ریخته گری چیست و انواع روش های ریخته گری چه هستند؟ – جامع و رایگان

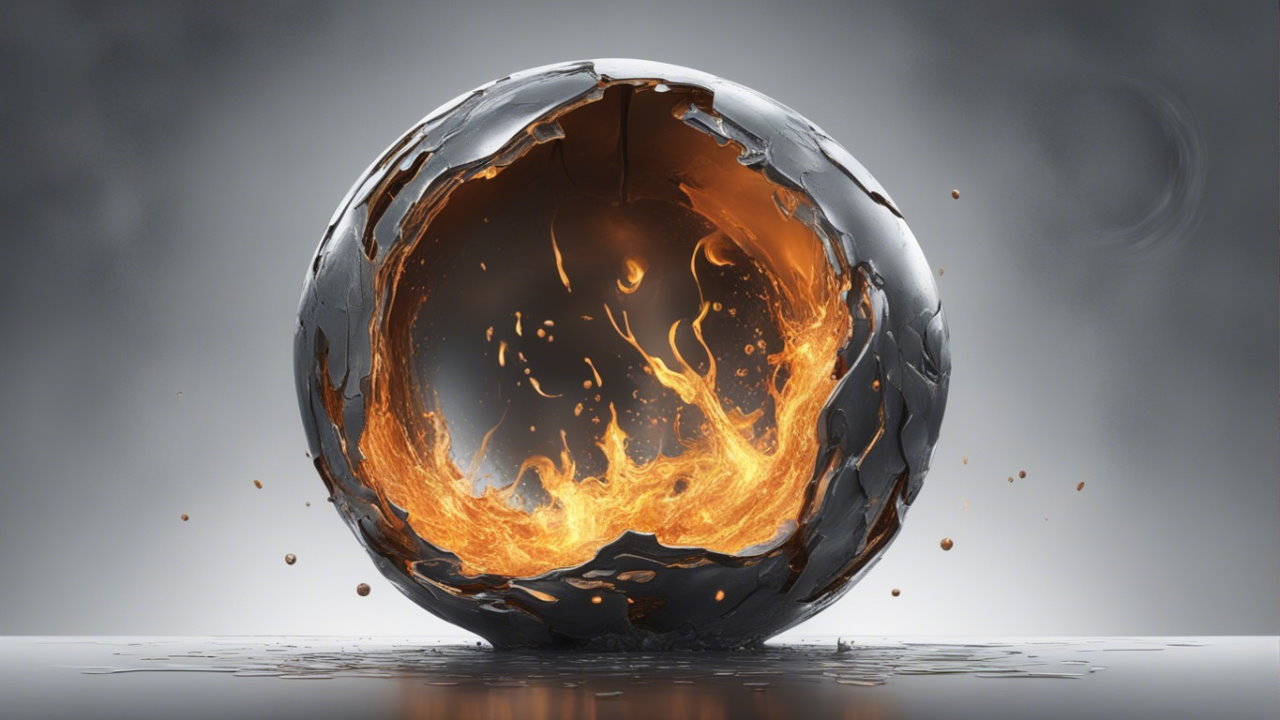
قطعات موجود در وسایل و تجهیزات اطراف ما، با استفاده از فرآیندهای ساخت، تولید میشوند. ساخت برخی از این قطعات، در مقیاسهای کوچک و برخی دیگر، در مقیاسهای بزرگ و صنعتی انجام میگیرد. از شناخته شدهترین روشهای صنعتی ساخت و تولید میتوان به ریختهگری اشاره کرد. ریختهگری، فرآیندی است که به طور گسترده برای تولید قطعات فلزی مورد استفاده قرار میگیرد. این فرآیند از محبوبیت بالایی در صنایع خودروسازی و ماشینسازی برخوردار است. در این مقاله، به معرفی اصول و مفاهیم ریخته گری میپردازیم. در ابتدا، کاربردها، مواد مورد استفاده، انواع روشهای اجرا، روند کلی اجرا، مزایا، معایب و عیوب این فرآیند را مرور میکنیم. سپس، تاریخچه، اصطلاحات رایج و انواع روشهای ریختهگری را مورد بررسی قرار میهیم. در انتها نیز به ارائه برخی از نکات تکمیلی و منابع یادگیری این فرآیند مهم میپردازیم.
روش های ساخت و تولید کدام هستند؟
ساخت و تولید، یک اصطلاح کلی است که به مجموعه فعالیتهای مورد نیاز برای ایجاد یک قطعه در صنایع مختلف اشاره میکند. روشها و فرآیندهای متنوعی برای ایجاد قطعات صنعتی و غیر صنعتی وجود دارند. به عنوان مثال، قطعات پلاستیکی مورد استفاده در بسیاری از تجهیزات، با استفاده از روش قالب گیری تزریقی ساخته میشوند.
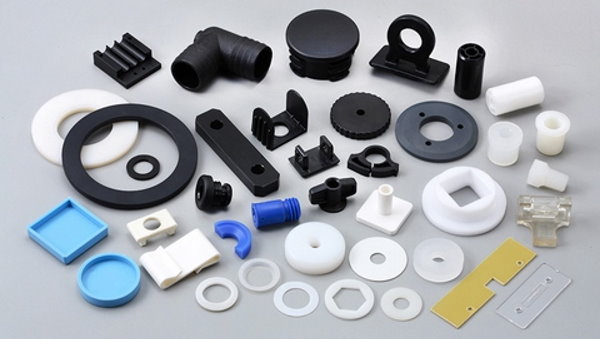
شناختهشدهترین روشهای ساخت و تولید عبارت هستند از:
- ریخته گری
- پوششدهی و حکاکی: حکاکی با لیزر، چاپ، انباشت بخار شیمیایی، لایهنشانی کندوپاش، آبکاری و پاشش حرارتی
- قالب گیری: متالورژی پودر، قالب گیری پلاستیک و پوشش شرینک
- شکل دهی: فرم دهی انتهای لوله، آهنگری، نورد، اکستروژن، پرسکاری، خمکاری، برشکاری و غیره
- ماشین کاری: فرزکاری، تراشکاری، سوراخکاری، خانکشی، هونینگ، برشکاری با لیزر، واتر جت، برش پلاسما، تخلیه الکتریکی، سنگزنی و غیره
- اتصال: جوشکاری، لحیمکاری، تف جوشی، چسبکاری، پیچکاری و غیره
- ساخت افزایشی: چاپ سه بعدی، تف جوشی لیزری انتخابی، رشته پیچی، رشته ذوبی، لایهسازی، تف جوشی با پلاسما، استریولیتوگرافی و غیره
- روشهای دیگر: معدنکاری، تولید شیمیایی، پتروشیمی، مونتاژ، لجستیک، بستهبندی، چوبکاری، عملیات حرارتی (مانند سخت کاری)، پخت و غیره
موارد بالا، به منظور ساخت و تولید قطعات فلزی، پلاستیکی، پلیمری و غیره مورد استفاده قرار میگیرند. روشهای ساخت و تولید میتوانند کاربریهای اختصاصی (یک صنعت و یک ماده خاص) یا عمومی داشته باشند. البته توجه داشته باشید که امکان تقسیمبندیها روشهای ساخت و تولید به گروههای کلیتر نیز وجود دارد. به عنوان مثال، ریختهگری، شکلدهی و اتصال، به عنوان روشهای فلزکاری در نظر گرفته میشوند.
ریخته گری چیست؟
«ریخته گری» (Casting)، یکی از قدیمیترین فرآیندهای ساخت و تولید است که با ذوب مواد و ریختن آنها به درون قالب انجام میگیرد. این فرآیند، از متداولترین روشهای ساخت قطعات فلزی در صنایع مختلف به شمار میرود.
ریختهگری، امکان تولید انبوه قطعاتی با ابعاد کوچک تا بزرگ، وزن چند گرم تا چند تن، شکل ساده تا پیچیده و ساختار یکپارچه را فراهم میکند. روشهای متعددی برای اجرای ریخته گری وجود دارند. با این حال، ریخته گری ماسه ای به عنوان قدیمیترین و رایجترین روش اجرای ریختهگری شناخته میشود.
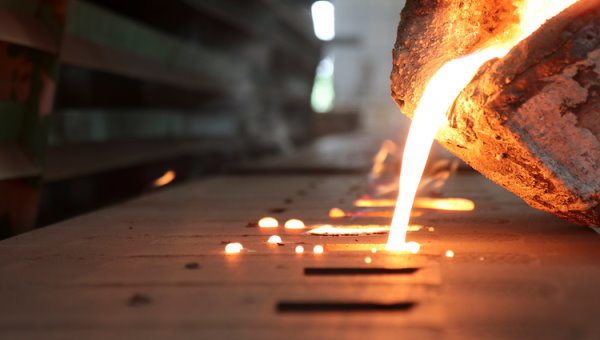
کاربرد ریخته گری چیست؟
ریخته گری، تقریبا در تمام صنایع کاربرد دارد. حدود 90 درصد از محصولات تولید شده در صنایع مختلف و ماشینآلات صنعتی، به نحوی با فرآیندهای ریخته گری در ارتباط هستند. با این وجود، بیش از 50 درصد از قطعات ریخته گری شده در صنایع ساخت ماشینآلات سنگین و تجهیزات حمل و نقل مورد استفاده قرار میگیرند.
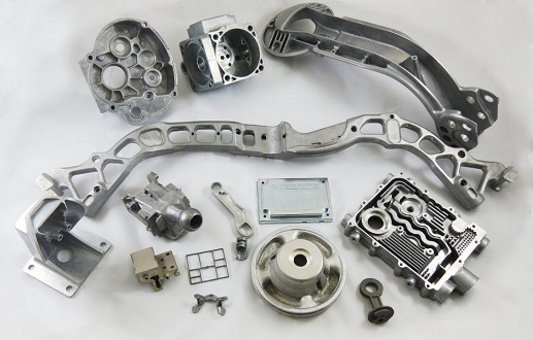
صنایع و حوزههای مختلفی که ریختهگری در آنها کاربرد دارد، عبارت هستند از:
- حمل و نقل: خودروسازی، تجهیزات راهآهن، تجهیزات راهآهن و کشتیسازی
- ماشین آلات سنگین: ماشین آلات راهسازی، کشاورزی و معدنکاری
- ماشین ابزار: تجهیزات ماشینکاری، قالبسازی، آهنگری، اکستروژن، شکلدهی و ریخته گری
- ماشین آلات کارخانه: تجهیزات کارخانههای تولید مواد شیمیایی، پتروشیمی، کاغذسازی، تولید شکر، نساجی، ذوب و نیروگاهها
- صنایع نظامی: خودروها، تسلیحات، مهمات، مخازن و تجهیزات نگهدارنده
- صنایع الکتریکی: موتور، ژنراتور، پمپ و کمپرسور
- تاسیسات: لولهها، اتصالات، ولوها و فیتینگهای مورد استفاده در پایپینگ، تاسیسات بهداشتی و تاسیسات سرمایشی
- لوازم خانگی: وسایل آشپزخانه، مبلمان و تجهیزات باغبانی
- هنر: مجسمهسازی، وسایل زینتی، دکوراسیون و غیره
مواد مورد استفاده در ریخته گری چه هستند؟
چدن خاکستری، پرکاربردترین ماده مورد استفاده در فرآیند ریخته گری است. از دیگر فلزات متداول در این فرآیند میتوان به چدن نشکن، آلومینیوم، فولاد، مس و روی اشاره کرد. البته امکان استفاده از مواد غیر فلزی مانند بتن، شیشه، پلاستیک و رزین نیز برای ساخت قطعات ریختهگری وجود دارد.
انتخاب ماده مناسب برای ساخت قطعات، به پارامترهایی نظیر حجم تولید، صرفه اقتصادی، دمای ذوب، سرعت خنککاری، مقاومت در برابر فرسودگی، وزن و قابلیت جذب ارتعاش بستگی دارد. نوع ماده مورد استفاده، یکی از معیارهای تقسیمبندی انواع روش های ریخته گری و کاربردهای آنها است.
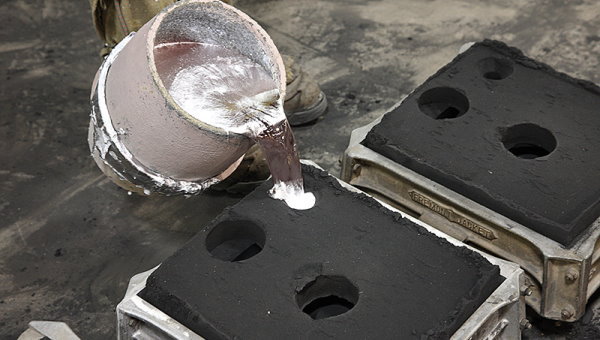
کارخانه ذوب یا کارخانه ریخته گری چیست؟
کارخانه ریخته گری یا «کارخانه ذوب» (Foundry)، محل تولید قطعات فلزی به روش ریختهگری است. تمامی مراحل اجرای ریختهگری در این انجام میشود. از تجهیزات و مواد مورد استفاده در کارخانه ذوب میتوان به دستگاههای قالبگیری، میکسر، کوره، پاتیل، وسایل انتقال، فیلتر، فلزات، آلیاژها، افزودنیها و سیستمهای پیوند شیمیایی مواد اشاره کرد.
