوز کوره مورد استفاده قرار میدهند.
با گرم شدن آجرهای نسوز میتوان از آن برای گرم کردن هوای کوره استفاده کرد. در نهایت، این روش به همراه بکارگیری روشهای زیر، صرفه اقتصادی زیادی را به همراه خواهد داشت:
- استفاده از هوا با اکسیژن غنی
- بکارگیری هیدروکربنها به عنوان سوخت جایگزین
- افزایش فشار عملیاتی کورهها
- کاهش استفاده از آهک (کلسیم کربنات)
- آمادهسازی سنگ آهن قبل از ورود به کوره برای افزایش سرعت واکنش
حذف گوگرد از آهن
در تولید فولاد، غلظت بسیار کمی از گوگرد نیاز است چراکه سبب شکنندگی آن خواهد شد. بسیاری از ناخالصیها در تولید فولاد را میتوان به کمک واکنشهای کاهشی حذف کرد اما برای حذف گوگرد از آهن مذاب به صورت اقتصادی، باید قبل از تولید فولاد این کار را انجام داد که با اضافه کردن یک واکنشگر (ریجنت) صورت میگیرد.
به طور معمول از کلسیم کربنات برای این کار استفاده میکنند اما تاثیر بکارگیری منیزیم به مراتب بیشتر است. ریجنت را به کمک گاز نیتروژن به زیر سطح آهن مذاب تزریق میکنند. واکنش آن به صورت زیر خواهد بود:
کافی است تا سرباره تولیدی غنی از گوگرد را به هنگام تشکیل شدن خارج کنیم.
اگر این مطلب برای شما مفید بوده است، آموزشهای زیر نیز به شما پیشنهاد میشوند:
- مجموعه آموزشهای دروس شیمی
- مجموعه آموزشهای مهندسی مواد و معدن
- آموزش استخراج فلزات ۱ (آهن و فولاد)
- تیتانیوم و کاربردهای آن — از صفر تا صد
- آبکاری — به زبان ساده
^^
خدا قوت- جالب بود
خوب بود
چقدر مناسب و بجا است که منبع مقالات داده شود.
سلام، وقت شما بخیر؛
اگر دقت بفرمائيد منبع تمامی مقالات مجله فرادرس در انتهای آنها و بعد از بخش معرفی آموزشها و مطالب مشابه آمده است.
از اینکه همراه مجله فرادرس هستید از شما بسیار سپاسگزاریم.