تقطیر جز به جز – از صفر تا صد
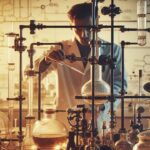
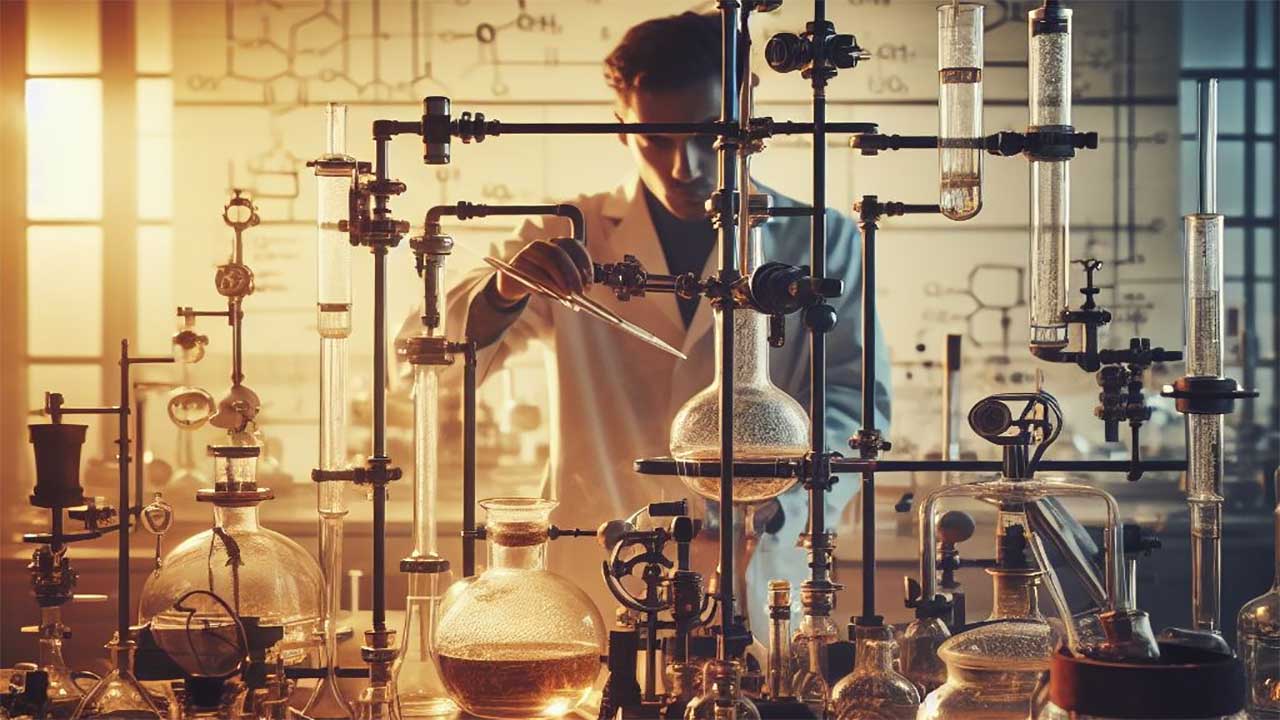
تقطیر جز به جز به جداسازی یک مخلوط به اجزای مختلف (برش) میگویند. ترکیبات شیمیایی را حرارت میدهند تا به دمایی برسند که یک یا چند «برش» (Fraction) از ماده تبخیر شود. در حقیقت، اجزای ماده شیمیایی مورد نظر، نقطه جوشی دارند که اختلاف نقطه جوش این اجزا از یکدیگر، کمتر از ۲۵ درجه سانتیگراد است. اگر این اختلاف، بیش از ۲۵ درجه سانتیگراد باشد، استفاده از یک تقطیر ساده کفایت میکند.
تقطیر جز به جز برای خالصسازی مواد شیمیایی و جداسازی اجزای مختلف یک ماده شیمیایی مورد استفاده قرار میگیرد. از تقطیر جز به جز در صنعت و آزمایشگاه بهره میگیرند. این روش، مزایای اقتصادی فراوانی دارد به طوریکه صنایع نفتی و شیمیایی، همگی برای تولیدات خود و فروش آنها، بر این روش تکیه دارند.