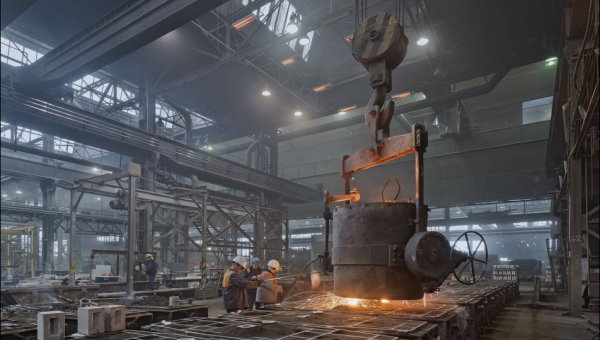
ریخته گری چگونه انجام میشود؟
با وجود روشهای مختلف برای اجرای ریخته گری، این فرآیند، معمولا طی چندین مرحله کلی شامل ساخت الگو، ساخت ماهیچه، ساخت قالب، ذوب کردن فلز، ریختن ماده مذاب به درون قالب، انجماد، باز کردن قالب و پرداخت قطعه انجام میگیرد. فعالیتهای موجود در هر یک از این مراحل عبارت هستند از:
- مدلسازی: طراحی قالب های صنعتی مورد استفاده در فرآیند ریخته گری توسط نرم افزارهای تخصصی و ساخت مدل فیزیکی قطعه نهایی
- ساخت ماهیچه: طراحی و ساخت ماهیچههای مورد نیاز برای ایجاد سطوح داخلی قطعه
- قالب سازی: ساخت قالب ریختهگری با توجه به مستندات طراحی و با استفاده از موادی نظیر ماسه، موم، فولاد و غیره
- ذوب و ریختن: اعمال دمای بالا به فلزات برای تبدیل به حالت مایع و ریختن مواد مذاب به درون قالب توسط بوته یا دیگر تجهیزات موجود
- انجماد: کاهش دمای قالب و مواد مذاب درون آن پس از اتمام فرآیند ریختن
- باز کردن قالب: جدا کردن بخشهای مختلف قالب و خارج کردن قطعه قالب ریخته گری شده
- پرداخت: اجرای برشکاری، سنگزنی، سندبلاست و غیره به منظور جدا کردن بخشهای اضافی قطعه، ایجاد بافت مناسب و یا آمادهسازی سطح آن برای پوششدهی
انواع روش های ریخته گری کدام هستند؟
طبق یک دسته بندی کلی، انواع روش های ریخته گری در دو گروه ریختهگری با قالب یکبار مصرف و ریختهگری با قالب دائمی تقسیم میشوند.
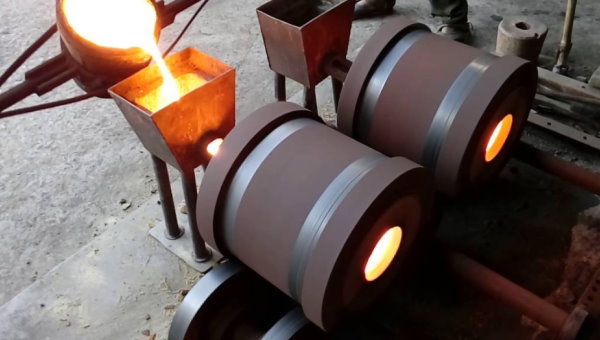
روشهای قابل اجرا با استفاده از قالبهای موقتی و دائمی ریختهگری عبارت هستند از:
- قالبهای یکبار مصرف: ریخته گری در قالبهای موقتی و بدون امکان استفاده مجدد
- ریختهگری ماسه ای
- ریختهگری گچی
- ریختهگری پوسته ای
- ریختهگری دقیق
- ریختهگری الگوی تبخیری
- قالبهای دائمی: ریخته گری در قالبهای چندبار مصرف و بدون نیاز به اعمال تغییر بر روی قالب پس از هر چرخه تولید
- ریختهگری ثقلی
- ریختهگری تحت فشار (دایکاست)
- ریختهگری نیمه جامد
- ریختهگری گریز از مرکز
- ریختهگری پیوسته
در بخشهای بعدی، به معرفی تمام روشهای معرفی شده خواهیم پرداخت.
مزایا و معایب ریخته گری چه هستند؟
از مهمترین مزیتهای ریختهگری نسبت به دیگر روشهای ساخت و تولید میتوان به موارد زیر اشاره کرد:
- امکان ساخت قطعات پیچیده با هزینه نسبتا کم
- عدم تاثیر ابعاد قطعه مورد نظر بر روی فرآیند
- خواص مکانیکی بسیار خوب قطعه نهایی
- امکان ساخت قطعات با جزئیات ریز و دقیق
- عدم وجود محدودیت در مواد قابل استفاده
- ساختار داخلی یکنواخت و همسانگرد قطعه
- صرفه اقتصادی نسبت به دیگر روشهای ساخت
- امکان ساخت قطعات کامپوزیتی (متشکل از چندین ماده)
برخی از محدودیتهای ریختهگری عبارت هستند از:
- پرداخت نسبتا ضعیف سطح و نیاز به انجام پرداخت ثانویه در اغلب موارد
- امکان رخ دادن عیب و نقص در قطعه
- کنترل نسبتا دشوار به دلیل وجود مراحل زیاد
- مقاومت پایین در برابر خستگی نسبت به آهنگری
عیوب ریخته گری چه هستند؟
به مشکلات ایجاد شده در ساختار قطعه طی فرآیند ریختهگری، عیوب ریخته گری میگویند. هر یک از روش های ریخته گری، مستعد رخ دادن عیب و نقصهای مختص به خود هستند. برخی از این عیب و نقصها، کیفیت و عملکرد قطعه را تحت تاثیر قرار میدهند. به همین دلیل، این عیوب، معمولا طی فرآیندهای کنترل کیفیت شناسایی میشوند.
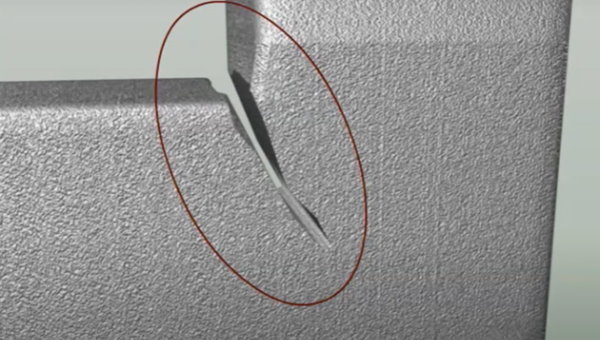
از رایجترین نواقص احتمالی در قطعات ساخته شده به روش ریختهگری میتوان به موارد زیر اشاره کرد:
- عدم انطباق: عدم جانمایی مناسب نیمههای قالب و ماهیچه
- تورم: افزایش ابعاد حفره قالب به دلیل فشار زیاد مواد فشار
- جوشیدن (سوسه و مک): محبوس شدن گاز در سطح قطعه به دلیل فرآیند انجماد
- ماسه ریزی: وجود ترک بر روی سطح بالایی ماسه و اضافه شدن ذرات ماسه به درون فلز مذاب
- نفوذ فلز: سطوح ناهموار و زبر قطعه به دلیل دانهبندی بزرگ ماسه و نفوذ مواد مذاب به درون قالب
- حفرههای کوچک: حفرههای بسیار ریز (حدود 2 میلیمتر) بر روی سطح قطعه به دلیل آزاد شدن گاز هیدروژن از مواد مذاب
- حفرههای انقباضی: ایجاد حفرههای داخلی ناشی از کاهش حجم قطعه در حین انجماد
- اتصال سرد: به جا ماندن اثر خط برخورد مواد مذاب در قالبهای دارای دو مجرای ورودی
- نیامد: انجماد مواد مذاب قبل از پر کردن کامل تمام حفره
- آخال سربارهای: وجود ذرات سرباره درون مواد مذاب
- ترک گرم: شکست کششی ناشی از تنشهای پسماند در مواد مذاب
- سخت ریزه: انجماد سریعتر برخی از نقاط نسبت به مواد اطراف
- ماهیچه ماسهای: حفرههای داخلی یا خارجی ناشی از ورود ذرات سست ماسه به درون حفره قالب یا ریختن سریع مواد مذاب به درون قالب
- لکه: ناهمواری سطح قطعه به دلیل وجود ذرات اضافی بر روی سطح داخلی قالب
- حفرههای شبکهای: ایجاد چندین حفره کوچک و نزدیک به هم در سطح خارجی قطعه
- تابیدگی: تغییر شکل قطعه در حین انجماد یا پس از انجماد به دلیل یکنواخت نبودن نرخ کاهش دمای مواد
- پلیسه: ایجاد لایه نازک
همان طور که مشاهده میکنید، احتمال رخ دادن عیب و نقصهای زیادی در فرآیند ریختهگری وجود دارد. همین موضوع، اهمیت طراحی مناسب، اجرا اصولی و نظارت مداوم بر روی ساخت قطعات توسط این روش را دو چندان میکند.
تاریخچه ریخته گری
آغاز فرآیند ریختهگری، به بیش از 6500 سال پیش باز میگردد. اولین آثار یافت شده از این فرآیند ساخت و تولید مربوط به دوران تمدن بینالنهرین میشود. در آن دوران، ریخته گری طلا، به منظور ساخت قطعات تزئینی و بازیافت فلزات گرانبها مورد استفاده قرار میگرفت. پایین بودن دمای ذوب طلا، این فلز گرانبها را به گزینهای مناسب برای ریختهگری تبدیل میکرد. با گذشت زمان، فلزات دیگر نیز مسیر خود را به این فرآیند پیدا کردند. برنز و آلیاژ قلع از جمله فلزاتی بودند که به منظور ساخت ابزارآلات و تسلیحات به کار گرفته میشدند. البته قدیمیترین قطعه ریختهگری شده باقی مانده از تمدن بینالنهرین، یک مجسمه مسی با قدمت بیش از 5200 سال است.
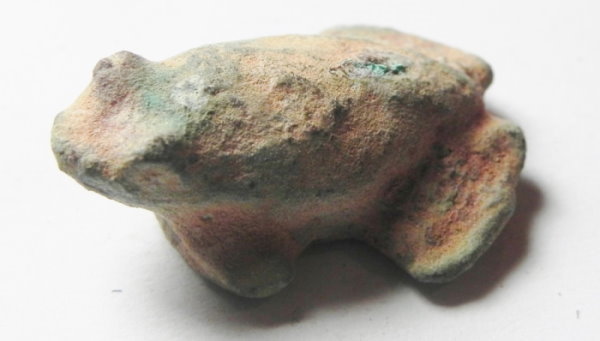
در طی چندین هزار سال، عصر برنز، سراسر کره زمین را فرا گرفت. مصریان، دمنده مخصوصی اختراع کردند که امکان انتقال حرارت به فلزات و رساندن دمای آنها به مقادیر بالاتر از روشهای مرسوم را فراهم میکرد. این ابزارهای ریختهگری، قادر به پمپاٰژ هوای گرم به درون کوره بودند. در عصر برنز، ریخته گری فلزات با پیشرفت قابل توجهی همراه شد. در این دوران، ساخت قطعات فلزی با ریختن مواد مذاب به درون قالبهای سنگی باز صورت میگرفت. به این ترتیب، یکی از سطوح قطعه، همیشه به شکل صاف ساخته میشد. در حدود 4000 سال پیش، روشی برای ساخت حفرههای پیچیده در قالب ریخته گری با استفاده از مواد مومی توسعه یافت. این روش، مشکل قالبهای سنگی باز را برطرف کرد. مسجمههای برنزی جالب توجهی از این دوران باقی مانده است.
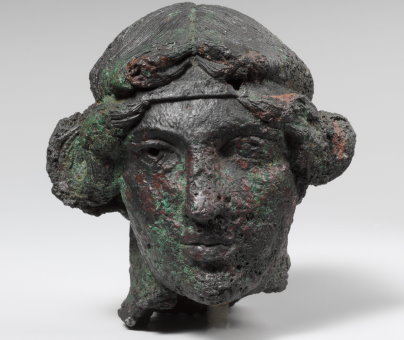
آهن، یک عنصر فلزی است که معمولا به صورت اکسید در طبیعت یافت و استخراج میشود. اولین تلاشهای بشر برای استفاده از آهن در فرآیند ریختهگری به حدود 3700 پیش باز میگردد. بر اساس شواهد موجود، هیتیتیها، از کورههای مخصوص برای استخراج آهن و ریختهگری آن استفاده میکردند. با این وجود، گسترش ریخته گری آهن به قرن 14 میلادی (قرن 8 شمسی) باز میگردد.
آهن خام، یکی از آلیاژهای آهن با درصد کربن بالا است. این آلیاژ، نقطه ذوب پایینتری نسبت به فلز آهن دارد. در قرن 7 میلادی (قرن 1 شمسی)، آهن خام به عنوان یکی از مواد رایج برای ساخت قطعات به روش ریختهگری مورد استفاده قرار میگرفت. چینیها نیز مانند مصریان باستان، از تکنولوژی اعمال حرارت توسط دمنده به منظور دستیابی دمای بالا (حدود 1150 درجه سانتیگراد) برای ذوب آهن خام استفاده میکردند. قطعات ساخته شده به روش ریخته گری آهن خام، از شکنندگی بالایی برخوردار بودند. احتمالا این مشکل، یکی دیگر از دلایل فاصله زمانی زیاد بین معرفی ریختهگری آهن در تمدنهای دیگر و شروع به کارگیری آن در اروپا است.
