طراحی قالب های صنعتی – راهنمای رایگان مبانی طراحی انواع قالب صنعتی
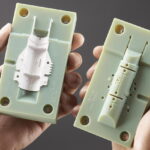
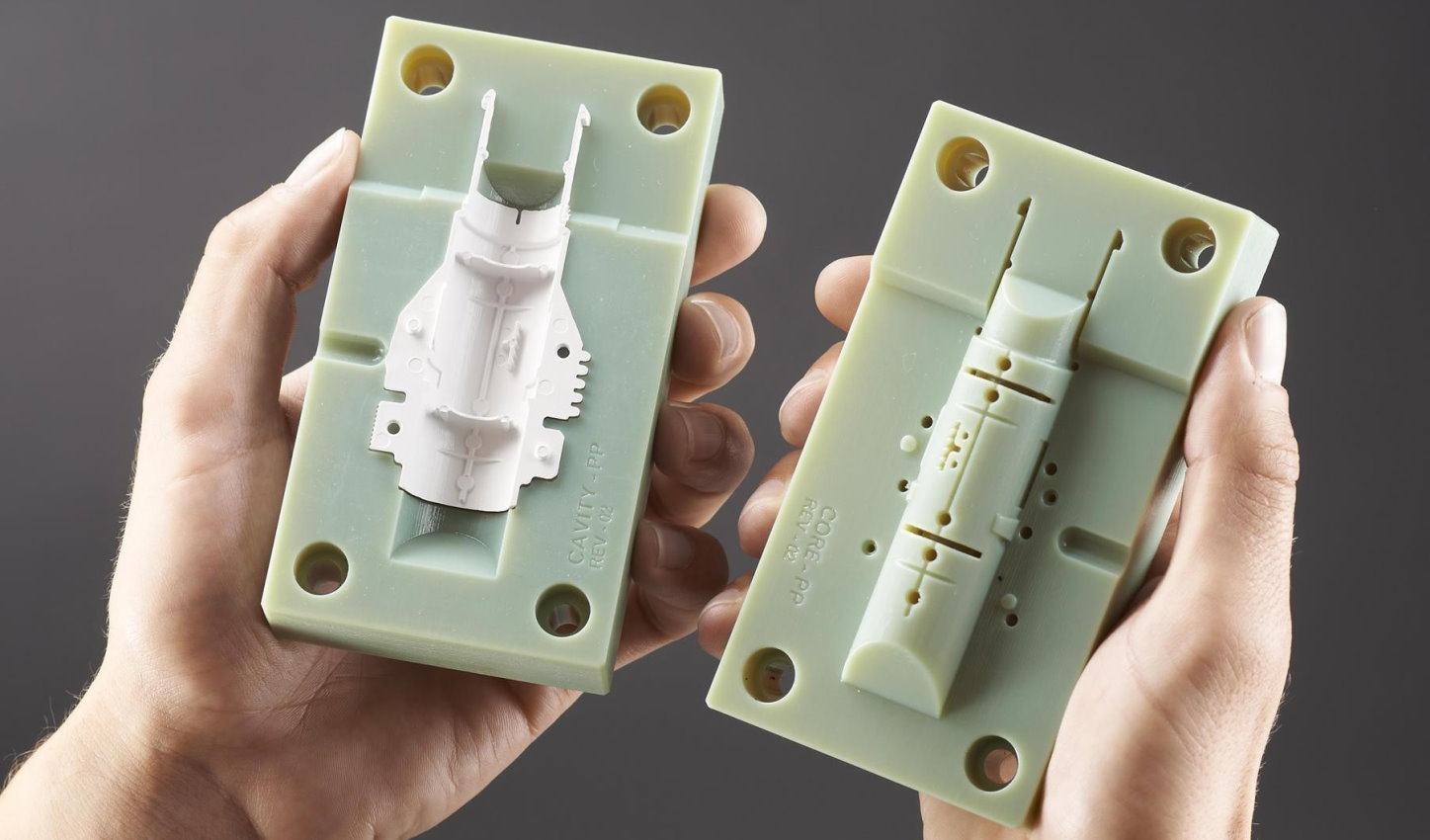
اگر به وسایل محیط اطراف خود دقت کنید، متوجه خواهید شد که بسیاری از آنها از اتصال چند قطعه به یکدیگر تشکیل شدهاند. اغلب این قطعات دارای جزئیاتی هستند که باعث کنجکاوی افراد در مورد نحوه ساخت آنها میشوند. استفاده از قالب های صنعتی برای قالبگیری یا ریختهگری، از رایجترین روشهای ساخت و تولید انبوه قطعات است. آشنایی با این قالبها و نحوه به کارگیری آنها، ابهام بسیاری از افراد در مورد نحوه ساخت قطعات مختلف را برطرف میکند. با این وجود، سوال تخصصیتری که پیش میآید این است که قالب های صنعتی چگونه ساخته میشوند. قالبهای صنعتی انواع متعددی دارند که هر یک از آنها با توجه به مکانیزم مختص به خود، به منظور ساخت قطعات متفاوت مورد استفاده قرار میگیرند. این قالبها طی چندین مرحله و با بررسی دقیق تمام جوانب مربوط به مکانیزم قالبگیری ساخته میشوند. از مهمترین مراحل ساخت قالب های صنعتی، طراحی آنها است. در این مقاله، به معرفی اصول طراحی قالب های صنعتی و بهترین منابع موجود برای یادگیری این مهارت میپردازیم. به این منظور، انواع قالبها، اجزا و مکانیزم اجرایی آنها مورد بررسی قرار میدهیم. البته شما میتوانید با مشاهده فیلمهای مجموعه آموزش طراحی قالب – مقدماتی تا پیشرفته در فرادرس، خیلی سریع و راحت، نحوه طراحی انواع قالبهای صنعتی را یاد بگیرید.
روش های ساخت و تولید قطعات کدام هستند؟
روشهای متنوعی برای ساخت و تولید قطعات در مقیاس صنعتی وجود دارند. از متداولترین روشهای تولید انبوه قطعات میتوان به ریخته گری، قالب گیری، پوشش دهی، حکاکی و چاپ، شکل دهی یا فلزکاری، ماشین کاری و اتصال (جوشکاری، پیچکاری و غیره) اشاره کرد.
ریخته گری و قالب گیری از روشهای ساخت و تولید به وسیله قالب های صنعتی هستند.