تئوری آزمایش تقطیر جز به جز
بخارهای حاصل از یک محلول در حال جوشیدن، از یک ستون مرتفع موسوم به «برج تقطیر» (Fractionating Column) عبور میکنند. این ستون از گلولههای پلاستیکی یا شیشهای پر شده است تا با افزایش سطح، امکان میعان و تبخیر بیشتر را فراهم کند. دمای این ستون در طول آن به ترتیب کاهش مییابد و اجزا با نقطه جوش بیشتر، در ستون، مایع و دوباره به محلول وارد میشوند. اجزایی که نقطه جوش کمتری دارند، فرارتر هستند و با گذر از ستون، در محلی جمعآوری میشوند.
به عبارت سادهتر، هرقدر گازها به طرف بالای ستون (برج) تقطیر حرکت کنند، دما کاهش پیدا میکند. با کاهش دما، اجزای ماده شیمیایی، در سطوح مختلفی، مایع و جمعآوری میشوند. به طور کلی، هرقدر مقدار گلولهها بیشتر باشد، تقطیر بهتری خواهیم داشت. البته اضافه کردن گلولهها یا سینی (بشقابک) به ستون تقطیر، زمان و انرژی مورد نیاز برای فرآیند تقطیر جزء به جزء را افزایش میدهد. فرآیند تقطیر جز به جز فرآیندی ساده اما قدرتمند است چراکه میتواند تمامی ترکیبات مختلف و پیچیده نفت خام را از یکدیگر جدا کند.
در حقیقت، به کمک یک تقطیر ساده نمیتوان موادی که نقطه جوش نزدیکی دارند را از یکدیگر جدا کرد. همانطور که در بالا هم به آن اشاره شد، زمانی که اختلاف نقطه جوش مواد، زیر ۲۵ درجه باشد، از تقطیر جز به جز استفاده میکنیم. استفاده از یک ستون تقطیر سبب میشود تا بسیاری از فرآیندهای تقطیر به یکباره انجام شوند و نیاز به تغییر ساختار دستگاه آزمایش هم نباشد. ستونهای تقطیر، انواع مختلفی دارند که داخل آنها با موادی پر شده است.
مواد داخل ستون تقطیر، سطح تماسی دارند که بخارات در تماس با آنها مایع میشوند. گرمای فرآیند تقطیر نیز مجددا قطرات مایع را تبخیر میکند. هرکدام از فرآیندهای تبخیر و میعان، همچون یک تقطیر ساده عمل میکنند و هر کدام از مواد که نقطه جوش کمتری داشته باشند، زودتر تقطیر میشوند.
مفهوم تقطیر جز به جز را میتوان به کمک نمودار تقطیر نشان داد. یکی از این نمودارها، در تصویر زیر دیده میشود. در تقطیر یک مخلوط دو جزئی ، با تعداد مول برابر، یکی از رویدادهای تبخیر-میعان به کمک نقاط a تا c نشان داده شده است. این فرآیند نشاندهنده یک «سینی نظری» (Theoretical Plate) و تقطیر آن ۸۱ درصد و ۱۹ درصد بدست میدهد. در این نمودار، رویداد تقطیر و میعان دیگری نیز مشاهده میشود که از نقطه c شروع و به نقطه d ختم شده است که تقطیری با 96 درصد و 4 درصد تولید میکند.
شرح آزمایش تقطیر جز به جز
همانطور که گفته شد، زمانی که اختلاف نقطه جوش اجزای مختلف یک ماده از یکدیگر کم باشند، از تقطیر جز به جز استفاده میشود. برای انجام این روش در آزمایشگاه، به یک چراغ بونزن، یک بالون تهگرد، یک «کندانسور» (Condenser) و یک ستون تقطیر نیاز داریم.
به عنوان نمونه، تقطیر مخلوطی از آب و اتانول را در نظر بگیرید. اتانول در دمای 78/4 درجه سانتیگراد میجوشد درحالیکه نقطه جوش آب ۱۰۰ درجه است. بنابراین، با حرارتدادن مخلوط، جزء فرارتر (اتانول) شروع به تبخیر میکند. در اینجا لازم به ذکر است که بگوییم برخی مخلوطها به هنگام اختلاط، «آزئوتروپها» (Azeotropes) را تشکیل میدهند. این نوع از مخلوطها در دمای پایینتری نسبت به هر جزء میجوشند.