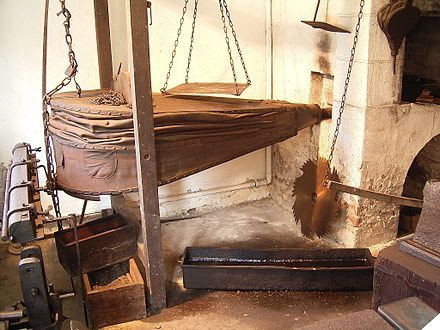
تا پیش از انقلاب صنعتی در قرن 18 میلادی (قرن 12 شمسی)، آهن خام به عنوان اصلیترین ماده مورد استفاده برای ریختهگری در نظر گرفته میشد. دروازههای برخی از کلیساهای قرون وسطی توسط ریختهگری آهن خام ساخته شدهاند. البته کیفیت ساخت این دروازهها پایین بوده و بسیاری از آنها نیازمند ترمیم و تقویت هستند. در قرن 15 میلادی (قرن 9 شمسی)، اولین لولههای چدنی با استفاده به روش ریختهگری ساخته شد.
پس از انقلاب صنعتی، تعداد کارخانههای ذوب در سراسر اروپا و آمریکا به میزان قابل توجهی افزایش یافت. این توسعه، گسترش کاربردهای فرآیند ریختهگری را به همراه داشت. اقبال صنایع مختلف به ریختهگری، باعث پیشرفت روشهای اجرا، تجهیزات و مواد مورد استفاده در این فرآیند ساخت و تولید شد. از ابداعات این دوران میتوان به استفاده از کک متالورژی در کورههای آهنگدازی برای استخراج آهن و اختراع اولین چدن چکشخوار اشاره کرد.
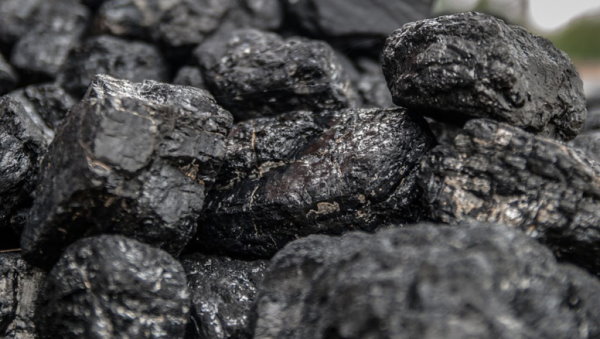
بازه زمانی بین انقلاب صنعتی و شروع قرن 20 میلادی (قرن 14 شمسی) را میتوان به عنوان مهمترین دوره پیشرفت و ترقی صنعت ریخته گری در نظر گرفت. اجرای اولین ریخته گری فولاد با استفاده از بوته های ریختهگری، افتتاح اولین کارخانه تجاری فولاد و توسعه متالوگرافی، از پیشرفتهایی بودند که زمینه تولید انبوه قطعات آهنی و فولادی با کیفیت در سراسر دنیا را فراهم کردند.
در ادامه قرن 20 میلادی، الکتریسیته پا به صنعت ریختهگری گذاشت؛ امکان ساخت قطعات فولاد ضد زنگ فراهم شد و صنعت خودروسازی نیز در اروپا، آمریکا و ژاپن توسعه یافت. جنگ جهانی دوم، شکل صنعت فلزات را تغییر داد. در آن دوران، بسیاری از کشورهای درگیر، مشغول بازسازی سازههای خود بودند. بهرهگیری از منابع انرژی جدید به همراه اصول مدیریتی ژاپنیها نظیر شش سیگما، کانبان و تولید به هنگام، مسیر دستیابی به تولید ناب را هموار کرد.
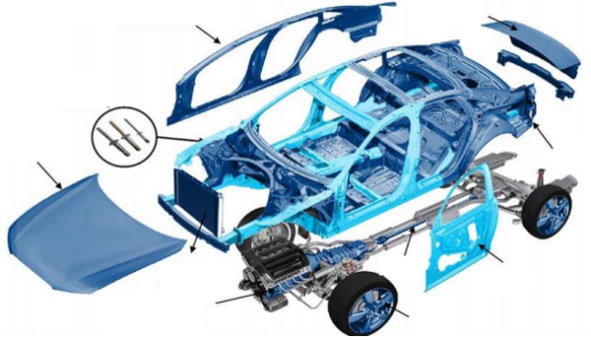
در دهههای اخیر، بسیاری از صنایع در تلاش بودهاند تا سازگاری فرآیندهای ریختهگری با مسائل محیط زیستی را افزایش دهد. همین مسئله باعث توسعه ریختهگری الکترومغناطیس در سال 1997 میلادی (1376 شمسی) شد. این روش، هزینه و ردپای کربن در فرآیند ریختهگری را به میزان قابل توجهی کاهش داد. امروزه، تمرکز اصلی صنعتگران بر روی اختراع روشهای جدید، ارزان و پاک در ساخت قطعات فلزی توسط ریختهگری است.
اصطلاحات ریخته گری
ریخته گری، یکی از متداولترین روشهای ساخت و تولید است که طی چندین مرحله و با استفاده از ابزارهای متنوع اجرا میشود. یادگیری اصطلاحات رایج ریخته گری، امکان درک بهتر مکانیزم اجرای این فرآیند را فراهم میکند. برخی از این اصطلاحات عبارت هستند از:
- اصطلاحات مربوط به ابزارهای ریختهگری
- قالب
- حفره
- سیستم راهگاهی
- قطعه
- ماسه ریخته گری
- ماسه رویه
- ماسه رزینی
- فلاسک
- کوپ و درگ
- چیک
- مدل
- ماهیچه
- چپلت
- چیل
- بوته
- پاتیل
- اصطلاحات مربوط به سیستم راهگاهی درون قالب
- حوضچه
- بارریز
- اسپرو
- چشمه
- رانر
- گیت
- رایزر
- غلاف
- هواکش
در ادامه به معرفی هر یک از اصطلاحات بالا میپردازیم.
قالب ریخته گری
«قالب» (Mold یا Mould)، ابزاری است که به منظور شکلدهی به فلز مذاب مورد استفاده قرار میگیرد. قالب ریختهگری تحت فشار با اصطلاح «دای» (Die) شناخته میشود.
طراحی قالب های صنعتی مورد استفاده از فعالیتهای بسیار مهم در فرآیند ریختهگری به شمار میرود؛ چراکه تمامی بخشهای موجود در قالب، بر روی کیفیت قطعه ریخته گری شده تاثیر میگذارند.
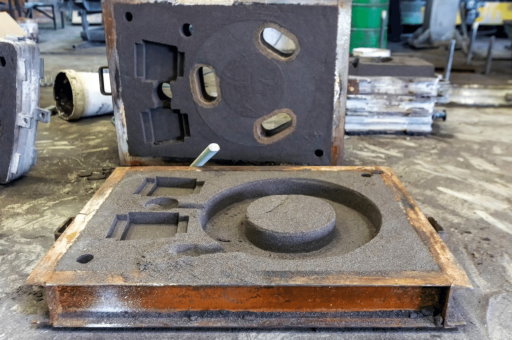
حفره قالب
«حفره» (Cavity)، فضای خالی درون قالب و مقصد نهایی مواد مذاب است. مواد مذاب با پر کردن حفره قالب، ساختار کلی قطعه مورد نظر را تشکیل میدهند.
سیستم راهگاهی قالب
«سیستم راهگاهی» (Gating system)، مجموعهای از مجراهای درون قالب است که امکان هدایت مواد مذاب از بیرون قالب به درون حفره را فراهم میکند. حوضچه، اسپرو، چشمه، راهبار، تغذیه، راهبار، راهباره و دریچه، از بخشهای اصلی سیستم راهگاهی به شمار میروند.
قطعه ریخته گری شده
قطعه ریخته گری شده، جسمی است که پس از فرآیند انجماد از درون حفره قالب خارج میشود. به قطعه ریخته گری شده، اصطلاحا «کستینگ» (Casting) میگویند.
ماسه ریخته گری
ریخته گری ماسه ای به عنوان متداولترین روش اجرای ریختهگری شناخته میشود. ماده اصلی در ساخت قالبهای این فرآیند، ماسه است. فراوانی و هزینه پایین ماسه سیلیسی، این ماده را به گزینه اول ساخت قالبهای ماسهای تبدیل میکند. البته انبساط حرارتی بالای ماسه سیلیسی، احتمال رخ دادن عیوب ریخته گری را افزایش میدهد. ماسه تر یا ماسه سبز، سیلیکات سدیم یا شیشه مایع و ماسه رزینی از رایجترین مواد مورد استفاده برای ساخت قالبهای ریختهگری هستند.
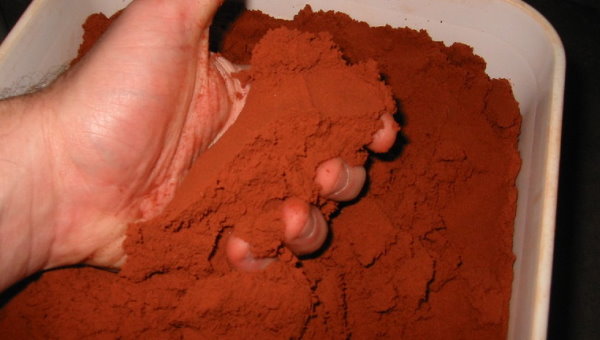
ماسه رزینی
ماسه رزینی، مادهای است که معمولا از ترکیب ماسه سیلیسی ریزدانه با رزین فنولی ترموست تشکیل میشود. مخلوط کردن این مواد با یکدیگر، امکان ساخت قالبهای سخت با استحکام بالا را فراهم میکند.
ماسه رویه
«ماسه رویه» (Facing Sand)، ماسهای است که برای ساخت بخشهای قالب در مجاورت مدل استفاده میشود. ماسه رویه در ارتباط مستقیم با مواد مذاب قرار میگیرد. از اینرو، این ماسه از مقاومت بسیار بالایی در برابر تنشهای حرارتی اعمال شده از طرف مواد مذاب بهره میبرد.
درجه یا فلاسک
دُرجه یا «فلاسک» (Flask)، ابزاری است که به منظور نگهداری قالب ریخته گری مورد استفاده قرار میگیرد. این وسیله، فقط دارای دیوارههای جانبی است و هیچ بخش بالایی یا پایینی ندارد. مقطع فلاسک، معمولا به شکل مقاطع سادهای نظیر مربع، مستطیل و دایره است.
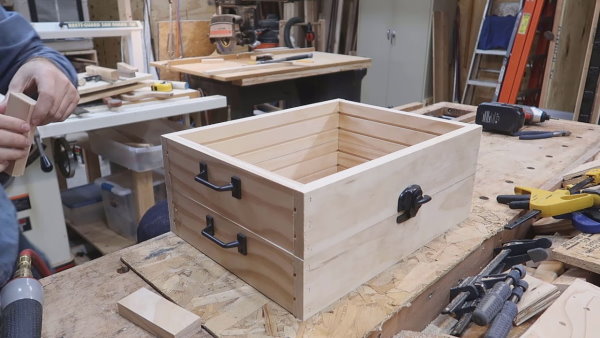
نیمه های فلاسک
اغلب روش های ریخته گری، از قالبهای دو تکه برای ساخت قطعات استفاده میکنند. از اینرو، فلاسک نیز به صورت دو تکه ساخته میشود. به بخش بالایی فلاسک، «کوپ» (Cope) و به بخش پایینی آن، «درگ» (Drag) میگویند.
چیک
در ریختهگریهای پیچیده، فلاسک، از چندین تکه (بیش از دو تکه) تشکیل میشود. به بخشهای میانی فلاسک در این حالت، «چیک» (Cheek) میگویند.
مدل یا الگو
مدل یا «الگو» (Pattern)، جسمی کاملا مشابه با قطعه نهایی ریخته گری است. این جسم به منظور ایجاد حفره قالب (فضای جریان یافتن مواد مذاب) مورد استفاده قرار میگیرد. از مواد قابل استفاده برای ساخت مدل ریخته گری میتوان به چوب، فلز و پلاستیک اشاره کرد.

مغزه یا ماهیچه
ماهیچه یا «مغزه» (Core)، قطعهای مجزا در قالب ریخته گری است که به منظور ایجاد بازکننده و فضاهای توخالی در قطعه مورد استفاده قرار میگیرد. در صورت پیچیدگی ساختار داخلی قطعه و عدم امکان دستیابی به شکل مورد نظر توسط مدل، از ماهیچه درون حفره قالب استفاده میشود. به این ترتیب، مواد مذاب، محل قرارگیری ماهیچهها را پر نمیکنند. ماهیچهها از ابزارهای پرکاربرد در فرآیندهای ریختهگری به شمار میروند.
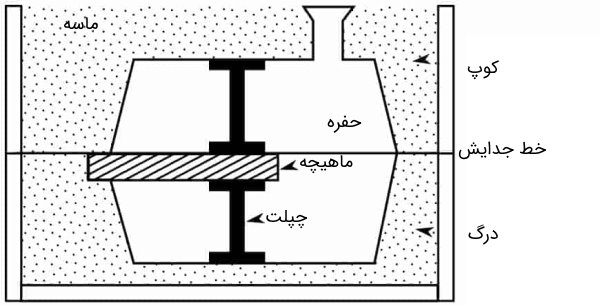
چپلت
«چپلت» (Chaplet)، قطعه کوچک فلزی است که به منظور نگهداری ماهیچه در حین فرآیند ریخته گری مورد استفاده قرار میگیرد. چپلتها، از جابجایی ماهیچه بر اثر نیروهای اعمال شده از طرف جریان مواد مذاب جلوگیری میکنند.