قالب چیست ؟
«قالب» (Mold یا Mould)، یک قطعه صلب یا بلوک توخالی است که توسط مایعات یا مواد انعطافپذیری مانند پلاستیک، لاستیک، فلز، شیشه یا سرامیک (در حالت مذاب) پر میشود. مواد پرکننده طی فرآیند گیرش از حالت مایع به حالت جامد در میآیند و شکل قالب را به خود میگیرند.
به طور کلی، قالبها وسایلی هستند که برای ساخت و تولید قطعات مختلف با شکلهای دلخواه در فرآیندهای ریخته گری و قالب گیری به کار برده میشوند. به قالبهای مورد استفاده برای تولید انبوه قطعات در صنایع مختلف، قالب صنعتی میگویند.
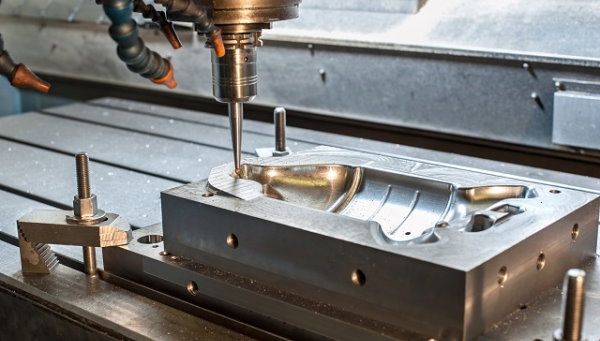
روش های قالب گیری کدام هستند؟
قالب گیری روشهای مختلفی دارد که هر یک در صنایع متفاوت مورد استفاده قرار میگیرند. از متداولترین روش های قالب گیری میتوان به ریخته گری، قالب گیری تزریقی، قالب گیری بادی، متالورژی پودر، تف جوشی، قالب گیری فشاری، قالب گیری اکستروژن یا برون ریزی، لایه سازی یا لمینت، قالب گیری ماتریسی، قالب گیری چرخشی، قالب گیری گریز از مرکز، قالب گیری انتقالی، قالب گیری حرارتی و قالب گیری فایبرگلاس اشاره کرد. قالبهای دایکاست، ریژه، ماسهای و تزریق پلاستیک کاربرد گستردهای در روشهای قالبگیری صنعتی دارند.
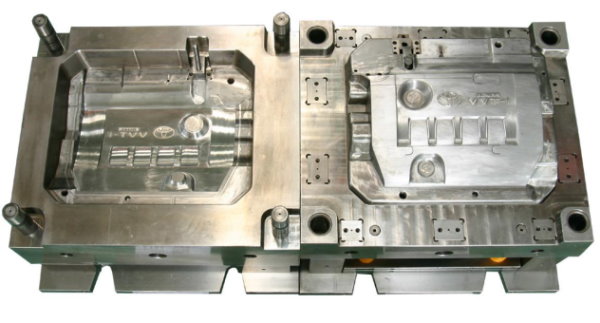
تفاوت قالب گیری با ریخته گری در چیست؟
در حالت کلی، ریخته گری به عنوان یکی از روش های متداول قالب گیری در نظر گرفته میشود. با این وجود، تفاوت اصلی بین اصطلاحات «قالب گیری» (Molding) و «ریخته گری» (Casting)، مواد مورد استفاده در فرآیند ساخت قطعات است.
ریخته گری معمولا به ساخت قطعات فلزی اشاره دارد. در صورتی که منظور از قالب گیری، فرآیند ساخت قطعات پلاستیکی، مخصوصا به روش تزریق پلاستیک است. این دو فرآیند شباهتها و تفاوتهای زیادی دارند که در بخشهای بعدی به آنها خواهیم پرداخت. شکل زیر، اجزای مختلف دستگاههای مورد استفاده در ریختهگری و قالبگیری تزریقی را نمایش میدهد.
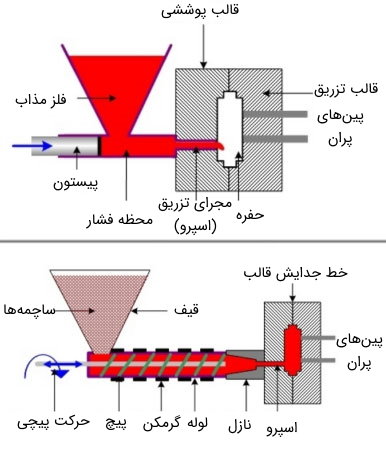
قالب چگونه ساخته میشود؟
ساخت و تولید یک قطعه با استفاده از روشهای قالب گیری نیازمند ساخت قالب های مخصوص آن قطعه است. این کار طی دو مرحله طراحی قطعه و طراحی قالب های صنعتی مخصوص آن انجام میگیرد. طراحی قالب های صنعتی مراحل متعددی دارد که در بخش بعدی به معرفی آنها میپردازیم.
مراحل طراحی قالب های صنعتی چه هستند؟
امکانسنجی و بررسی قابلیت ساخت، طراحی مدلهای اولیه دو بعدی و سه بعدی، طراحی نهایی، ساخت بخشهای اصلی و فرعی، به کارگیری قالب برای ساخت نمونه اولیه و اعمال اصلاحات نهایی به عنوان مراحل کلی طراحی قالب های صنعتی در نظر گرفته میشوند. در ادامه به معرفی هر یک از این مراحل میپردازیم.
مرحله اول: امکانسنجی و بررسی قابلیت ساخت
در اولین مرحله از فرآیند طراحی قالب، مهندسان بخشهای مختلف نظیر طراحی، ابزارسازی، متالورژی، ساخت، کنترل کیفیت و تکنسینهای آزمایشگاه به منظور تصمیمگیری راجع به مشخصات قطعه مورد نظر، عملکرد بخشهای مختلف قالب، جنس ماده سازنده قالب، محدودیتهای اجرایی و اقدامات لازم برای بهبود کیفیت کار با یکدیگر به تبادل نظر میپردازند. هدف اصلی این تیم، یافتن هر گونه مشکل احتمالی در هندسه قطعه، تلورانسهای ناشی از شرایط نامناسب قالب یا ابزارهای مورد نیاز به منظور دستیابی به خروجی مطلوب است. در این مرحله، جزئیاتی نظیر مشخصات رزین، جنس قالب، سیستم خنککاری، بهترین نوع دریچه، محل قرارگیری دریچه و محل تهویه مورد بررسی قرار میگیرند.