در این مثال، مخلوطی از ۹۶ درصد اتانول و ۴ درصد آب، در دمای 78/2 درجه سانتیگراد به نقطه جوش خود میرسد که پایینتر از نقطه جوش آب و اتانول است. به همین دلیل، اتانول را نمیتوان به صورت کامل و از طریق تقطیر جز به جز خالصسازی کرد. به طور معمول، دستگاه تقطیر جز به جز در آزمایشگاه، شامل یک لوله شیشهای است که داخل آن اشکال مارپیچی به قطر ۴-۷ میلیمتر وجود دارد. این ستون را میتوان به کمک تقطیر جز به جز یک ماده مشخص، کالیبره کرد.
ستونهای تقطیر جز به جز
اینکه از چه نوع ستون تقطیر استفاده کنیم، به نوع دسترسی و آزمایش بستگی دارد. ستونهای مختلفی در تصویر زیر نشان داده شدهاند: یک ستون شیشهای «دندانهدار» (Vigreux)، ستونی شامل الیاف فولادی (سیم ظرفشویی) و ستونی پر شده با گلولههای شیشهای. این ستونها هرکدام دارای سطوح و تعداد «سینیهای نظری» (Theoretical Plates) متفاوتی هستند. در نتیجه، هرکدام قابلیتهای مختلفی برای جداسازی مواد دارند. حتی مقدار مادهای که در بخش مرطوب این ستونها جمعآوری میشود نیز با یکدیگر تفاوت دارند.
کمترین مساحت، مربوط به ستون دندانهدار است و بنابراین کمترین قابلیت را برای جداسازی مواد با نقطه جوش نزدیک به هم دارد اما به دلیل همین مساحت کم، بیشترین بازیافت را خواهد داشت. بنابراین، در مواردی که جداسازی، دشوار نباشد میتوان از این ستون استفاده کرد. ستونهای پرشده، بیشترین سطح تماس را دارند و برای جداسازی مواد با نقطه جوش نزدیک به هم کاربرد دارند. با توجه به سطح تماس زیاد در این ستون، هدررفت زیادی را برای ماده مورد نظر خواهیم داشت.
ستونهای شامل الیاف فولاد یا آهن، سطح تماس متوسطی دارند و بازده آنها به این بستگی دارد که چقدر از الیاف آهن یا فولاد را در ستون پر کردهایم. از ستونهای شامل الیاف آهن نمیتوان در جداسازی مواد خورنده همچون اسیدها بهره برد.
خالصسازی واکنشدهندهها و فرآوردهها
«سیکلوپنتادین» (Cyclopentadiene) در بسیاری از واکنشهای شیمیایی شامل واکنشهای «دیلز-آلدر» (Diels-Alder Reactions) و فرآیندهای پلیمریزاسیون استفاده میشود. این واکنشگر (ریجنت)، بسیار فعال است و تحت یک واکنش دیلز-آلدر، در ظرف خود به «دیسیکلوپنتادین» (Dicyclopentadiene) تبدیل خواهد شد. بنابراین، کارخانههای شیمیایی هیچگاه سیکلوپنتادین را به فروش نمیرسانند و شیمیدانها با تقطیر دیسیکلوپنتادین به سیکلو پنتادین میرسند.
در دمای بالاتر از ۱۵۰ درجه سانتیگراد، دیمر تحت یک واکنش معکوس دیلز-آلدر، به مونومر تبدیل میشود که این مونومر ایجاد شده را میتوان به کمک تقطیر، جداسازی کرد. با وجود اینکه دو جزء مونومر و دیمر، نقطه جوش متفاوتی دارند، اما دمای مورد نیاز برای واکنش معکوس، به نقطه جوش دیسیکلوپنتادین بسیار نزدیک است و نمیتوان فشار بخار آن را نادیده گرفت. بنابراین، از تقطیر جز به جز در این فرآیند استفاده میشود.