چیل
«چیل» (Chill)، قطعهای است که به منظور بهبود فرآیند انجماد (افزایش نرخ خنک شدن)، درون حفره قالب یا اطراف آن جانمایی میشود. در ریختهگریهای پیچیده، عدم تقارن شکل و ضخامت قطعات، از انجماد خطی و یکنواخت بخشهای مختلف جلوگیری میکند. چیلها، با تنظیم انتقال حرارتی در نقاط بحرانی، باعث تعدیل فرآیند انجماد میشوند. جنس این قطعات از مواد دارای هدایت الکتریکی بسیار بالا است.
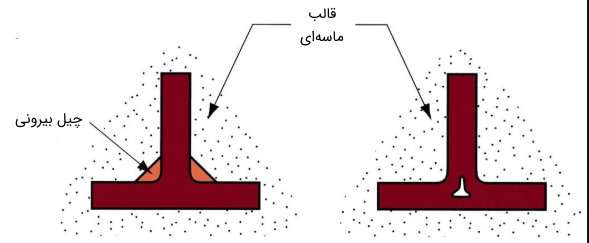
بوته
«بوته» (Crucible)، ظرفی است که به منظور نگهداری فلزات در حین فرآیند ذوب مورد استفاده قرار میگیرد. بوته ریخته گری معمولا از جنس مواد سرامیکی یا فلزی با نقطه ذوب بسیار بالا ساخته میشود. این وسیله درون کوره قرار میگیرد و حرارت کوره را به فلز درون خود انتقال میدهد. پس از ذوب شدن فلز، بوته برای شروع فرآیند ریختهگری به محل قرارگیری قالب انتقال داده میشود.
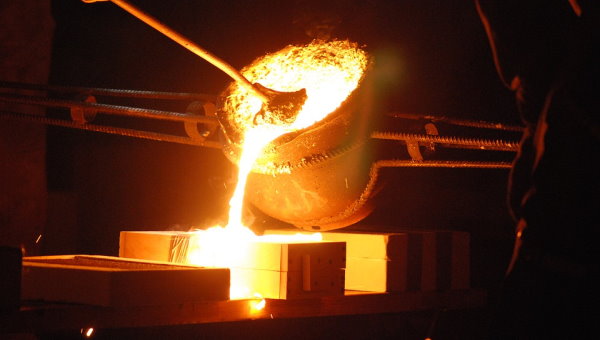
پاتیل
«پاتیل» (Ladle)، وسیلهای است که منظور انتقال و ریختن ماده مذاب در فرآیند ریخته گری مورد استفاده قرار میگیرد. پاتیلها اغلب در کارخانههای ذوب کاربرد دارند. این وسایل در ابعاد کوچک (با ظرفیت حدود 20 کیلوگرم) و بزرگ (با ظرفیت حدود 330 تن) ساخته میشوند. برخلاف بوته، پاتیلهای معمولی درون کوره قرار نمیگیرند. برخی از کورههای پایتلی، از قابلیت اعمال حرارت به فلز و ذوب آن بهره میبرند.
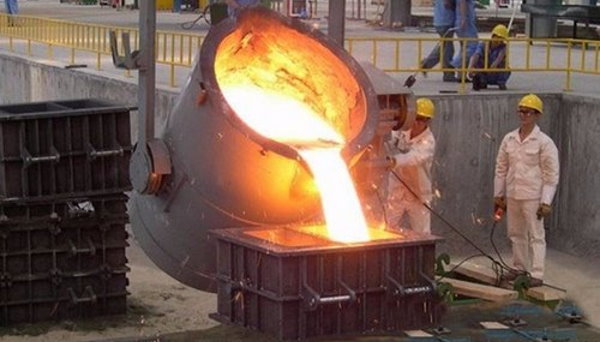
حوضچه بارریز
«حوضچه بارریز» (Pouring Basin)، یک حفره کوچک قیفی شکل در بخش بالایی قالب است که به منظور ریختن مواد مذاب به درون حفره داخلی استفاده میشود. حوضچه بارریز، نرخ جریان مواد مذاب را تنظیم میکند و اغتشاشات مواد در ورودی راهگاه را کاهش میدهد. تصویر زیر، بیانگر بخشهای مختلف قالب ریختهگری ماسهای و سیستم راهگاهی درون آن است. اصطلاحات مورد استفاده در اغلب روشهای ریختهگری، به یکدیگر شباهت دارند.
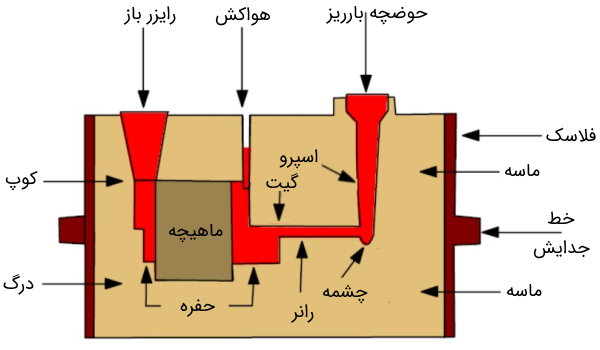
اسپرو یا راهگاه بارریز
راهگاه بارریز یا «اسپرو» (Sprue)، مجرای هدایت مواد مذاب از حوضچه بارریز به حفره قالب است. این مجرا، معمولا به شکل مخروطی طراحی و ساخته میشود. در بسیاری از موارد، کنترل جریان مواد مذاب توسط راهگاه بارریز انجام میگیرد.
چشمه راهگاه
در انتهای راهگاه بارریز و در محل اتصال آن با راهبار، فضایی وجود دارد که با تجمع مواد مذاب، از سقوط آزاد آنها جلوگیری میکند. به این فضا، چشمه راهگاه میگویند. چشمه راهگاه، اغتشاشات جریان و گیر کردن هوا درون مواد مذاب را کاهش میدهد. مقطع این چشمه معمولا به شکل دایره، قطر آن حدود دو برابر قطر انتهای راهگاه و عمق آن حدود دو برابر عمق راهبار است.
رانر یا راهبار
راهبار یا «رانر» (Runner)، مجرایی است که مواد مذاب را از راهگاه به دریچه یا تغذیه های اطراف حفره قالب هدایت میکند. رانرها با کاهش سرعت مواد مذاب، باعث جریان یکنواخت آنها به بخشهای مختلف حفره میشوند. این مجراها، معمولا در بخش پایینی قالب قرار دارند.
دریچه یا راهباره
راهباره یا دریچه «Gate یا Ingate»، مجرایی است که مواد مذاب را از راهبار به حفره اصلی قالب هدایت میکند. طراحی راهباره، باعث تغذیه یکنواخت حفره با نرخ ثابت و مطابق با نرخ انجماد میشود. در اغلب موارد، مقداری از مواد مذاب درون دریچه یا حتی دیگر مجراهای سیستم راهگاهی باقی میمانند. این مواد به همراه مواد درون حفره، طی فرآیند انجماد، سخت میشوند. از اینرو، پس از باز کردن قالب و خارج کردن قطعه، نیاز به عملیات ماشینکاری برای تهیه قطعه یا قطعات نهایی خواهد بود.
رایزر یا تغذیه
منبع تغذیه یا «رایزر» (Riser)، فضاهایی درون سیستم راهگاهی قالب هستند که در هنگام توقف ریختن مواد مذاب، به عنوان مخازن ذخیره و تامین مواد مورد استفاده قرار میگیرند. با توقف فرآیند ریختن، مواد مذاب درون حفرهها، بر اثر فرآیند انجماد، شروع به جمع شدن میکنند. کاهش حجم ناشی از جمعشدگی، باعث کاهش ابعاد و تغییر شکل قطعه ریختهگری شده نسبت به قطعه طراحی شده میشود. رایزرها، با تامین مواد مذاب اضافی، تاثیر جمعشدگی بر مشخصات ابعادی قطعه را کاهش میدهند. بر اساس دسترسی یا عدم دسترسی مجرا به بیرون قالب، رایزرها به انواع بالاسری (دسترسی از بالای قالب)، کناری (دسترسی از کنارههای قالب) و کور (بدون دسترسی) تقسیم میشوند.
غلاف رایزر
«غلاف رایزر» (Riser Sleeve)، قطعهای استوانهای شکل است که به منظور کاهش افت حرارتی رایزر توسط ایجاد عایق حرارتی و یا تولید حرارت برای جلوگیری از افت دما مورد استفاده قرار میگیرد. این قطعه، با کاهش میزان جمعشدگی، باعث پیوستگی فرآیند ریختهگری و افزایش کیفیت قطعه نهایی میشود.
هواکش
«هواکش» (Vent)، مجرای کوچکی است که امکان خروج هوا و گازهای ایجاد شده در قالب را فراهم میکند. طراحی مناسب هواکشها، از اهمیت بالایی برای جلوگیری از عیوب ریختهگری مرتبط با حضور گازها برخوردار است. هر چه سطح هواکشها از مقاومت کمتری در برابر جریان هوا برخوردار باشد، خروج گازها با سهولت بیشتری انجام میگیرد.
انواع روش های ریخته گری بر اساس مکانیزم اجرا چه هستند؟
ریخته گری ماسه ای، تحت فشار، ثقلی، دقیق و گریز از مرکز به عنوان متداولترین روشهای ریختهگری شناخته میشوند. در این بخش، به معرفی اصول اجرایی، کاربردها، تجهیزات، مزایا و معایب این روشها و دیگر روش های ریختهگری فلزات میپردازیم.
ریخته گری ماسه ای چیست ؟
«ریخته گری ماسه ای» (Sand Casting)، قدیمیترین و متداولترین روش ریختهگری است که در آن از قالب ماسهای یکبار مصرف برای ساخت قطعات فلزی استفاده میشود. ریخته گری با قالب ماسه ای در ساخت قطعات پیچیده کوچک تا بزرگ و سبک تا سنگین (چند گرم تا چند تن) کاربرد دارد. این روش به طور گسترده در کارخانههای ذوب مورد استفاده قرار میگیرد.
ریخته گری ماسه ای چگونه اجرا میشود؟
فرآیند ریختهگری ماسه ای طی شش مرحله کلی شامل قالب سازی، بستن قالب، ریختن مواد مذاب، خنک کاری، خارج کردن قطعه و برشکاری انجام میگیرد. طی این فرآیند، قالب ماسه ای به طور کامل از بین میرود و به منظور ساخت قطعه بعدی، یک قالب جدید ساخته میشود.
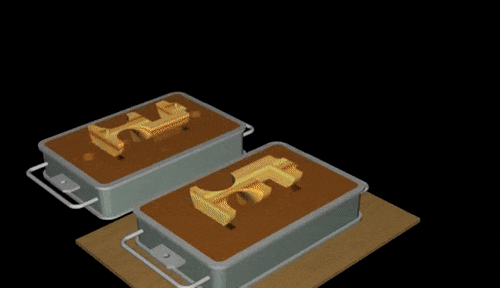
کاربرد ریخته گری ماسه ای چیست؟
ریختهگری ماسهای، متداولترین روش ساخت قطعات در کارخانههای ذوب است. این روش ساخت و تولید، در بسیاری از صنایع نظیر هوافضا، خودروسازی، ساخت ماشین آلات سنگین و غیره کاربرد دارد. به عنوان مثال، ساخت بلوک سیلندر، منیفلد، پایه ماشینآلات، دندهها و پولیها توسط ریختهگری ماسهای انجام میگیرد. انعطافپذیری بالا، باعث تنوع کاربری این روش شده است.
مواد قابل استفاده برای قطعات ریخته گری ماسه ای چه هستند؟
تقریبا تمام فلزات و آلیاژهای فلزی در ریختهگری ماسه ای قابل استفاده هستند. آلیاژهای فولادی، فولاد کربنی، چدن، برنج، فولاد ضد زنگ، آلومینیوم، مس، منیزیوم و نیکل از مواد اولیه رایج برای ساخت قطعات در قالب ماسه ای به شمار میروند. البته امکان ساخت قطعاتی از جنس سرب، قلع، تیتانیوم و روی نیز توسط این روش وجود دارد.
انواع ریخته گری ماسه ای کدام هستند؟
فرآیند ریختهگری ماسه ای، معمولا با توجه به الگوی قالب و نوع ماسه مورد استفاده برای قالب گیری تقسیمبندی میشوند. بر این اساس، از روشهای ساخت قطعات توسط قالبهای ماسهای میتوان به موارد زیر اشاره کرد:
- ریخته گری در ماسه تر
- ریخته گری در ماسه خشک
- ریخته گری گل و ماسه
- ریخته گری در قالب ماسه ای ماهیچه دار
تجهیزات مورد استفاده در ریخته گری ماسه ای چه هستند؟
قالب، ماهیچه، ماسه و ابزارهای تراکم ماسه از المانهای اصلی مورد نیاز برای ساخت قطعات فلزی به روش ریختهگری ماسهای هستند. ماهیچه، قطعهای به شکل قطعه نهایی است که به منظور ایجاد حفره درون قالب مورد استفاده قرار میگیرد. با ریختن خاک ریخته گری یا ماسه ریختهگری (معمولا ماسه سیلیسی) درون قالب، جانمایی ماهیچه درون ماسه و تراکم ماسه، حفرههای قالب و مجراهای ریختن مواد مذاب به درون آن تشکیل میشوند. فرآیند آمادهسازی تجهیزات این روش به دو صورت دستی و خودکار (توسط ماشینآلات مخصوص) قابل انجام هستند.