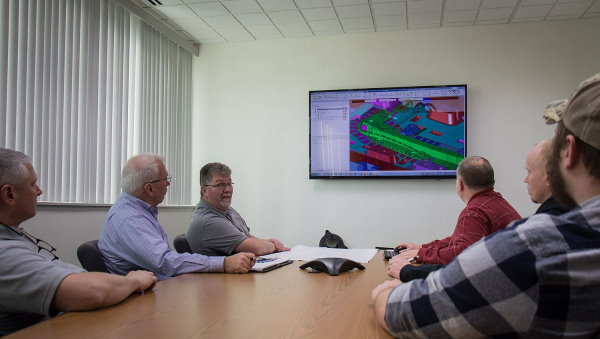
در انتهای مرحله امکانسنجی، به منظور بررسی قابلیت ساخت قالب و قطعه، دستورالعملهای استاندارد و دیتیل ساخت ابزارها جهت دستیابی به بهترین طراحی ممکن، مرور میشوند. سپس، تحلیل خطاهای احتمالی در فرآیند تولید با استفاده از روش «PFMEA» انجام میگیرد.
در صورت رضایتبخش نبودن نتایج تحلیل، گزینههای مختلف برای رفع خطاهای موجود بررسی میشوند. یکی از روشهای برطرف کردن خطاهای احتمالی، تکنیک خطاناپذیر سازی فرآیند یا «پوکایوکه» (Poka-Yoke) است.
مرحله دوم: طراحی اولیه و نهایی
پس از رفع خطاهای احتمالی و تایید نتایج تحلیل، طراحان با استفاده از نرم افزارهای تخصصی و مستندات جمعآوری شده، شروع به طراحی مدلهای دو بعدی و سه بعدی میکنند.
این مدلها به منظور تعیین ابعاد قالب و بخشهای مختلف آن مورد استفاده قرار میگیرند. در صورت تایید کارشناسان، جزئیات مدلهای طراحی شده نهایی میشوند.

مرحله سوم: تعیین مشخصات طراحی نهایی
در این مرحله، واحد ساخت و ماشین افزار، مشخصات طراحی نهایی را دریافت کرده و با در نظر گرفتن قابلیت ساخت و الزامات مربوط به ابعاد، تغییرات مورد نیاز را به قالب اعمال میکند.
مرحله چهارم: ساخت بخشهای اصلی و فرعی
در این مرحله، مستندات و نقشههای مربوطه تکمیل میشوند. سپس، دستورالعملها و استانداردهای ساخت مورد بررسی و تایید قرار میگیرند. روند کار واحد ابزارسازی به طور دقیق نظارت شده و جلسات کارگاهی در این زمینه برگزار میشوند. با اتمام ساخت بخشهای اصلی و فرعی قالب، نتیجه کار با استفاده از یک چک لیست جامع مورد ارزیابی قرار میگیرد. در انتهای مقاله، نمونهای از موارد موجود در چک لیست طراحی قالب های صنعتی را ارائه خواهیم کرد.
مرحله پنجم: تست کردن قالب برای ساخت نمونه
پس از تکمیل ساخت بخشهای اصلی و فرعی قالب، فرآیند قالبگیری و ساخت قطعه آزمایشی شروع میشود. پیش از شروع این فرآیند، بخش ساخت و تولید، پارامترهای اجرایی مناسب را مشخص میکند. سپس، ساخت نمونه اولیه با استفاده از اصول کاربردی انجام میگیرد. در انتها، کیفیت قطعه بررسی میشود.
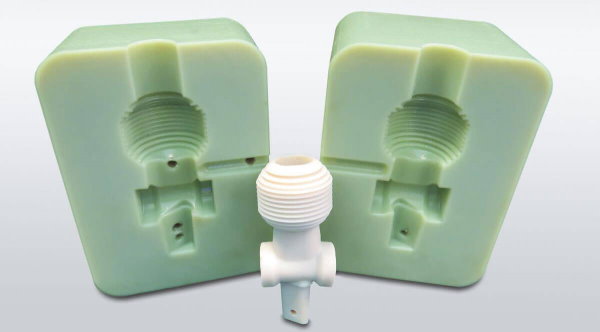
مرحله ششم: اعمال تغییرات نهایی
آخرین مرحله از طراحی قالب های صنعتی به اعمال تغییرات و اصطلاحات مورد نیاز اختصاص دارد. در این مرحله، نحوه ساخت قالب مورد تایید قرار میگیرد و جزئیات هر مرحله به صورت مستند در میآیند. مستندسازی، زمان تنظیم تجهیزات برای شروع تولید در مقیاس صنعتی را کاهش میدهد. در نهایت، قطعه ساخته شده برای تایید نهایی به مشتری ارسال میشود. پس از تایید مشتری، خط تولید با استفاده از قالب طراحی شده به راه میافتد.
در زمینه طراحی قالب های صنعتی با استفاده از نرم افزارهای تخصصی، فرادرس، چندین مجموعه آموزشی جامع و کاربردی را تهیه کرده است که میتوانند در شروع یادگیری این مبحث به شما کمک کنند. لینک این مجموعهها در ادامه آورده شده است:
انواع قالب های صنعتی کدام هستند؟
از پرکاربردترین قالب های صنعتی میتوان به قالب تزریق پلاستیک، قالب دایکاست، قالب ریژه و قالب ماسهای و قالب پرس اشاره کرد. هر یک از این قالبها برای فرآیندهای مختص به خود مورد استفاده قرار میگیرند. طراحی قالب های صنعتی نیازمند آشنایی با انواع، اجزا و مکانیزم عملکرد آنها است. در ادامه به معرفی ویژگیهای پرکاربردترین قالبهای صنعتی مورد استفاده برای تولید انبوه قطعات میپردازیم.
قالب تزریق پلاستیک چیست؟
«قالب تزریقی» (Injection Mold)، قالبی است که معمولا به منظور تولید انبوه قطعات پلاستیکی (چند هزار یا حتی چند میلیون قطعه در هر مرحله) مورد استفاده قرار میگیرد. در قالب گیری تزریقی، مواد مذاب به درون قالب هدایت میشوند. پس از سرد شدن مواد و تبدیل آنها به حالت جامد، قطعه مورد نظر به دست میآید. این روش ساخت و تولید قطعات در صنایع مختلفی نظیر صنایع غذایی، اتومبیل سازی، پزشکی، داروسازی، لوازم خانگی، صنایع الکترونیکی و غیره کاربرد دارد.