مراحل تقطیر جز به جز
در تصویر زیر، یک دستگاه تقطیر جز به جز را میبینید که ستون آن از گلولههای شیشهای پر شده است. در ادامه قصد داریم تا مراحل انجام یک تقطیر جز به جز را به طور دقیق بررسی کنیم.
- درصورتیکه از ستون پر شده استفاده میکنید، میتوان در بالای ستون از پشم شیشه بهره گرفت تا این گلولهها به خوبی در جای خود محکم شوند. البته لازم است تا قبل از استفاده و جلوگیری از انجام واکنش، پشم شیشه را از ستون خارج کنیم. اگر از ستون دندانهدار استفاده میکنید، از سلامت این ستون و عدم شکستگی دندانهها اطمینان حاصل کنید.
- از آنجایی که بخار مایع باید فاصله زیادی را در ستون تقطیر طی کند، در نتیجه برای جلوگیری از میعان زودهنگام آن، باید با شدت بیشتری، ظرف تقطیر را حرارت داد. به عنوان یک قانون سرانگشتی، ظرف تقطیر باید ۳۰ درجه سانتیگراد گرمتر از بالای ستون باشد تا مواد از داخل ستون به طرف بالا حرکت کنند. درصورتیکه این شرایط امکانپذیر نباشد، بهتر است که با پشم شیشه و فویل آلومینیومی، ستون را عایق کنید. این کار سبب میشود تا ستون، گرم بماند و نمونه، مدت زمان بیشتری به حالت گاز باشد.
- در حالت ایدهآل، هر دو شکل مایع و گاز را باید در ستون تقطیر مشاهده کرد. چراکه نمونه متحمل فرآیندهای مختلف تبخیر و میعان میشود. قطرات مایع در سطوح مواد پرشده قابل مشاهده هستند اما مقدار آنها نباید زیاد باشد. اگر ستون تقطیر جز به جز از قطرات مایع پر شد، حرارت دادن را متوقف و صبر کنید تا قطرات مایع به داخل ظرف برگردند و پس از آن، دوباره ظرف را حرارت دهید.
- برای تمیز کردن سطوح تقطیر به روش زیر عمل کنید:
-
- ستون دندانهدار: با استون شستشو دهید. از برسهای شیشهشو استفاده نکنید زیرا ممکن است سبب شکستن دندانهها شوند.
- ستون الیاف فولاد: با مقادیر زیادی از استون، ستون را شستشو دهید. توجه داشته باشید که ستون را با آب شستشو نکنید چراکه به مرور زمان موجب خوردگی الیاف فولاد میشود.
- ستون پرشده: ستون را با استون شسشتو دهید و پس از آن، برای جلوگیری از بیرون افتادن گلولهها، از پشم شیشه استفاده کنید. در روشی دیگر میتوانید گلولهها را از ستون خارج کنید و آنها را به طور جداگانه شستشو دهید. هنگام شستشوی ستونها با شیشهشوی، احتیاط کنید چون لبههای این ستونها شکننده هستند.
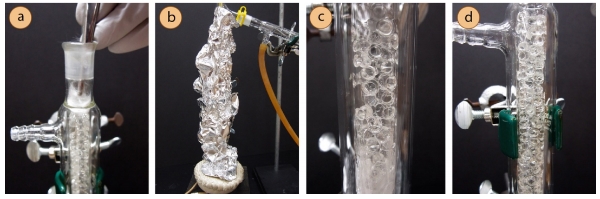
تقطیر در صنعت
تقطیر جز به جز از معمولترین روشهای جداسازی در پالایشگاههای نفت، پتروشیمی، واحدهای فرآوری گاز طبیعی و سایر کارخانههای مواد شیمیایی است. در بیشتر حالات، تقطیر را در «شرایط پایدار» (Steady State) انجام میدهند. همواره خوراک تازه به ستون (برج) تقطیر اضافه و فرآورده از آن خارج میشود.