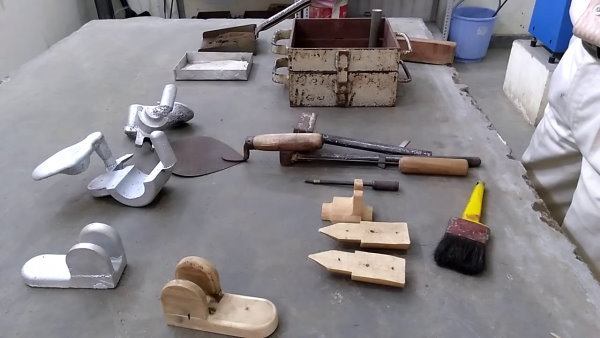
مزایا و معایب ریخته گری ماسه ای چیست؟
مزیتهای اصلی ساخت قطعات فلزی با قالبهای ماسهای عبارت هستند از:
- امکان تولید قطعات بسیار بزرگ
- امکان ساخت قطعات دارای ساختار پیچیده
- تنوع زیاد در مواد قابل استفاده
- هزینه پایین تجهیزات و ابزارهای برش
- کوتاه بودن فاصله زمانی بین دریافت سفارش تا تحویل کامل قطعات
از محدودیتهای ریختهگری ماسه ای میتوان به موارد زیر اشاره کرد:
- مقاومت نسبتا پایین قطعات
- احتمال بالای ایجاد تخلخل در قطعه
- کیفیت پایین پرداخت سطح و تلرانس آن
- نیاز به ماشینکاری ثانویه در اغلب موارد
- نرخ پایین تولید
- هزینه بالای نیروی کار
ریخته گری تحت فشار یا دایکاست چیست؟
ریخته گری تحت فشار یا دایکاست، یکی از متداولترین روشهای تولید انبوه قطعات فلزی غیر آهنی کوچک تا متوسط با استفاده قالبهای دائمی است. این روش، کاربرد بسیار گستردهای در ساخت قطعات مورد استفاده در صنعت اتومبیلسازی دارد. اغلب قطعات دایکاست از جنس آلومینیوم هستند. ریختهگری تحت فشار، امکان ساخت قطعات فلزی ساده تا پیچیده با ساختار یکپارچه را فراهم میکند.
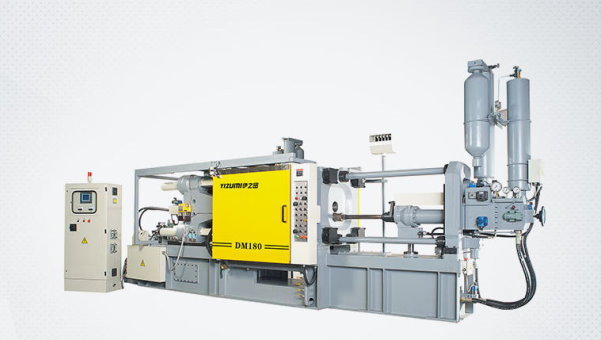
کاربرد دایکاست چیست؟
حدود 60 درصد از قطعات ساخته شده به روش ریختهگری تحت فشار در صنعت خودروسازی مورد استفاده قرار میگیرند. البته این روش ساخت و تولید در صنایع هوافضا، تجهیزات الکترونیکی، لوازم خانگی و جواهرسازی نیز به کار برده میشود.
دایکاست چگونه اجرا میشود؟
دایکاست طی پنج مرحله شامل آمادهسازی قالب، تزریق مواد مذاب، خنککاری، باز کردن قالب و برشکاری انجام میگیرد. فرآیند اجرای ریختهگری تحت فشار، شباهت بسیار زیادی به قالب گیری تزریقی (ساخت قطعات یکپارچه پلاستیکی) دارد.
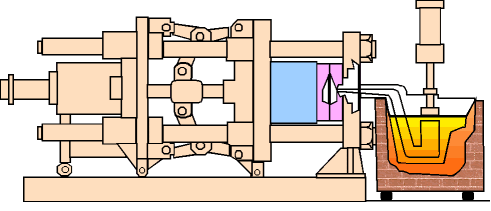
مواد قابل استفاده در دایکاست چه هستند؟
بیش از 80 درصد از قطعات دایکاست با استفاده از آلومینیوم و آلیاژهای مختلف آن نظیر زاماک ساخته میشوند. مس، منیزیوم، روی و قلع نیز کاربرد زیادی در فرآیند ریختهگری تحت فشار دارند.
انواع دایکاست کدام هستند؟
به طور کلی، ریختهگری تحت فشار بالا، به عنوان روش اصلی و استاندارد دایکاست شناخته میشود. با این وجود، محدودیت به کارگیری مواد در این روش، باعث توسعه فرآیندهای متنوعی از دایکاست شده است. هر یک از این فرآیندها، امکان ساخت قطعات با کیفیت، از جنس فلزات مختلف را فراهم میکنند. از انواع روشهای دایکاست بر اساس مکانیزم اجرا میتوان به موارد زیر اشاره کرد:
- ریخته گری تحت فشار بالا: ساخت قطعاتی از جنس آلومینیوم، برنج و منیزیوم (مواد دارای نقطه ذوب نسبتا بالا) توسط دستگاه دایکاست محفظه سرد
- ریخته گری تحت فشار پایین: ساخت قطعاتی از جنس روی، قلع و سرب (آلیاژهای دارای نقطه ذوب پایین) توسط دستگاه دایکاست محفظه گرم
- ریخته گری تحت فشار در خلا یا ریخته گری تحت خلا: ساخت قطعات نیازمند عملیات حرارتی
- ریخته گری تحت فشار کوبشی یا ریخته گری کوبشی: تقویت مواد الیافی و آلومینیوم مذاب
- ریخته گری تحت فشار نیمه جامد: ساخت قطعات منیزیمی و آلیاژهای آلومینیومی برای دستیابی به چگالی حداکثری و تخلخل حداقلی
تجهیزات مورد استفاده در دایکاست چه هستند؟
به طور کلی، دو نوع دستگاه شامل دستگاه دایکاست با سیستم تزریق محفظه گرم و دستگاه دایکاست با سیستم تزریق محفظه سرد در ریختهگری تحت فشار مورد استفاده قرار میگیرند.
دستگاههای محفظه گرم در ساخت قطعاتی از جنس روی، قلع و سرب (آلیاژهای دارای نقطه ذوب پایین) و دستگاههای محفظه سرد در ساخت قطعاتی از جنس آلومینیوم، برنج و منیزیوم (مواد دارای نقطه ذوب نسبتا بالا) کاربرد دارند. فشار عملیاتی دستگاههای محفظه گرم (69 تا 345 بار)، معمولا پایینتر از فشار عملیاتی دستگاههای محفظه سرد (138 تا 1380 بار) است.
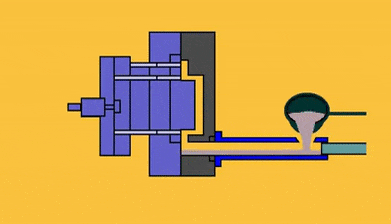
قالب دایکاست، از دیگر تجهیزات اصلی در اجرای ریختهگری تحت فشار است. این قالب، از اجزای متعددی تشکیل میشود که بر روی روند ساخت و کیفیت قطعه نهایی تاثیر میگذارند. طراحی قالب دایکاست، از مهمترین مراحل آمادهسازی در تولید قطعات دایکاست به شمار میرود.
مزایا و معایب دایکاست چیست؟
ریختهگری به روش دایکاست دارای مزایای متعددی است که مهمترین آنها عبارت هستند از:
- راندمان تولید بالا
- دقت ساخت خوب در ابعاد قطعات
- پرداخت خوب سطح و حجم پایین ماشینکاری مورد نیاز
- هزینه عملیاتی پایین در تولید انبوه
- هزینه پایین نیروی کار
- یکپارچگی بالای قطعه
- مقاومت بسیار مناسب در برابر خوردگی
از محدودیتهای اصلی دایکاست میتوان به موارد زیر اشاره کرد:
- مناسب نبودن برای فلزات و آلیاژهای دارای نقطه ذوب بالا مانند فولاد
- محدودیت ساخت قطعات بزرگ یا دارای طول بلند
- هزینه بالای سرمایهگذاری و تهیه قالب
- طولانی بودن فاصله زمانی بین دریافت سفارش تا تحویل کامل قطعات
- عدم صرفه اقتصادی برای تولید قطعات در تعداد کم
- امکان تشکیل حباب و تخلخل داخل قطعه
ریخته گری دقیق چیست ؟
«ریخته گری دقیق» (Investment Casting)، یکی از قدیمیترین روشهای ساخت و تولید قطعات فلزی پیچیده با دقت بالا است. در این روش، از قالبهای سرامیکی یکبار مصرف برای شکلدهی به مواد مذاب استفاده میشود.
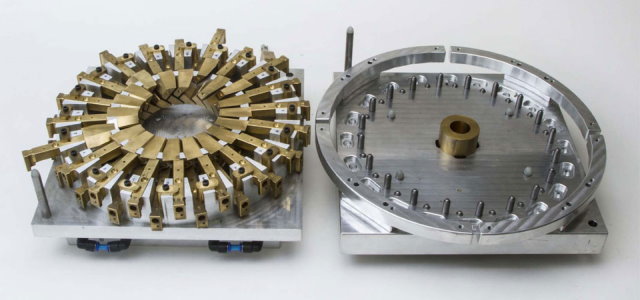
کاربرد ریخته گری دقیق چیست؟
ریختهگری دقیق در ساخت بسیاری از قطعات صنعتی و تجاری کاربرد دارد. به عنوان مثال، قطعات مهندسی نظیر رتور و پره توربین در موتور و ژنراتورها، اجزای مختلف ولوها، قطعات سلاحهای گرم و تجهیزات مورد استفاده در کارخانههای تولید مواد غذایی معمولا با استفاده از روش ریختهگری دقیق ساخته میشوند.
ریخته گری دقیق چگونه اجرا میشود؟
ریختهگری دقیق طی شش مرحله شامل مدلسازی، قالبسازی، ریختن مواد مذاب، خنککاری، خارج کردن قطعه از درون قالب و پرداخت سطح انجام میگیرد. الگوی قطعه (قطعهای از جنس موم)، درون دوغاب سرامیکی فرو برده شده و خارج میشود. پس از گیرش دوغاب، الگو به همراه سرامیک خشک شده داخل کوره قرار میگیرد. حرارت کوره، موم را آب میکند. به این ترتیب، قالب توخالی برای انجام مراحل بعدی آماده میشود.
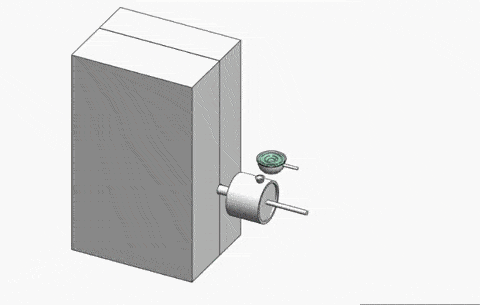
انواع روش های ریخته گری دقیق کدام هستند؟
از روشهای اجرای ریخته گری دقیق میتوان به «ریخته گری ضد جاذبه» (Counter Gravity Casting) و (ریخته گری لاست فوم) (Lost-Foam Casting) اشاره کرد.
مواد قابل استفاده برای قطعات ریخته گری دقیق چه هستند؟
از متداولترین مواد قابل استفاده در ریختهگری دقیق میتوان به فولاد، فولاد ابزاری فولاد کربنی، فولاد ضد زنگ، آلیاژهای آلومینیوم، آلیاژهای برنز، مس و نیکل اشاره کرد. علاوه بر این موارد، امکان ساخت قطعاتی از جنس چدن، سرب، منیزیوم، قلع، تیتانیوم و روی با استفاده از این روش وجود دارد. در صورت بالا بودن نقطه ذوب مواد و عدم امکان استفاده از قالبهای پلاستیکی یا فلزی، ریختهگری دقیق گزینه مناسبی خواهد بود.
تجهیزات مورد استفاده در ریخته گری دقیق چه هستند؟
موم، سرامیک و قالب فلزی مورد استفاده برای ساخت الگوی مومی، از المانهای مخصوص ریختهگری دقیق به شمار میروند. شکل حفره درون قالب سرامیکی (شکل قطعه مورد نظر)، با استفاده از یک الگوی مومی ایجاد میشود. این الگو درون دوغاب سرامیکی قرار میگیرد. پس از سخت شدن دوغاب، الگوی مومی از درون حفر خارج میشود. از اینرو، به روش ریختهگری دقیق، ریخته گری موم زائد یا اصطلاحا «ریخته گری لاست واکس» (Lost-Wax Casting) نیز میگویند.
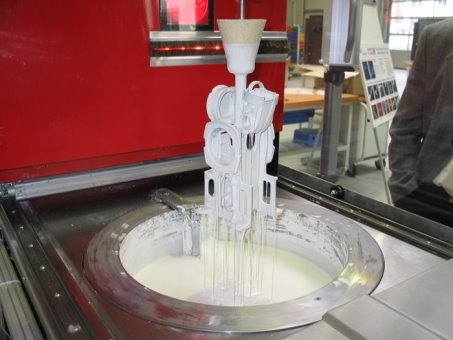
مزایا و معایب ریخته گری دقیق چیست؟
مهمترین مزیتهای ریختهگری دقیق عبارت هستند از:
- امکان ساخت قطعات ساده تا پیچیده با جزئیات دقیق
- تنوع مواد اولیه برای ساخت قطعات
- مقاومت بالای قطعات نهایی
- پرداخت بسیار خوب سطح با دقت بسیار بالا
- نیاز بسیار کم به ماشینکاری ثانویه
از محدودیتهای ریختهگری دقیق میتوان به موارد زیر اشاره کرد:
- زمانبر بودن روند اجرا
- هزینه بالای تهیه تجهیزات و نیروی کار
- طولانی بودن بازه دریافت تا تحویل سفارش
ریخته گری گریز از مرکز چیست ؟
«ریخته گری گریز از مرکز» (Centrifugal Casting) یا «ریخته گری دورانی» (Rotocasting)، یکی از انواع روش های ریختهگری است که به منظور ساخت قطعات استوانهای با دیوارههای نازک مورد استفاده قرار میگیرد.