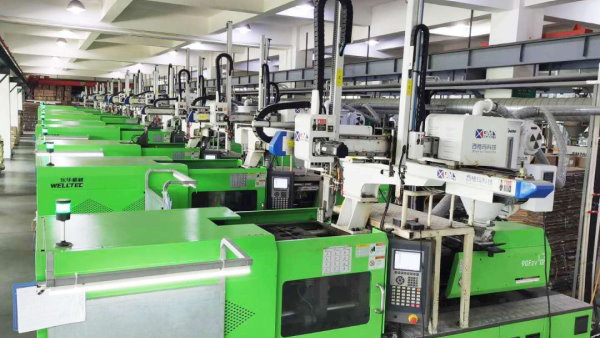
مراحل قالب گیری تزریقی چه هستند؟
آشنایی با روند اجرای قالبگیری تزریقی میتواند درک بهتری از جوانب مختلف طراحی قالبهای مورد استفاده در این فرآیند را به همراه داشته باشد. فرآیند قالبگیری تزریقی طی چند مرحله شامل بستن قالب، تزریق، خنک کردن، باز کردن قالب و خارج کردن قطعه انجام میگیرد. تصویر متحرک زیر، این فرآیند را به خوبی نمایش میدهد.
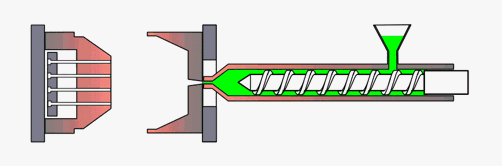
اجزای قالب تزریقی چه هستند؟
دستگاه قالب گیری تزریقی از دو واحد «کلمپینگ» (Clamping) و تزریق تشکیل میشود. بخش کلمپینگ وظیفه باز کردن قالب، خروج قطعه و بستن قالب را برعهده دارد. بخش تزریق نیز به منظور ذوب کردن ماده و انتقال آن به درون قالب مورد استفاده قرار میگیرد. تصویر زیر، اجزای مختلف دستگاه قالب گیری تزریقی را نمایش میدهد.
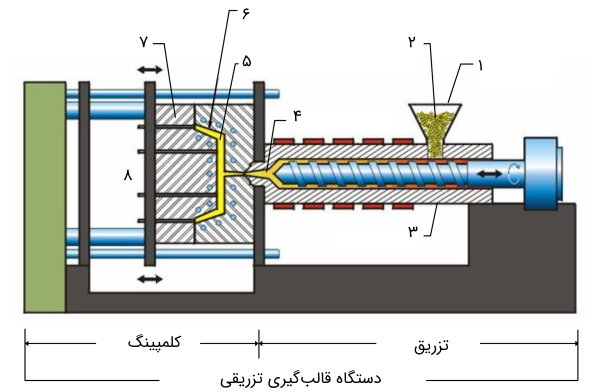
موارد نمایش داده شده در تصویر بالا عبارت هستند از:
- قیف
- مواد خام پلاستیکی به شکل گلوله یا اصطلاحا گندله
- لوله
- پلاستیک مذاب
- بخش قالبگیری شده
- حفره
- قالب
- پینهای پران برای رهاسازی قطعه خنک شدن از درون قالب
موارد بالا، بخشهای اصلی دستگاه قالب تزریق پلاستیک را تشکیل میدهند. علاوه بر این موارد، پیچ، شیر، سیلندر و اجزای متعدد دیگری نیز وجود دارند که عملکرد این روش ساخت قطعه را کامل میکنند. طراحی قالب های صنعتی با طراحی تمام اجزای مختلف یک قالب با توجه به عملکردهای مورد انتظار از آنها انجام میگیرد.
عوامل موثر بر طراحی قالب های تزریقی چه هستند؟
از مهمترین عوامل موثر بر کیفیت طراحی قالبهای تزریق پلاستیک میتوان به تنش و فشار در هنگام تزریق، نوع، محل قرارگیری و مکانیزم عملکرد دریچهها، ضخامت مناسب برای دیوارهها، زاویه خروج قطعه در هنگام باز کردن قالب، بافت سطح داخلی، آثار جریان مواد مذاب بر روی قطعه، خط جدایش قالب در هنگام باز و بسته کردن و نقصهای متداول اشاره کرد.
آشنایی با طراحی قالبهای تزریقی از اهمیت بسیار بالایی در ساخت و تولید قطعات پلاستیکی در صنایع مختلف برخوردار است. طراحی قالب های صنعتی با استفاده از نرم افزارهای تخصصی انجام میگیرد.
قالب ریخته گری چیست؟
«ریخته گری» (Casting)، فرآیندی است به منظور ایجاد قطعات فلزی با شکل دلخواه مورد استفاده قرار میگیرد. طی این فرآیند، فلز یا آلیاژ فلزی ذوب شده به درون قالب میریزند تا شکل آن را به خود بگیرد. سپس، به مواد مذاب اجازه سرد شدن میدهند. کاهش دمای مواد، تبدیل آنها از فاز مایع به فاز جامد را در پی دارد. ریخته گری یکی از قدیمیترین و متداولترین روشهای قالبگیری فلزات است که قدمت آن به بیش از 7000 سال پیش باز میگردد.
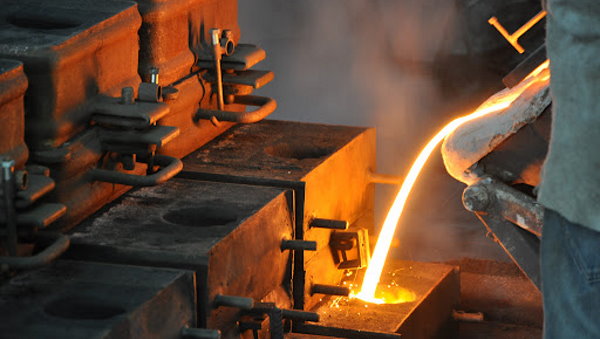
قالبهای ریخته گری در ساخت قطعات صنایع مختلفی نظیر اتومبیلسازی، هواپیماسازی، راهآهن، کشتیسازی، تجهیزات سنگین (ساختمانسازی، کشاورزی، معدنکاری)، ابزارهای ساخت، تجهیزات کارخانهای و نیروگاهی، تجهیزات الکترونیکی، تاسیسات بهداشتی و پایپینگ، لوازم خانگی و بسیاری از صنایع دیگر کاربرد دارند.