مراحل تقطیر جز به جز نفت خام
نفت خام شامل بسیاری از هیدروکربنها همچون آلکانها و آروماتیکها و همچنین مخلوطی از ترکیباتی تا ۴۰ اتم کربن است. از این ترکیبات در تهیه سوخت و روانکنندهها بهره میگیرند اما تا زمانی که با یکدیگر مخلوط باشند، کاربردی ندارند. در این موارد از تقطیر جزء به جزء استفاده میشود تا این مخلوطهای پیچیده را با نقطه جوش، جرم مولکولی و خواص نزدیک به هم، بتوان از یکدیگر جدا کرد. بنزین، گازوئیل، کروژن و سوخت هواپیما از جمله برشهای نفتی حاصل از تقطیر جز به جز نفت خام است.
بنزین و بسیاری از ترکیبات شیمیایی دیگر را به کمک تقطیر جز به جز نفت خام بدست میآورند. تا زمانی که فرآیند تغییری نکند، یعنی تغییرات خوراک، حرارت، دمای محیط یا میعان نداشته باشیم، مقدار خوراک ورودی و فرآورده خروجی برابر خواهند بود. به این نوع از تقطیر، «تقطیر جز به جز پیوسته و پایدار» (Continuous Steady-State Fractional Distillation) میگویند.
تقطیر جز به جز به صورت صنعتی معمولا در ستونهای استوانهای عمودی موسوم به «برج تقطیر» یا «ستون تقطیر» انجام میشود. قطر این برجهای تقطیر بین 0/65 تا 6 متر و ارتفاع آن از 6 تا ۶۰ متر متغیر است. برجهای تقطیر، مایعات خروجی را در فاصلههای مختلفی از بالای برج تقطیر تخلیه میکنند که به کمک آن، برشهای مختلف فرآورده با نقطه جوشهای مختلف بدست میآیند. با افزایش دمای فرآورده در داخل ستون، برشهای مختلف از یکدیگر جدا خواهند شد. سبکترین فرآورده، با کمترین نقطه جوش، از بالای ستون و سنگینترین آن با بیشترین نقطه جوش از پایین خارج خواهد شد.
به طور مثال، از تقطیر جز به جز در پالایشگاههای نفت خام استفاده میشود تا نفت خام را به برشهای مختلف هیدروکربنی با نقطه جوشهای متفاوت تبدیل کنند. برشهای نفت خام با نقطه جوش بالاتر، دارای ویژگیهای زیر هستند:
- اتمهای کربن بیشتری را شامل میشوند.
- جرم مولکولی بیشتری دارند.
- بیشتر، از آلکانهای راستزنجیر تشکیل شدهاند.
- رنگ تیرهتری دارند.
- ویسکوزتر هستند.
- سوزاندن آنها دشوارتر است.
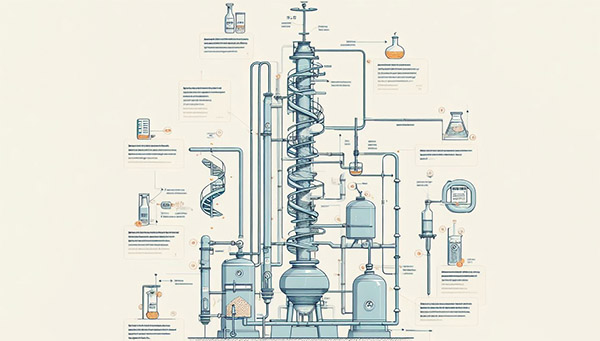
جریان برگشتی
برجهای تقطیر صنعتی با مقیاس بزرگ، از «فرآیند بازگشتی» (Reflux) استفاده میکنند تا جدایش برشهای مختلف، کاملتر انجام شود. جریان برگشتی (رفلاکس) به بخشی از مایع سرد شده میگویند که بعد از فرآیند تقطیر، به طور مجدد به قسمت قوقانی برج تقطیر بازگردانده میشود. در داخل برج، مایع رفلاکس، با حرکت به سمت پایین و گذر از سینیهای تقطیر، بازده برج تقطیر را بالا میبرد. به همین دلیل، هرقدر برای یک تقطیر، از رفلاکس بیشتری استفاده کنیم، به سینی (بشقابک) کمتری نیاز خواهیم داشت.