روند اجرای این روش ساخت، باعث تراکم بیشتر ذرات در نزدیکی محیط خارجی قطعه و بهبود مشخصات مکانیکی آن نسبت به روشهای دیگر میشود.
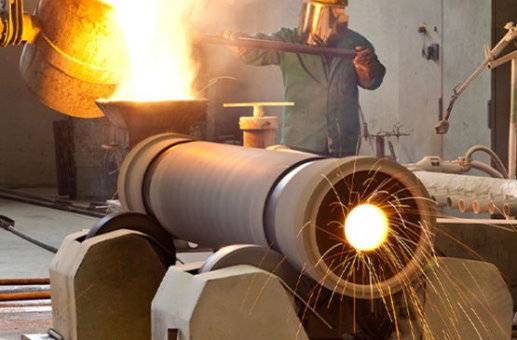
کاربرد ریخته گری گریز از مرکز چیست؟
کاربرد اصلی ریختهگری گریز از مرکز، ساخت قطعات استوانهای مورد استفاده در صنایع مختلف است. این فرآیند در تولید لوله، چرخ، فلنج، غلاف، شفت، رینگ پیستون، بوش، نازل پمپ، نازل ولو، فیتینگ، پوسته یاتاقان، مخزن فشار و بسیاری از دیگر قطعات استوانهای کاربرد دارد.
ریخته گری گریز از مرکز چگونه اجرا میشود؟
ریختهگری گریز از مرکز طی 5 مرحله اصلی شامل آمادهسازی قالب، ریختن مواد مذاب، خنککاری، خارج کردن قطعه از قالب و پرداخت سطح قطعه انجام میگیرد. روند اجرای این روش با اغلب روشهای ریختهگری تفاوت دارد. در ریخته گری دورانی، نیروی گریز از مرکز، باعث حرکت مواد مذاب به سمت دیوارههای قالب و تشکیل قطعه استوانهای میشود. محور دوران قالب، معمولا افقی است.
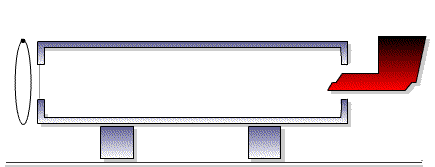
مواد قابل استفاده برای قطعات ریخته گری گریز از مرکز چه هستند؟
در ساخت قطعات به روش ریختهگری گریز از مرکز، از آلیاژهای آهنی نظیر فولاد کم آلیاژ، فولاد ضد زنگ، آهن و آلیاژهای غیر آهنی مانند آلومینیوم، برنز، مس، منیزیوم و نیکل استفاده میشود. البته این روش در تولید قطعات غیر فلزی نظیر شیشه و بتن نیز کاربرد دارد.
انواع ریخته گری گریز از مرکز کدام هستند؟
ریختهگری گریز از مرکز، با توجه به فرآیند اجرا، به سه نوع زیر تقسیم میشود:
- ریخته گری گریز از مرکز حقیقی یا کامل
- ریخته گری نیمه گریز از مرکز
- ریخته گری سانتریفیوژ
تجهیزات مورد استفاده در ریخته گری گریز از مرکز چه هستند؟
ریختهگری گریز از مرکز با استفاده از دستگاههای مخصوص انجام میگیرد. این دستگاهها از اجزایی نظیر غلتک، قالب استوانهای، ابزار انتقال مواد مذاب (قیف) و منبع تامین انرژی (موتور) تشکیل میشوند. پیکربندی دستگاه ریختهری گریز از مرکز میتواند به صورت افقی یا عمودی باشد.
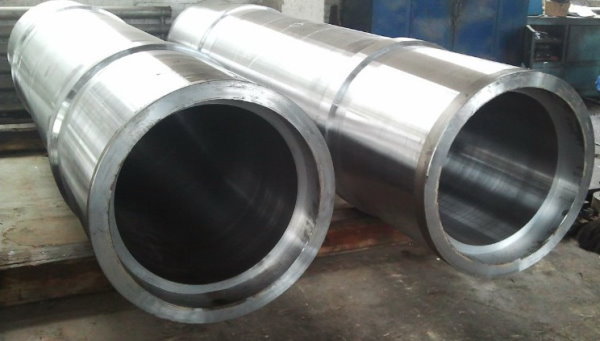
مزایا و معایب ریخته گری گریز از مرکز چیست؟
برخی از مهمترین مزیتهای ریختهگری گریز از مرکز عبارت هستند از:
- امکان ساخت قطعات بسیار بزرگ
- مشخصات مکانیکی خوب قطعات ساخته شده
- دقت بالای قطعات و پرداخت مناسب سطح خارجی
- هزینه پایین تجهیزات و نیروی کار مورد نیاز
- کم بودن میزان ضایعات تولید شده
از محدودیتهای ریختهگری دورانی میتوان به موارد زیر اشاره کرد:
- محدودیت شکل قطعات (استوانهای)
- نیاز به ماشینکاری ثانویه برای سطح داخلی در اغلب موارد
- زیاد بودن بازه تولید از دریافت تا تحویل سفارش
ریخته گری ثقلی چیست ؟
«ریخته گری ثقلی» (Gravity Casting) یا «ریخته گری در قالب دائمی» (Permanent Mold Casting)، از دیگر روشهای قدیمی ساخت قطعات فلزی با حجم متوسط تا بالا است. این روش شباهتهای زیادی به ریختهگری ماسهای و دایکاست دارد. البته برخلاف ریختهگری ماسهای و مشابه با دایکاست، قالب مورد استفاده در روش ثقلی از جنس فلز و از نوع دائمی (دارای قابلیت استفاده مجدد) است. این روش، اغلب به منظور تولید انبوه قطعات کوچک و ساده فلزی با ضخامت یکنواخت مورد استفاده قرار میگیرد.
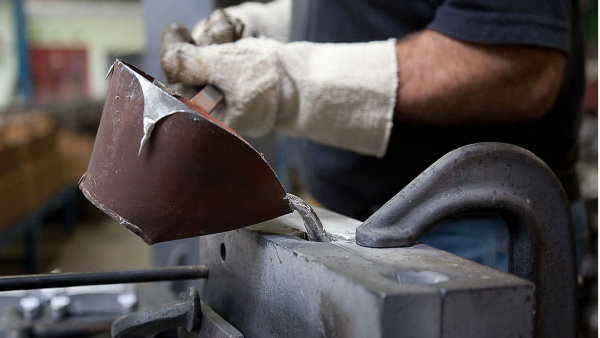
کاربرد ریخته گری ثقلی چیست؟
ریختهگری ثقلی، یکی از گزینههای بسیار مناسب برای ساخت قطعات پیچیده آلومینیومی در صنایع خودروسازی نظیر سر سیلندر، پیستون غیر فولادی، میل لنگ، دیسک ترمز و قطعات هیدرولیکی است. البته این روش ساخت در تولید قطعات تجهیزات روشنایی، آشپزخانه، نظامی/دفاعی، نیروگاهی و پزشکی نیز کاربرد دارد.
ریخته گری ثقلی چگونه اجرا میشود؟
ریختهگری ثقلی طی شش مرحله اصلی شامل آمادهسازی قالب (اعمال ماده جداکننده به سطح داخلی قالب)، سر هم کردن بخشهای مختلف قالب، ریختن فلز مذاب، خنککاری، باز کردن قالب و برشکاری بخشهای اضافی انجام میگیرد. ماده مذاب بر اثر نیروی جاذبه، وارد مجراهای قالب میشود و حفرههای درون آن را پر میکند.
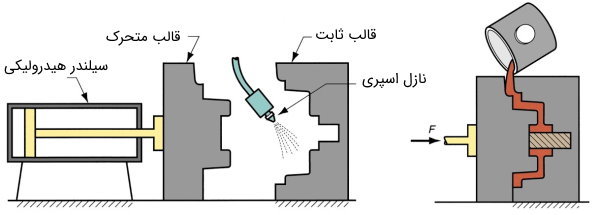
مواد قابل استفاده برای قطعات ریخته گری ثقلی چه هستند؟
قطعات در ریختهگری ثقلی معمولا از جنس آلیاژهای آلومینیومی و آلیاژهای غیر آهنی نظیر آلیاژهای مس، منیزیوم و روی هستند. البته در صورت استفاده از قالبهای گرافیتی، امکان تولید قطعات آهنی و فولادی نیز وجود خواهد داشت. از دیگر مواد قابل استفاده برای قطعات ریخته گری در قالب دائمی میتوان به فولاد کربنی، فولاد ضد زنگ، چدن، سرب، نیکل، قلع و تیتانیوم اشاره کرد.
انواع ریخته گری ثقلی کدام هستند؟
علاوه بر روند کلی اجرای ریختهگری ثقلی، فرآیندهای دیگری برای ساخت قطعات فلزی به این روش وجود دارند. از این متداولترین این فرآیندها میتوان به موارد زیر اشاره کرد:
- ریخته گری توخالی
- ریخته گری کم فشار در قالب دائمی
- ریخته گری تحت خلا در قالب دائمی
تجهیزات مورد استفاده در ریخته گری ثقلی چه هستند؟
ابزارها و تجهیزات اصلی مورد استفاده در ریختهگری ثقلی، مشابه با ابزارها و تجهیزات ریختهری ماسهای هستند. با این وجود، مکانیزم قالبگیری در این فرآیند، شباهت زیادی به دایکاست دارد. با این تفاوت که در ریختهگری ثقلی از دستگاههای قالب ریختهگری ثقلی، معمولا با عنوان قالب ریژه شناخته میشود.
این قالب مانند قالب دایکاست از دو بخش ثابت و متحرک تشکیل میشود. جابجایی قالب متحرک توسط یک سیلندر هیدرولیکی انجام میگیرد.
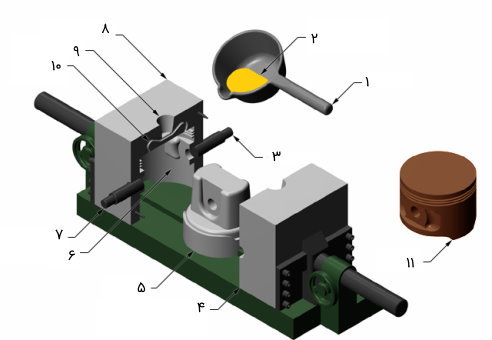
اجزای نمایش داده شده در تصویر بالا عبارت هستند از:
- پاتیل
- ماده مذاب
- پین یا چپلت ماهیچه
- نیمه ثابت قالب
- ماهیچه
- حفره
- پین یا چپلت ماهیچه
- نیمه متحرک قالب
- اسپرو
- رانر
- قطعه نهایی
مزایا و معایب ریخته گری ثقلی چیست؟
مزیتهای ریختهگری در قالب ریژه عبارت هستند از:
- دقت ابعادی بالا با تلرانس خوب
- تخلخل پایین
- هزینه پایین نیروی کار
- امکان بازیافت و استفاده مجدد از ضایعات
- پرداخت صافتر سطح قطعه نسبت به قالب ماسهای
- بهبود مشخصات مکانیکی قطعه نسبت به قالب ماسهای
- امکان ساخت قطعاتی با دیوارههای نازکتر نسبت به قالب ماسهای
- امکان ساخت قطعه با المانهای داخلی و پینهای فولادی
از محدودیتهای ریختهگری ثقلی میتوان به موارد زیر اشاره کرد:
- نرخ تولید پایین برای برخی از آلیاژها
- هزینه بالای طراحی و ساخت قالب نسبت به قالب ماسهای
- وجود محدودیت برای ساخت قطعات نازک (حداقل ضخامت 3 تا 5 میلیمتر)
- احتمال افزایش زمان بین دریافت تا تحویل سفارش
روشهای که تا به اینجا معرفی کردیم، بخش وسیعی از فرآیندهای مورد استفاده در صنعت ریختهگری را پوشش میدهند. بیش از 60 درصد از فرآیندهای ریختهگری با استفاده از قالبهای ماسه ای انجام میشوند. ساخت درصد بالایی از قطعات آلومینیومی، با استفاده از ریخته گری دایکاست انجام میگیرد. با وجود گسترش این روشها و سلطه آنها بر روی صنعت ریختهگری، روشهای دیگری نیز وجود دارند که هر یک از مزایای بیشتری در کاربریهای مختص به خود بهره میبرند. در ادامه به معرفی این روشها میپردازیم.
ریخته گری قالب پوسته ای چیست ؟
«ریخته گری قالب پوسته ای» (Shell Mold Casting)، یکی دیگر از روشهای ساخت قطعات فلزی پیچیده با ابعاد کوچک تا متوسط، توسط قالب یکبار مصرف نازک است. این روش، شباهت زیادی به ریختهگری ماسهای دارد. با این تفاوت که قالب مورد استفاده در این فرآیند، از ماسه رزینی با ضخامت کم ساخته میشود.