از روشهای مختلف ریختهگری میتوان به موارد زیر اشاره کرد:
- «قالب دایکاست» (Die Cast Mold): تزریق پرفشار فلز مذاب به درون حفره قالب فولادی
- «قالب ریژه» (Gravity Cast Mold): نفوذ مواد مذاب تحت نیروی ثقلی به درون قالبهای دائمی
- «قالب ماسه ای» (Sand Cast Mold): ریختن مواد مذاب به درون پوشش فلزی حاوی ماسه فشرده با الگوی دلخواه
از بین موارد بالا، ریختهگری ماسهای از کاربرد بیشتری برخوردار است.
مراحل ریخته گری چه هستند؟
ریخته گری، فرآیندی است که با ریختن مواد فلزی مذاب به درون یک قالب توخالی با شکل مشخص انجام میگیرد. کلیت ریخته گری تفاوت زیادی با دیگر روشهای قالب گیری ندارد. این فرآیند شامل طراحی و آمادهسازی قالب، ماهیچه زنی بخشهای قالب، قالبگیری، ذوب کردن، ریختن مواد مذاب و پرداخت سطح قطعه میشود. تصاویر متحرک زیر، فرآیند کلی ریختهگری با استفاده از قالبهای دایکاست و ماسهای را نمایش میدهند.
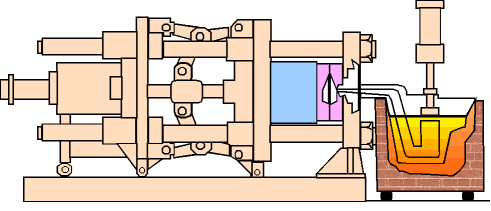
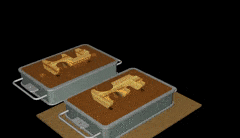
عوامل موثر بر طراحی قالب های ریخته گری چه هستند؟
عوامل متعددی بر روی طراحی قالب های صنعتی مورد استفاده در فرآیند ریختهگری تاثیر دارند که از مهمترین آنها میتوان به مشخصات فلز مورد استفاده، ابعاد مجاز، تلورانسها، پرداخت سطح، ضخامت دیوارهها، زاویه خروج، دندانهها، حفرهها و علائم تجاری مشتری اشاره کرد.
قالب آهنگری چیست؟
«آهنگری» (Forging) یکی از پرکاربردترین فرآیندهای شکلدهی به فلزات با استفاده از اعمال نیروی فشاری و ضربه به نقاط مشخصی از یک قطعه فلزی داغ است.
روشهای مختلفی برای آهنگری فلزات وجود دارد که از متداولترین آنها میتوان به روش آهنگری با قالب باز و آهنگری با قالب بسته اشاره کرد:
- آهنگری با قالب باز: در این روش، شکل ابزار به شکل نهایی بستگی ندارد و تغییر شکل بر روی قسمتی از قطعه یا کل آن انجام میشود. در برخی از موارد، محصول آهنگری با قالب باز به عنوان ماده اولیه آهنگری با قالب بسته مورد استفاده قرار میگیرد.
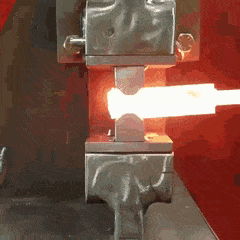
- آهنگری با قالب بسته: در این روش، شکل مورد نظر با اعمال فشار از طریق قالب به تمامی بخشهای قطعه حاصل میشود. آهنگری با قالب باز در ساخت قطعات اولیه و نهایی با اشکال ساده تا پیچیده و وزنهای سبک تا سنگین کاربرد دارد.
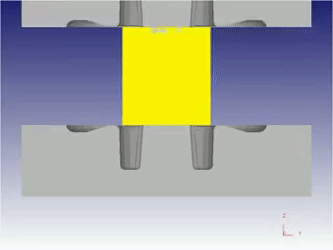
عوامل موثر بر طراحی قالب های آهنگری چه هستند؟
بحث طراحی قالبهای آهنگری بیشتر در روش آهنگری با قالب بسته مورد توجه قرار میگیرد. در این روش، جنس قطعه، عملیات حرارتی، موقعیت قرارگیری قطعه و قالب، پرداخت سطح، شکل هندسی، نحوه تغییر شکل و نحوه توزیع بار اشاره کرد.
قالب پرس چیست؟
قالب پرس، یکی از انواع قالبهای بسته مورد استفاده در فرآیند شکلدهی به فلزات است. این قالبها از دو بخش بالایی و پایینی تشکیل میشوند. در فرآیند شکلدهی به وسیله قالبهای پرس، قطعه بین دو قالب بالایی و پایینی قرار میگیرد.
اعمال تدریجی فشار به قطعه، آن را به شکل دلخواه در میآورد. قالب پرس در شکلدهی فلزات و تولید قطعات در مقیاس بزرگ کاربرد دارد.
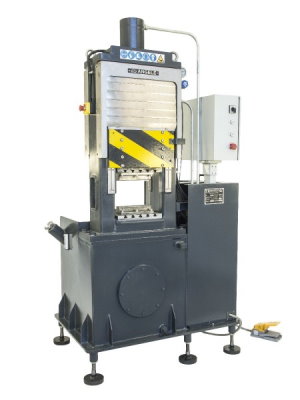
فرآیند شکلدهی به ورقهای فلزی از مهمترین فرآیندهای صنعتی است که معمولا توسط دستگاههای پرس انجام میشود. نرم افزارهای تخصصی طراحی قالب های صنعتی، امکان مدلسازی، تحلیل و طراحی انواع سیستمهای قالب گیری نظیر سیستم پرس را فراهم میکنند.
عوامل موثر بر طراحی قالب های صنعتی کدام هستند؟
عوامل متعددی بر روی طراحی قالب های صنعتی و کیفیت قطعه به دست آمده تاثیرگذار میگذارند. با این وجود، به دلیل متفاوت بودن بخشهای مختلف انواع قالبها، پارامترهای مشترکی نظیر دریچه، زاویه خروج قطعه، بافت سطح و قابلیت ساخت از اهمیت بیشتری برخوردار هستند. در ادامه به معرفی این موارد میپردازیم.