تقطیر جز به جز در سایر موارد صنعتی
از تقطیر جز به جز در جداسازی هوا و تولید اکسیژن و نیتروژن مایع (هوای مایع) و همچنین آرگون تغلیظ شده بهره میگیرند. علاوه بر این، از تقطیر «کلروسیلانها» (Chlorosilanes) میتوان به سیلیکون با خلوص بسیار بالا دستیافت که از آن در ساخت ابررساناها استفاده میشود. کلروسیلانها گروهی فعال از ترکیبات شیمیایی حاوی کلر هستند که در آنها حداقل یک پیوند سیلیکون-کلر وجود دارد.
در برخی مصارف صنعتی، به جای استفاده از از سینیهای تقطیر، از ستونهای «پرشده» (Packing) ویژهای استفاده میکنند. استفاده از ستونهای پرشده، مخصوصا زمانی اهمیت دارد که نیاز به افت فشاری در طول ستون تقطیر یا شرایط عملیاتی تحت خلأ داشته باشیم. مایعات، موجب تر شدن سطوح مواد پر شده میشوند و بخارهای حاصل از تبخیر، از میان این سطوح مرطوب گذر میکنند و این همانجایی است که انتقال جرم صورت میگیرد.
برخلاف سینیهای تقطیر که در آن، هر سینی، نقطهای مجزا از تعادل بخار-مایع را دارد، نمودار تعادل بخار-مایع در ستون حاوی این مواد فشرده (بستهها)، به صورت پیوسته است. البته به هنگام شبیهسازی این فرآیندها بهتر است که تعداد نظری سینیها محاسبه شود تا بتوان بازده تقطیر به کمک این دو روش را تحلیل کرد. این بستهها هرکدام شکل و سطح متفاوتی دارند که به تبع آن دارای فضاهای خالی بین خود نیز هستند. این دو عامل، بر عملکرد بستهها تاثیرگذارند.
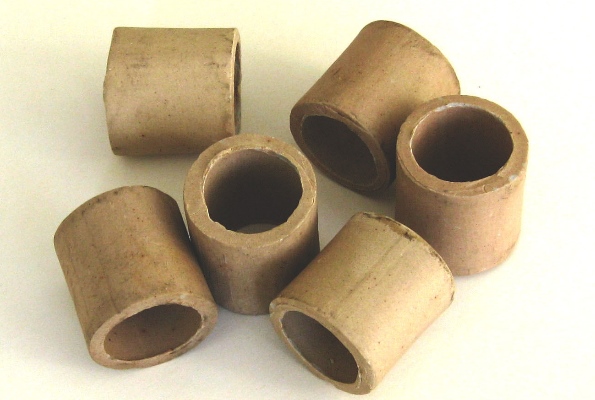
طراحی ستونهای تقطیر صنعتی
طراحی و عملیات یک ستون تقطیر، به خوراک و مواد فرآورده وابسته است. اگر خوراک ورودی، یک سیستم دو جزئی باشد، میتوان از «روش مککیب-تیل» (McCabe–Thiele Method) یا «معادله فنسک» (Fenske Equation) استفاده کرد. برای خوراک چندجزئی، از مدلهای شبیهسازی در طراحی و عملیات بهره میگیرند.
علاوه بر این، بازده سطوح تماسی بخار-مایع یا همان سینیها، عموما کمتر از بازده نظری آنها است. بنابراین، یک ستون تقطیر، بیش از تعداد نظری محاسبه شده، به سینیها نیاز دارد. همانطور که بالاتر نیز به آن اشاره شد، وجود رفلاکس، موجب تراکم و میعان بخارهای بالارونده در ستون میشود. «نسبت رفلاکس» (Reflux Ratio) که نسبت رفلاکس داخلی به فرآورده بالای برج است، به طور معکوس با تعداد مراحل نظری برای تقطیر پربازده تناسب دارد.
طراحی برجهای تقطیر بمنظور دستیابی به بازده مناسب در جداسازی مواد انجام میشود و به طور معمول شامل دو مرحله است: «طراحی فرآیند» (Process Design) و «طراحی مکانیکی» (Mechanical Design).