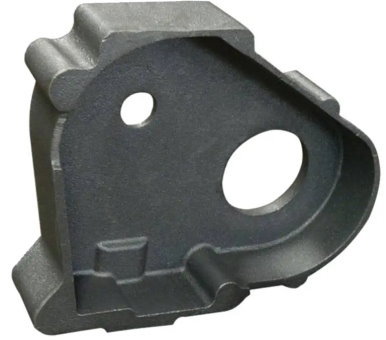
کاربرد ریخته گری قالب پوسته ای چیست؟
ریختهگری قالب پوسته ای در صنایعی به کار میرود که نیاز به ساخت قطعات کوچک تا متوسط با دقت بالا باشد. به عنوان مثال، این روش در تولید بدنه جعبه دنده، سر سیلندر، میلههای اتصال و اهرمهای اتومبیل کاربرد دارد.
ریخته گری قالب پوسته ای چگونه اجرا میشود؟
ریختهگری با قالب پوسته ای، طی شش مرحله اصلی شامل مدلسازی، ساخت قالب، سر هم کردن قالب، ریختن مواد مذاب به درون قالب، خنککاری و خارج کردن قطعه انجام میگیرد. تصویر متحرک زیر، نحوه ساخت قالب ماسه رزینی در این فرآیند را نمایش میدهد. به منظور خروج قطعه در انتهای ریختهگری پوستهای، قالب شکسته میشود. با وجود یکبار مصرف بودن قالب، مدل قطعه، برای ساخت قالب در چرخههای بعدی قابل استفاده است.
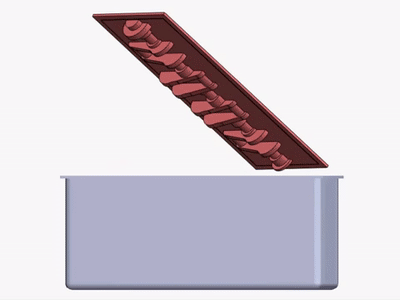
مواد قابل استفاده برای قطعات ریخته گری قالب پوسته ای چه هستند؟
از ریختهگری در قالب پوسته ای میتوان برای ساخت قطعاتی از جنس مواد آهنی و غیر آهنی استفاده کرد. چدن، فولاد کربنی، فولاد آلیاژی، فولاد ضد زنگ، آلیاژهای آلومینیوم، آلیاژهای مس و آلیاژهای نیکل از متداولترین مواد قابل استفاده در این فرآیند هستند.
تجهیزات مورد استفاده در ریخته گری قالب پوسته ای چه هستند؟
در فرآیند ریختهگری پوسته ای، از یک دستگاه مخصوص برای ساخت قالب استفاده میشود. از دیگر ابزارها و تجهیزات مورد استفاده در این فرآیند میتوان به مدلهای چدنی چندبار مصرف، ماسه رزینی و آون اشاره کرد.
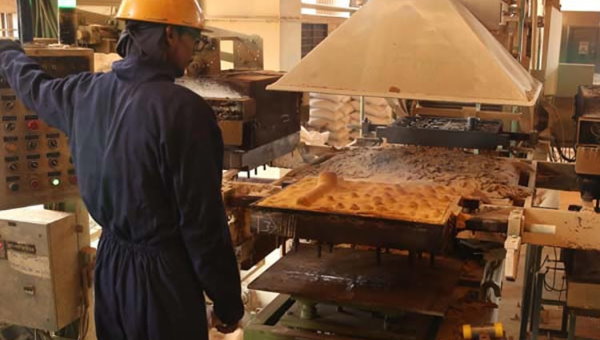
مزایا و معایب ریخته گری قالب پوسته ای چیست؟
برخی از مهمترین مزیتهای ریختهگری قالب پوسته ای عبارت هستند از:
- امکان ساخت قطعات پیچیده با جزئیات ریز و دیوارهای نازک به دلیل استفاده از قالبهای یکبار مصرف
- نرخ تولید بالا به دلیل استفاده از مدلهای چندبار مصرف
- پرداخت بسیار خوب سطح
- هزینه پایین نیروی کار به دلیل عدم نیاز به نیروی کار ماهر
- هزینه پایین ساخت قالب
- ضایعات کم
از محدودیتهای ریختهگری با قالب پوسته ای میتوان به موارد زیر اشاره کرد:
- هزینه بالای تجهیزات و تولید (صرفه اقتصادی در تولید انبوه)
- هزینه بالای الگوها
- محدودیت در ابعاد و وزن قطعات قابل ساخت
ریخته گری پیوسته چیست ؟
ریخته گری مداوم یا «ریخته گری پیوسته» (Continuous Casting)، یکی از روشهای سریع ریختهگری است که به منظور تولید قطعات ساده فولادی نظیر میلگرد و قطعات نیمه ساخته مورد استفاده قرار میگیرد. ریختهگری مداوم به عنوان یکی از روشهای متفرقه ریختهگری به شمار میرود؛ چراکه علاوه بر فرآیند اجرایی متفاوت، از هیچ قالب مرسومی در آن استفاده نمیشود.
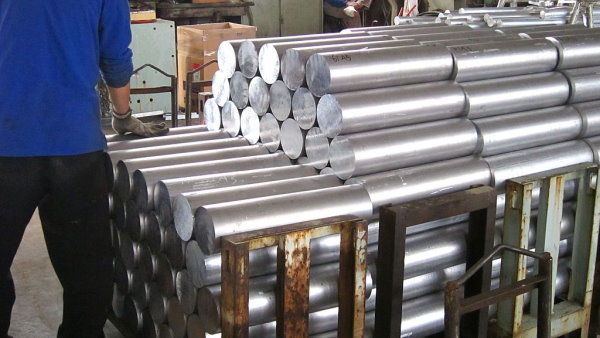
کاربرد ریخته گری پیوسته چیست؟
ریخته گری مداوم، از روشهای پرکاربرد و در حال توسعه در صنعت فولاد، مخصوصا کارخانه های تولید میلگرد به شمار میرود. در سال 2003 میلادی (1382 شمسی)، حدود 21 درصد از میلگردهای دنیا با استفاده از این روش ساخته شدند. به طور کلی، ریختهگری پیوسته در ساخت محصولات نیمه ساخته نظیر شمش، شمشال، شمشه و تختال کاربرد دارد. این محصولات، طی فرآیندهای ثانویه به محصولات قابل استفاده در صنایع دیگر تبدیل میشوند.
ریخته گری پیوسته چگونه اجرا میشود؟
ریخته گری پیوسته طی چهار مرحله اصلی شامل ریختن ماده مذاب به درون پاتیل، انتقال ماده مذاب به پاتیل میانی، عبور ماده مذاب از قالب بسیار خنک و برش قطعات انجام میگیرد. تصویر زیر، ترتیب اجرای این چهار مرحله را به خوبی نمایش میدهد. در هنگام عبور ماده مذاب از درون قالب خنک کننده، یک پوسته سخت در اطراف مواد به وجود میآید. این مسئله باعث حفظ دمای بالا در مرکز رشته به وجود آمده میشود.
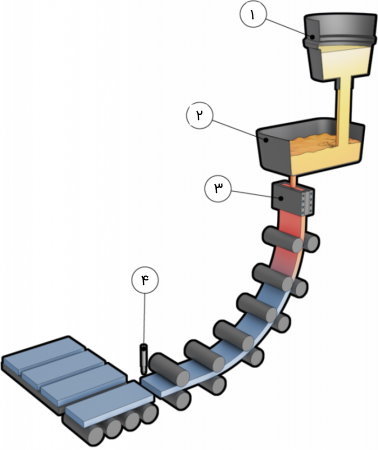
تجهیزات مورد استفاده در ریخته گری پیوسته کدام هستند؟
ریخته گری پیوسته با استفاده از تجهیزات مخصوص و بزرگ اجرا میشود. پاتیل میانی، قالب خنککننده و ابزار برش از المانهای شاخص در این فرآیند هستند. پاتیل میانی یا اصطلاحا «تاندیش» (Tandish)، به منظور اطمینان از کافی بودن فلز مذاب برای اجرای فرآیند ریختهگری مورد استفاده قرار میگیرد. قالب خنک کننده نیز وظیفه اعمال مایع جداکننده و کاهش دمای مواد مذاب را بر عهده دارد. اطراف این قالب، کاملا بسته است. در انتهای فرآیند، دستگاه برشکاری اکسیژنی، رشتههای فولاد را به قطعات کوچکتر برش میدهند.
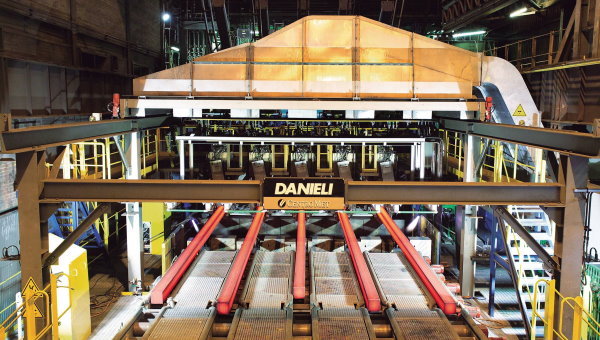
مواد قابل استفاده برای قطعات ریخته گری پیوسته چه هستند؟
ریخته گری پیوسته، فرآیندی است که به طور گسترده در ساخت قطعات فولادی مورد استفاده قرار میگیرد. با این وجود، امکان استفاده از این روش برای تولید قطعات آلومینیومی و مسی نیز وجود دارد.
مزایا و معایب ریخته گری پیوسته چیست؟
اصلیترین مزیتهای ریختهگری مداوم عبارت هستند از:
- تولید انبوه دالها و میلگردهای فولادی در مدت زمان کوتاه
- عدم استفاده از اسپرو، رانر، رایزر و استفاده 100 درصدی از مواد مذاب (بدون ضایعات و هدررفت)
- بالا بودن مشخصات مکانیکی قطعات
- پرداخت عالی سطح
- کاهش قابل توجه تخلخل داخلی و جمع شدگی مرکز قطعه
از محدودیتهای ریختهگری پیوسته میتوان به موارد زیر اشاره کرد:
- نیاز به تجهیزات مخصوص برای قالبگیری و خنککاری مداوم به منظور جلوگیری از جمع شدگی
- امکان تولید قطعات با شکل ساده و مقطع یکنواخت
- هزینه سرمایهگذاری بالا برای راهاندازی خط تولید و اقتصادی نبودن برای حجم تولید کم
- نیاز به فضای زیاد برای اجرای عملیات
ریخته گری با مدل تبخیری چیست ؟
«ریخته گری با مدل تبخیری» (Evaporative-Pattern Casting)، یکی از روشهای ریختهگری ماسهای است که در آن، از مدلهای قابل تبخیر برای ساخت حفره قالب استفاده میشود. مدلهای مورد استفاده در این فرآیند، معمولا از جنس فومهای پلی استایرن هستند. با ریختن ماده مذاب به درون قالب، مدل تبخیر میشود و ماده مذاب فضای خالی را پر میکند.
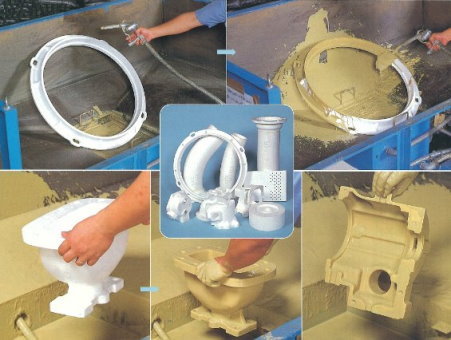
کابرد ریختهگری با مدل تبخیری چیست؟
ریختهگری با مدل تبخیری معمولا به منظور ساخت قطعات آلومینیومی مورد استفاده قرار میگیرد. البته این فرآیند در تولید قطعات فولادی و آهنی نظیر لولههای آب و قطعات پمپ نیز کاربرد دارد.
انواع ریختهگری با مدل تبخیری کدام هستند؟
ریختهگری با مدل تبخیری، به دو روش «ریخته گری لاست فوم» (Lost-Foam Casting) و «ریخته گری کامل قالب» (Full-Mold Casting) اجرا میشود:
- ریختهگری به روش لاست فوم: روشی مشابه با ریختهگری دقیق که به جای موم از فوم پلی استایرن استفاده میکند.
- ریختهگری کامل قالب: روشی مشابه ریختهگری ماسهای و لاست فوم که به جای مدل دائمی (چندبار مصرف) از مدل فوم تبخیری استفاده میکند.