نقش جنس قالب در در طراحی قالب های صنعتی
اکثر قالب های صنعتی از جنس فولاد آبدیده هستند. فولاد آبدیده، مقاومت بسیار خوبی در برابر فرسودگی دارد. آلومینیوم نیز در برخی از موارد به عنوان ماده سازنده قالب های صنعتی مورد استفاده قرار میگیرد. با این وجود، دوام قالبهای فولادی و نرخ بالای تولید پیش از نیاز به تعویض، این قالبها را به گزینه اول در اکثر واحدهای صنعتی تبدیل میکند.
البته هزینه قالبهای فولادی نسبت به قالبهای آلومینیومی بیشتر است و این مسئله باید در مرحله امکانسنجی پیش از طراحی قالب های صنعتی مورد توجه قرار گیرد. در نهایت، فولاد و آلومینیوم به عنوان دو گزینه اصلی برای ساخت قالب های صنعتی در نظر گرفته میشوند.
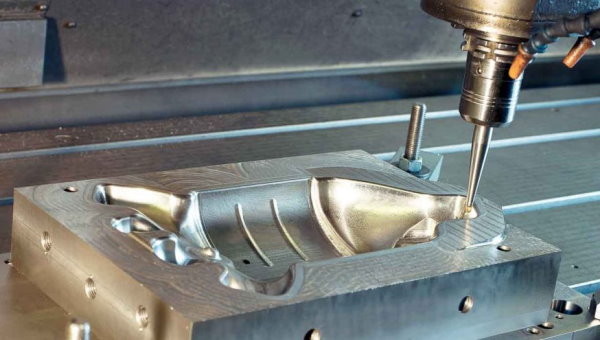
قابلیت ماشینکاری، زمان کمتر ساخت قالب و امکان تغییر سریع چرخههای تولید را میتوان به عنوان مزیتهای آلومینیوم نسبت به فولاد در نظر گرفت. اگرچه، قابلیت جوشکاری پایین، نگهداری دشوارتر و فرسایش سریع آلومینیوم، محدودیتهایی هستند که این ماده را به منظور ساخت قالبهای مورد استفاده در تولید نمونههای آزمایشی یا تولید در بازههای زمانی کوتاه مناسب میکنند. در برخی از موارد، قالب های صنعتی به صورت ترکیبی از قطعات فولادی و آلومینیومی طراحی میشوند. قطعات آلومینیومی در این قالبها نقش انتقال بهتر حرارت را برعهده دارند.
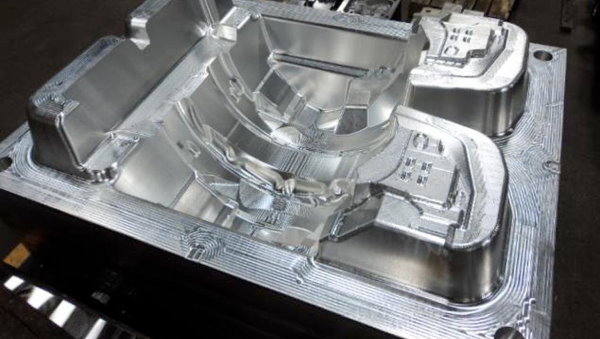
در صورت پیچیده یا سخت بودن قطعات مورد نظر، استفاده از آلومینیوم گزینه مناسبی نخواهد بود. آلیاژهای مسی در این موارد میتوانند وظیفه مواد انتقال دهنده حرارت در قالبهای ترکیبی را بر عهده داشته باشند. پوششدهی قالب های صنعتی از روشهایی است که به منظور بهبود مقاومت فولاد و آلومینیوم در برابر فرسایش مورد استفاده قرار میگیرد.
نقش دریچه قالب در طراحی قالب های صنعتی
دریچهها، بخشهایی هستند که جریان مواد مذاب را به درون حفر قالب هدایت میکنند. ابعاد و شکل دریچههای قالب به طراحی قطعه و آن بستگی دارند. طراحان باید پارامترهای متعددی را برای تعیین نوع و محل قرارگیری دریچه در نظر بگیرند. این موارد بر روی دستیابی به جریان مواد مذاب، فشار پرکنندگی، زمان خنک شدن و تلورانس/ابعاد تاثیر میگذارند. محل قرارگیری دریچه نباید عمکلرد قطعه یا ظاهر آن را تحت تاثیر قرار دهد.
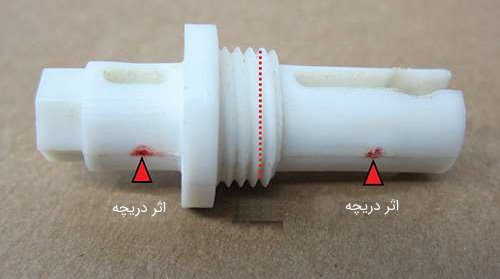
نقش زاویه خروج قطعه در طراحی قالب های صنعتی
از مهمترین جنبههای در طراحی قالب های صنعتی میتوان به راحتی خروج قطعه نهایی بدون هیچ گونه آسیبی به سطح آن اشاره کرد. این هدف با ایجاد یک زاویه خروج مناسب به دیواره قالب محقق میشود. میزان زاویه خروج به عوامل مختلفی نظیر طراحی قطعه، جنس مواد، عمق حفره قالب، پرداخت سطح، بافت سطح و میزان جمع شدگی مواد بستگی دارد. معمولا دیوارهها با چند درجه (حدود 1 تا 5 درجه) زاویه طراحی میشوند تا در هنگام باز شدن قالب، فضای کافی برای خروج راحت قطعه فراهم شود. به طور کلی، هرچه عمق حفره قالب بیشتر باشد زاویه شیب مورد نیاز نیز بیشتر خواهد بود.