هدف طراحی فرآیند، محاسبه تعداد نظری مراحل و جریانهای برج تقطیر شامل پارامترهای مختلف رفلاکس است. هدف طراحی مکانیکی، تعیین پارامترهای برج همچون ارتفاع و قطر ستون را شامل میشود. در بسیاری از موارد، طراحی مکانیکی برج تقطیر به صورت مستقیم انجام نمیگیرد. برای طراحی مناسب بخشهای داخلی برج و محاسبه دقیق ستون تقطیر و قطر آن، عوامل متعددی را باید مد نظر قرار داد. از جمله این عوامل میتوان به مقدار خوراک ورودی، خواص خوراک و نوع ستون اشاره کرد.
دو نوع متداول ستونهای تقطیر عبارتند از برجهای تقطیر سینیدار و «پرشده» (Packing). از ستون های پر شده در موارد زیر استفاده میشود:
- برجهای تقطیر با طول کوتاه
- خوراک ورودی «خورنده» (Corrosive)
- خوراک ورودی حساس به دما
- شرایطی همچون خلأ که در آن، افت فشار مهم باشد.
در مقابل، از برجهای تقطیر سینیدار در ستونهای بزرگتر با حجم خوراک بیشتر بهره میگیرند. این نوع از برجهای تقطیر در دهه 1820 ظهور کردند. در عملیات فرآوری نفت خام، معمولا از این نوع برجهای تقطیر استفاده میشود تا به کمک آن، برشهای مختلف نفتی بدست آیند. البته طراحی برجهای تقطیر در صنعت نفت، پایهای تجربی دارد و در طراحی آنها، نمودارها، جداول و معادلات پیچیده تجربی بکار میروند. البته در سالهای اخیر، تلاشهایی در خصوص توسعه روشهایی مبتنی بر طراحیهای کامپیوتری صورت گرفته است.
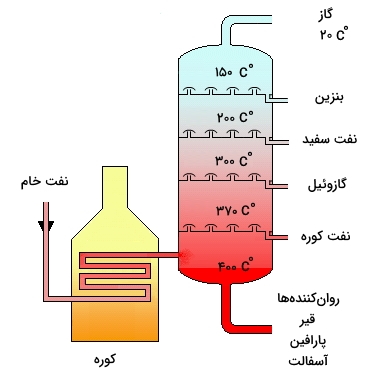
تاثیر ناخالصی در تقطیر جز به جز
لازم به ذکر است، مخلوطی ۵۰/۵۰ از دو جزء که نقطه جوش آنها تنها ۲۰-۳۰ درجه با یکدیگر تفاوت دارند، حداقل به سه سینی نظری نیاز دارد تا تقطیری با خلوص بیش از ۹۵ درصد بدست دهد. در عمل، تقطیر جز به جز همچنان مخلوطهایی تولید میکند. بهترین حالت برای رسیدن به خلوص در تقطیر جز به جز، زمانی است که مقادیر کمی از ناخالصی داشته باشیم.
اگر این مطلب برای شما مفید بوده است، آموزشهای زیر نیز به شما پیشنهاد میشوند:
- مجموعه آموزشهای مهندسی شیمی
- مجموعه آموزشهای طراحی مکانیکی (Mechanical Design)
- آموزش شبیه سازی فرایندهای پالایشگاهی با Aspen HYSYS
- نقطه ذوب و اندازه گیری آن — از صفر تا صد
- غلظت محلول ها — به زبان ساده
^^
با سلام وخسته نباشید ممنون از مطالب اموزنده و خیلی مفیدتون.در رابطه با تصفیه حلالهای صنعتی در چهارچوب صنعت رنگسازی اگر مطلبی باشه ممنون میشم کمکم کنید.با تشکر از زحمات شما
با سلام؛
خوشحالیم که مطالعه این مطلب برای شما مفید بوده است. در حال حاضر، دوره مرتبطی در این رابطه موجود نیست اما میتوانید با مراجعه به آدرس زیر، سایر دورههای مرتبط با مهندسی شیمی را مشاهده کنید.
مجموعه آموزش مهندسی شیمی
با تشکر از همراهی شما با مجله فرادرس
از مشکلاتی که من با آن روبرو هستم مخلوط شدن آب با روغن های نفتی مثل روغن هیدرولیک است.برای جدا سازی آب از روغن هیدرولیک استفاده از خلا بهتر است یا برج تقطیر
متشکرم
عالی بود.
بسیار خوب توضیح دادید و خیلی استفاده کردم.
سپاس.