مزایا و معایب ریختهگری با مدل تبخیری چه هستند؟
مزیتهای ریختهگری با مدل تبخیری عبارت هستند از:
- قابلیت ساخت قطعات سبک
- اجرای آسان نسبت به دیگر روشهای ریختهگری
- دقت ابعادی بالا
- امکان ساخت قطعات پیچیده بدون نیاز به ماهیچه
- پرداخت با کیفیت و صاف قطعه
- هزینه پایین نسبت به ریختهگری دقیق به دلیل استفاده از فوم به جای موم
- عدم نیاز به طراحی رایزر به دلیل خنککاری سریع مواد مذاب (تبخیر فوم)
از محدودیتهای ریختهگری با مدل تبخیری میتوان به موارد زیر اشاره کرد:
- نیاز به دمای بالا برای تبخیر مدل
- محدودیت در ساخت قطعات دارای ضخامتهای پایین
- آسیبپذیری بالای مدلها
- زمانبر بودن فرآیند اجرا به دلیل مراحل نسبتا زیاد
- اقتصادی نبودن برای حجم تولید پایین
- هزینه اولیه بالا در صورت استفاده از قالبهای مخصوص مدلسازی
دیگر انواع روش های ریخته گری
در بخشهای قبلی، به معرفی برخی از مهمترین و پرکاربردترین روشهای ریختهگری پرداختیم. ریختهگری، از تنوع بسیار زیادی در فرآیند اجرا و تجهیزات مورد استفاده بهره میبرند. برخی دیگر از روشهای شناختهشده برای اجرای این فرآیند عبارت هستند از:
- «ریخته گری دیزاماتیک» (DISAMATIC Casting): روشی با خط تولید اتوماتیک برای ساخت قالب ماسهای و تولید انبوه قطعات مورد استفاده در صنایع خودروسازی و ماشینسازی
- «ریخته گری در قالب گچی» (Plaster Mold Casting): روشی مشابه ریختهگری ماسهای اما با قالبهای یکبار مصرف گچی
- «ریخته گری سریع» (Rapid Casting): ادغام روشهای مرسوم ریختهگری با روشهای نمونهسازی سریع نظیر
پرینت سهبعدی - «ریخته گری فرسابی» (Ablation Casting): روشی مشابه ریختهگری ماسهای اما با قالب قابل حل
- «ریخته گری سرمایش مستقیم» (Direct Chill Casting): روشی مشابه ریختهگری پیوسته با قالب باز و کوتاه
- «ریخته گری انجمادی» (Freeze-Casting): روشی برای ساخت قطعات متخلخل در دماهای پایین
- «ریخته گری ژلی» (Gelcasting): روشی برای ساخت داربست سرامیکی و پلیمری
- «ریخته گری شیشه» (Gelcasting): روشی برای ساخت قطعات شیشهای بر مبنای اصول ریختهگری
- «ریخته گری چرخشی» (Spin Casting): روشی مشابه ریختهگری گریز از مرکز برای ساخت قطعات لاستیکی
- «ریخته گری نواری» (Tape Casting): فرآیند ساخت نوارها و ورقههای سرامیکی
انواع روش های ریخته گری بر اساس ماده مورد استفاده و کاربرد آنها
همان طور که در بخشهای قبلی اشاره کردیم، فلزاتی نظیر چدن خاکستری، چدن نشکن، آلومینیوم، فولاد، مس و روی از متداولترین مواد مورد استفاده در ریختهگری به شمار میروند. خواص مکانیکی این مواد، هر یک از آنها را به گزینهای مناسب برای ساخت قطعات مورد نیاز در صنایع مختلف تبدیل میکند.
به علاوه، سازگاری برخی از مواد فلزی با برخی از روشهای ریختهگری بیشتر است. از اینرو، در صنایع مختلف، فرآیندهای ریختهگری معمولا با عنوان ماده مورد استفاده مشخص میشوند. در ادامه، به ویژگیهای هر یک از این فرآیندها میپردازیم.
ریخته گری چدن خاکستری
«چدن» (Cast Iron)، پرکاربردترین فلز مورد استفاده در حوزه ساخت و تولید است. این ماده از استحکام بالایی بهره میبرد. پرداخت آسان سطح قطعه بدون نیاز به روشهای مخرب، امکان ساخت قطعاتی با مشخصات سفارشی و هزینه پایین در تولید انبوه در ویژگیهای ریخته گری چدن خاکستری است.
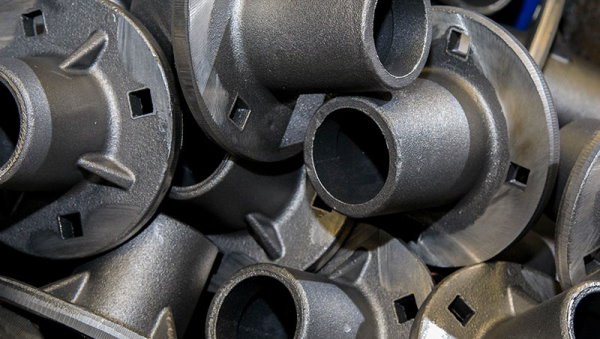
به طور کلی، این فرآیند در بسیاری از صنایع برای ساخت قطعاتی با مشخصات زیر به کار میرود:
- مقاوم در برابر لرزش
- نسبت مقاومت به وزن بالا
- ابعاد پایدار
ریخته گری چدن نشکن
چدن چکش خوار، چدن نشکن یا «چدن مالیبل» (Malleable Cast Iron)، مادهای با خصوصیات مشابه با چدن خاکستری است که امکان دستیابی به خواص مکانیکی بهتر را فراهم میکند.ریختهگری چدن نشکن برای ساخت قطعاتی با ویژگیهای زیر مورد استفاده قرار میگیرد:
- استحکام زیاد
- مقاومت در برابر خوردگی
- چقرمگی بالا
- شکلپذیری بالا
- وزن کمتر
- جمعشدگی کمتر
- هزینه پایینتر
ریخته گری آلومینیوم
آلومینیوم، از معدود مواد قابل استفاده در اغلب روش های ریختهگری است. این فلز از مقاومت عالی در برابر خوردگی، هدایت الکتریکی/حرارتی بالا، خواص مکانیکی خوب و استحکام مناسب در دماهای بالا بهره میبرد. تمام این ویژگیها، ریخته گری آلومینیوم را به یکی از فرآیندهای پرکاربرد در اکثر صنایع تبدیل میکنند.
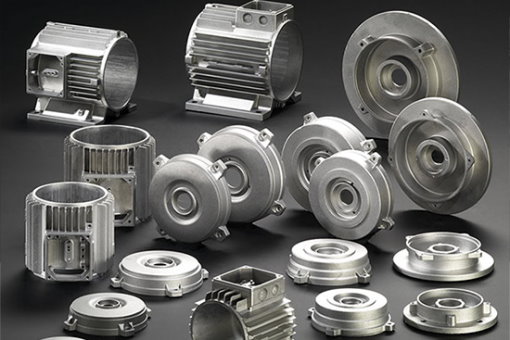
از متداولترین روش های ریختهگری آلومینیوم میتوان به موارد زیر اشاره کرد:
- دایکاست
- ریختهگری در قالب دائمی یا ریخته گری ثقلی
- ریختهگری دقیق
- ریختهگری ماسه ای
- ریختهگری لاست فوم
- ریختهگری کوبشی
ریخته گری فولاد
فولاد، به خصوص فولاد ضد زنگ، از مواد بسیار سختی است که برای ساخت قطعات تحت بارهای سنگین، لرزش زیاد و فرسودگی قابل توجه مورد استفاده قرار میگیرد. این ماده از عملکرد بسیار خوبی در محیطهای مرطوب و دماهای بالا بهره میبرد. ترکیب فولاد با کروم، آهن و نیکل، مقاومت آن در برابر خوردگی را بهبود میبخشد. از اینرو، ریخته گری فولاد در صنایع نیازمند این ویژگیها کاربرد دارد.
ریخته گری مس
مس، به عنوان یک مادهای با قابلیت هدایت الکتریکی عالی شناخته میشود. به همین دلیل، قطعات الکتریکی ساخته شده توسط ریخته گری مس، کاربرد گستردهای در صنعت ساختمانسازی دارند. برخی دیگر از مزایای قطعات مسی عبارت هستند از:
- چکشخواری خوب
- شکلپذیری عالی
- انتقال حرارتی مناسب
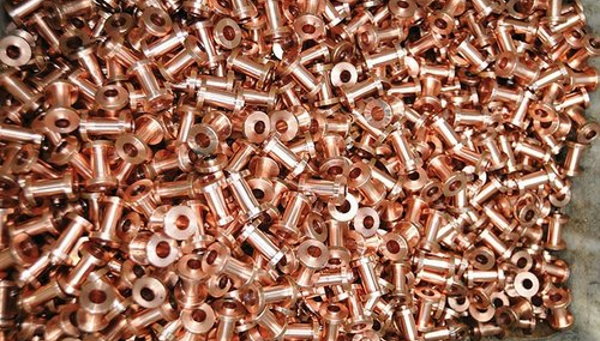
با وجود مزیتهای مس، ریختهگری این فلز میتواند باعث ایجاد ترک، تخلخل و حفرههای داخلی در قطعه شود. از اینرو، برای رفع این مشکلات، ریختهگری مس با ترکیب مواد دیگری نظیر سیلیکون، نیکل، روی، کروم، قلع و نقره انجام میگیرد.
ریخته گری روی
روی، فلزی با دمای ذوب پایین (425 درجه سانتیگراد) است. دمای ذوب پایین، روی را به یکی از مواد مناسب برای ریختهگری تبدیل میکند. ریخته گری روی با سرعت بالا (پر شدن راحت حفرهها و خنککاری سریع) انجام میشود. از نظر اقتصادی، ریختهگری روی برای تولید انبوه قطعات کوچک مناسب است.
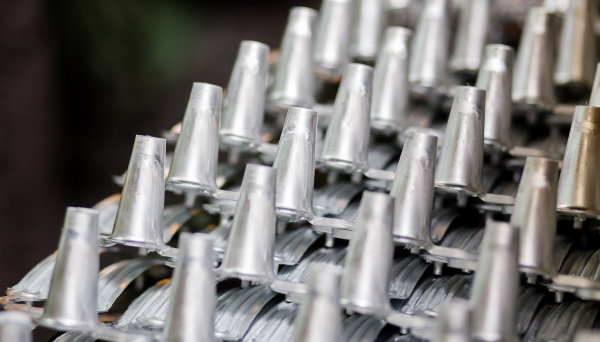
مقایسه مواد قابل استفاده در ریخته گری
ریخته گری روی، به عنوان روشی کارآمد برای اجرای دایکاست شناخته میشود. البته دوام پایین و مقاومت کم روی در برابر فرسودگی، کاربرد آن در محیطهای مستعد خوردگی یا کرنش زیاد را محدود میکند. برای دایکاست قطعاتی با عملکرد خوب و انعطافپذیری بالا، آلومینیوم گزینه مناسبی خواهد بود. برای ریختهگری قطعات مورد استفاده برای کاربریهای سازهای (نیاز به دوام و مقاومت بالا)، چدن خاکستری یا چدن نشکن در اولویت قرار میگیرد. کارایی چدن خاکستری در پروژههای نیازمند قطعاتی با شکل پیچیده و بدون جمعشدگی (مانند بلوک سیلندر) بیشتر است. چدن نشکن، عملکرد بهتری در ریختهگری قطعات نیازمند استحکام تنشی و چقرمگی بالا (نظیر اجزای حساس موتور) دارد.
عوامل موثر بر کیفیت ریخته گری چه هستند؟
هدف اصلی از اجرای فرآیند ریخته گری، تولید قطعات با کیفیت و بهرهمندی از مزایای این روش نسبت به دیگر روشهای ساخت است. عوامل متعددی بر کیفیت قطعه ریختهگری شده تاثیر میگذارند که از مهمترین آنها میتوان به موارد زیر اشاره کرد:
- طراحی قطعه و قالب
- روش اجرا
- کیفیت مواد اولیه
- تجهیزات
طراحی بخشهای مختلف قطعه و قالب
طی طراحی قالب های صنعتی، علاوه بر تعیین شکل و ابعاد بخشهای مختلف قالب بر اساس شرایط عملیاتی، منطقی بودن طراحیهای صورت گرفته بر اساس خواص مقاومتی نیز باید مورد بررسی قرار گیرد. به عنوان مثال، طراحی یکپارچه بخشهای مختلف قالب، استحکام را بهبود میبخشد. در طرف مقابل، یکپارچگی قالب در ریختهگریهای قطعات پیچیده، دقت اجرای فرآیند و سهولت خروج قطعه را با مشکل مواجه میکند. از اینرو، دستیابی به خروجی با کیفیت، نیازمند طراحی بهینه با قابلیت ساخت بالا خواهد بود.
انتخاب روش اجرای منطقی و مناسب
روش ریخته گری، باید مطابق با ساختار، وزن و ابعاد قطعه، مشخصات فلز یا آلیاژ مصرفی و شرایط عملیاتی انتخاب شود. سیستم راهگاهی، هواکش و دیگر اجزای قالب، تاثیر قابلتوجهی بر روی کیفیت قطعه نهایی دارند.
استفاده از مواد اولیه با کیفیت
هرچه کیفیت مواد اولیه و سازگاری آنها با روش انتخابی بیشتر باشد، کیفیت قطعه نهایی، مطابقت بیشتری با مشخصات طراحی خواهد داشت. در صورت استفاده از مواد بی کیفیت، احتمال رخ دادن عیب و نقصهای متعدد افزایش مییابد. این مسئله بر روی ساختار سطحی و داخلی قطعه تاثیر میگذارد. به علاوه، استفاده از مواد بی کیفیت، میزان ضایعات فرآیند را افزایش میدهد.
تجهیزات مورد استفاده
از دیگر عوامل موثر بر کیفیت ریختهگری میتوان به تجهیزات مورد استفاده در این فرآیند اشاره کرد. هر چه سطح تکنولوژی تجهیزات بالاتر باشد، توان فنی کارکنان و امکان اجرای صحیح فرآیندها افزایش مییابد.
سلام،بسیار ممنون از مطالب ارائه شده.
اگر ممکن هست مشخصا طرز ریخته گری پره های تک بلور( single crystal ) در توربین های گازی راکه درمعرض دمای حدود 1000 درجه سانتیگراد محصولات احتراق قرار دارند راتوضیح فرمائید.
ممنون عالی
بسیار عالی و کامل . ممنون
درود، خواهشاً هر بخش رو با تصویر نشون بدید تا درک موضوع برای ما راحت تر باشه،ممنون
بسیار مفید بود ممنون از شما
خیلی ممنون از اینکه انقدر کامل بود