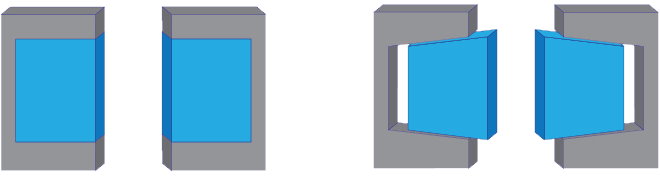
نقش پرداخت و بافت سطح در طراحی قالب های صنعتی
خنکسازی قالب و قطعه درون آن از اصلیترین عوامل موثر بر پرداخت سطح قطعه هستند. به عنوان مثال، دستیابی به یک سطح صاف و هموار بر روی یک ماده رزینی با محتوای 50 درصد شیشه با کنترل دما در حین فرآیند قالب گیری ممکن میشود. در این حالت، سطح قطعه باید کاملا رزینی بوده و در عمق کم، مواد فایبرگلاس وجود داشته باشند. این نتیجه با افزایش زمان خنک سازی به میزان 10 درصد به دست میآید. طراحی قالب های صنعتی میتواند به گونهای باشد که باعث ایجاد بافت و الگوهای مشخص بر روی سطح قطعه شود. به عنوان مثال، در صورت نیاز به حکاکی لوگوی شرکت سازنده بر روی قطعه، طراحی مناسب لوگو بر روی سطح قالب، این مرحله را از فرآیند تولید حذف میکند.
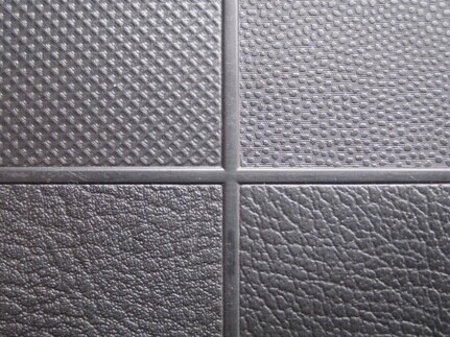
در برخی از موارد، بافت مناسب، عملکرد قطعه را بهبود میبخشد. به عنوان مثال، بافت زبر، برداشتن قطعه را راحتتر میکند و بافت صیقلی، فرسایش قطعه را کاهش میدهد. سطح مات، صیقلی، گرافیکی، دانهای، دارای لوگو و دارای الگوهای هندسی از گزینههای قابل اجرا هستند. با توجه به نوع، عمق و محل قرارگیری بافت سطح، امکان نیاز به زاویه خروج برای رهاسازی راحت قطعه وجود خواهد داشت. تمام این موارد در حین طراحی قالب های صنعتی در نظر گرفته میشوند.
نقش قابلیت ساخت و هزینه در طراحی قالب های صنعتی
هدف اصلی از طراحی قالب های صنعتی و ابزارسازی، ایجاد قطعهای است که قابلیت ساخت بالایی دارد. قابلیت ساخت بالا به معنای یک فرآیند تولید با کیفیت، ساده، کارآمد، بادوام و با نگهداری آسان است. چنین فرآیندی دستیابی به تمام مشخصات مورد نظر مشتری را با کمترین هزینه امکانپذیر میکند. به منظور تحقق این هدف، انتخاب ماشین افزار مناسب باید در مراحل اولیه طراحی قالب های صنعتی صورت بگیرد. به همین دلیل، وجود ابزارساز در تیم طراحی و کارگاه ماشین افزار مجهز در کارخانه ضروری است. بهترین رویکرد برای بهرهمندی حداکثری از ابزارهای موجود، برنامه ریزی بر اساس هزینه هر چرخه تولید است.
نرم افزارهای طراحی قالب های صنعتی کدام هستند؟
از پرکاربردترین نرم افزارهای مورد استفاده برای طراحی قالب های صنعتی میتوان به «سالیدورکس» (SolidWorks)، «کَتیا» (CATIA) و «اینونتور» (Inventor) اشاره کرد. این نرم افزارها با قابلیتها، ابزارها و افزونههای تخصصی خود، امکان مدلسازی، تحلیل و طراحی انواع قالبها و قطعات مکانیکی را فراهم میکنند. در این میان، سالیدورکس از محبوبیت بیشتری نزد طراحان حرفهای برخوردار است. البته کتیا و اینونتور نیز ابزارهای قدرتمندی دارند که آنها را به گزینههای بعدی برای طراحی قالب های صنعتی تبدیل میکنند.
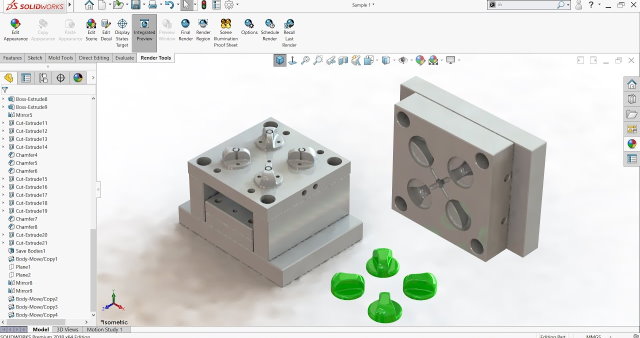
برای آشنایی با مبانی طراحی قالب در سالیدورک، مطالعه مطلب «طراحی قالب در سالیدورک — آموزش گام به گام» را به شما پیشنهاد میکنیم.
معرفی مجموعه فیلم های آموزش نرم افزارهای طراحی قالب های صنعتی
آشنایی با طراحی قالب های صنعتی، یکی از مهمترین مهارت های مهندسی مکانیک (ساخت و تولید)، متالورژی و قالبسازی است. مبانی طراحی قالب، بخصوص طراحی قالبهای پرس، پلاستیک، ریختهگری و آهنگری، طی درسهای تئوری و عملی در مقاطع کارشناسی و کارشناسی ارشد رشتههای مذکور آموزش داده میشوند. از اینرو، یادگیری مهارت طرحی قالب های صنعتی، علاوه بر پیشرفت درسی، زمینه موفقیت شغلی و یافتن فرصتهای بهتر را فراهم میکند. به این منظور، فرادرس، چندین فیلم آموزشی جامع و کاربردی را برای یادگیری اصول طراحی قالب های صنعتی و ریخته گری تهیه کرده است که میتوانند در یادگیری این مباحث به شما کمک کنند. لینک مشاهده این فیلمها در ادامه آورده شده است:
- برای مشاهده مجموعه فیلمهای آموزش سالیدورکس (SOLIDWORKS) + اینجا کلیک کنید.
- برای مشاهده فیلم آموزش طراحی قالب های تزریق پلاستیک با سالیدورکس + اینجا کلیک کنید.
- برای مشاهده فیلم آموزش طراحی قالب های پرس با نرم افزار لوگوپرس + اینجا کلیک کنید.
- برای مشاهده فیلم آموزش آشنایی با قالب کششی و طراحی آن در نرم افزار سالیدورکس + اینجا کلیک کنید.
- برای مشاهده فیلم آموزش پروژه محور سالیدورکس - طراحی قالب خمش + اینجا کلیک کنید.
- برای مشاهده فیلم آموزش پروژه محور SOLIDWORKS - طراحی قالب برش + اینجا کلیک کنید.
- برای مشاهده مجموعه فیلمهای مجموعه آموزش کتیا (CATIA) + اینجا کلیک کنید.
- برای مشاهده فیلم آموزش پروژهمحور CATIA (کتیا) - طراحی قالبهای تزریق پلاستیک + اینجا کلیک کنید.
- برای مشاهده فیلم آموزش نرم افزار اینونتور (INVENTOR) - طراحی قالبهای پلاستیک + اینجا کلیک کنید.
- برای مشاهده فیلم آموزش شبیهسازی فرآیندهای ریختهگری با نرم افزار پروکست + اینجا کلیک کنید.
چک لیست طراحی قالب های صنعتی قالب گیری تزریقی
پس از طراحی و ساخت قالب صنعتی، کیفیت قالب توسط چک لیستهای مخصوص مورد ارزیابی قرار میگیرد. در ادامه، موارد موجود در نمونهای از یک چک لیست طراحی قالبهای تزریقی را معرفی میکنیم.
- آیا از آخرین دادههای قطعه برای طراحی استفاده شده است؟
- آیا حفرههای قالب با برگه مشخصات فنی مطابقت دارند؟ آیا نقشه آنها معقول است؟
- آیا نرخ جمعشدگی با برگه مشخصات فنی همخوانی دارد؟
- آیا فاصله بین پینهای پران برای رهاسازی قطعه کافی است؟
- آیا میزان مواد پرکننده کافی است؟
- آیا نحوه باز و بسته شدن قالب و ابعاد صفحات آن با نیازهای مشتری همسان است؟
- آیا اجزای استاندارد با برگه مشخصات فنی مطابقت دارند؟
- آیا مدل و ابعاد حفره پیچهای قلابدار مناسب و مطابق با درخواست مشتری است؟
- آیا طراحی مناسب برای پیچهای قلابدار در صورت بیشتر بودن وزن قالب از 25 کیلوگرم انجام شده است؟
- آیا الزامات خاصی برای گریسکاری وجود دارد؟ آیا این الزامات مطابق با خواسته مشتری است؟
- آیا تجهیزات ایمنی مطابق خواسته مشتری یا استانداردهای موجود طراحی شدهاند؟
- آیا شعاع اسپرو با برگه مشخصات فنی یکسان است؟
- آیا شعاع حلقه جانمایی با برگه مشخصات فنی همخوانی دارد؟
- آیا نحوه ساخت مولفههای باز و بسته کردن قالب به خوبی انجام گرفته است؟
- آیا جنس مواد پوششدهنده صفحات مطابق با خواسته مشتری است؟
- آیا ابعاد و الگوی رزوههای رهاساز قالب و صفحه رهاساز با خواسته مشتری مطابقت دارد؟
- آیا امکان استفاده از قالب به صورت خودکار در خط تولیدهای مکانیزه وجود دارد؟
- آیا زاویه خروج مناسب بین تمام چفت و بستها در نظر گرفته شده است؟
- آیا شرایط فولاد اجزای مختلف مناسب است؟ در غیر اینصورت، آیا نیازی به اجزای یدکی وجود دارد؟
- در صورت بزرگتر بودن ابعاد حفره و مغزی تزریق از 300 میلیمتر، آیا بلوک گوهای در نظر گرفته شده است؟
- آیا حفره و مغزی تزریق به خوبی در یکدیگر چفت میشوند؟
- آیا عمق سیستم تهویه با برگه اطلاعات مواد مطابقت دارد؟
- آیا خط لوله آب مناسب و کافی است؟
- آیا کانکتور آب با سفارش مشتری مطابقت دارد؟
- آیا تمام ابعاد رزوههای خط لوله آب در نقشهها آورده شدهاند؟
- آیا جهتگیری ورودی و خروجی مطابق خواسته مشتری است؟
- آیا مشتری درخواستی برای تعبیه منیفولد آب داده است؟
- آیا تمام مسیرهای ورودی و خروجی هوا و روغن در نقشهها ذکر شدهاند؟
- آیا کانکتور روغن با سفارش مشتری همخوانی دارد؟
- آیا ابعاد راهگاه گرم با برگه مشخصات فنی یکسان است؟
- آیا نوع و ابعاد دریچه با برگه مشخصات فنی مطابقت دارد؟
- آیا محل طراحی دریچه مطابق با خط جدایش و برگه مشخصات فنی است؟
- آیا مشخصات سیستم راهگاه گرم با برگه مشخصات فنی تطابق دارد؟
- در صورت سفارش دریچه دارای ولو، آیا نوع ولو از نوع هیدولیکی یا پنوماتیکی انتخاب شده است؟
- آیا نوع کانکتورهای سیستم راهگاه گرم با سفارش مشتری مطابقت دارد؟
- آیا کانکتور سیستم راهگاه گرم در محل مناسب نصب شده است؟
- آیا نمودار سیمکشی سیستم راهگاه گرم در نقشهها آورده شده است؟
- آیا مواد اولیه مورد استفاده برای ساخت اجزای مختلف قالب مناسب هستند؟
- آیا سختی تمام اجزای قالب مناسب است؟
- آیا نقشهها دارای متره و برآورد کامل هستند؟
- آیا برای تمام اجزای استاندارد، شماره کاتالوگ در نظر گرفته شده است؟
- آیا محدوده خالی بین بوش تزریق با قالب و حفر وجود ندارد؟
- آیا اطلاعات مربوط به پرداخت در نقشهها ذکر شدهاند؟
در هنگام کنترل کیفیت و بررسی نتیجه طراحی قالب های صنعتی سوالات بسیار بیشتری باید جواب داده شوند. این سوالات به عملکرد مورد انتظار مشتری از قالب و مستندات جمعآوری شده توسط تیم طراحی و ساخت بستگی دارند.