سیمان چیست و چگونه ساخته می شود؟ | هر آنچه باید بدانید
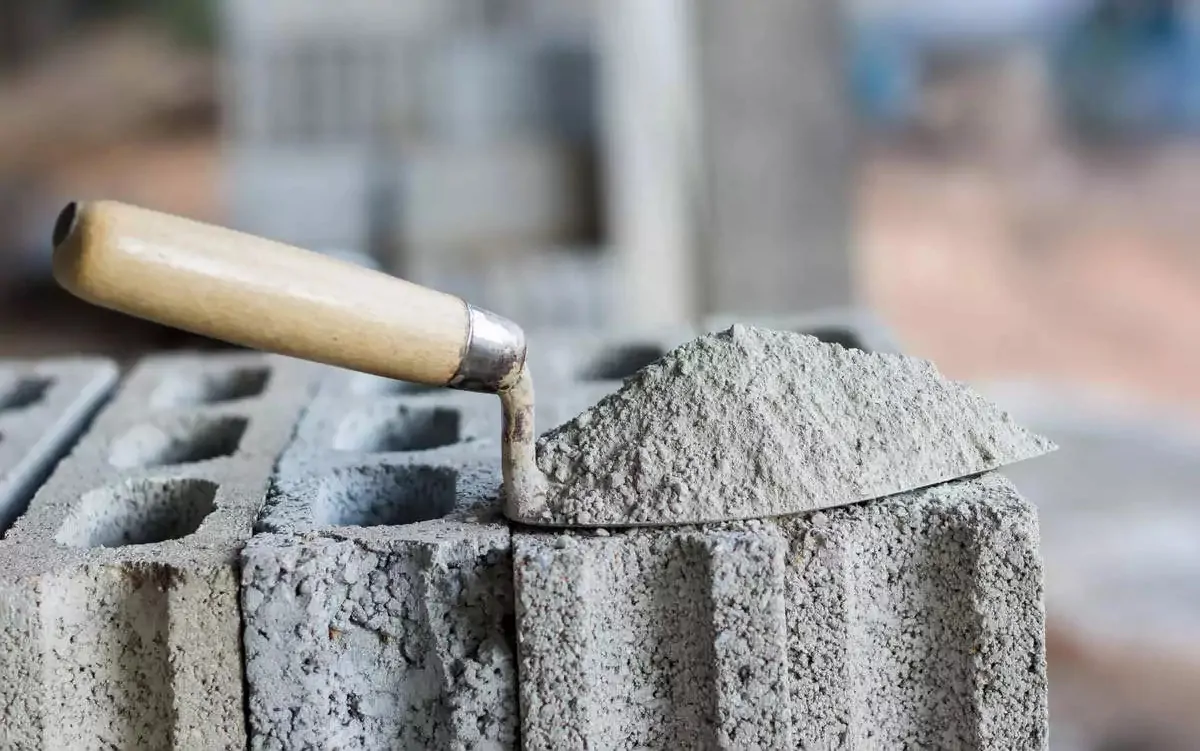
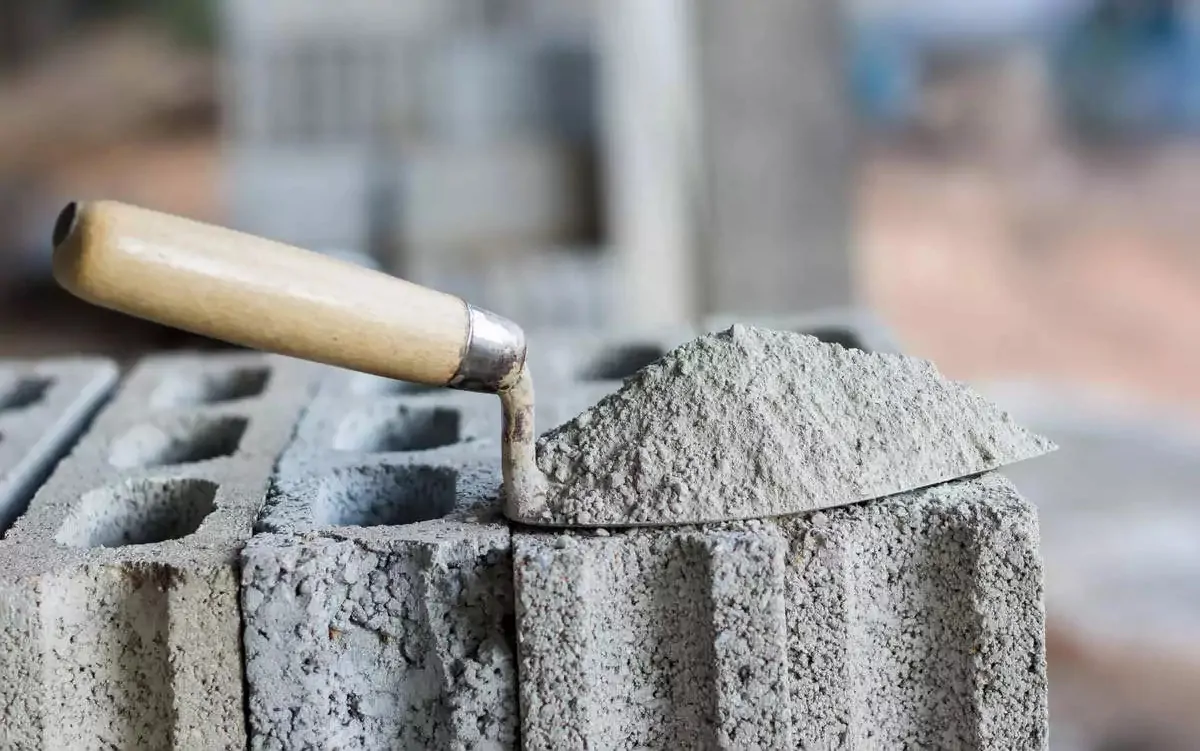
«سیمان» (Cement)، یکی از مهمترین مواد مورد استفاده در مصالح ساختمانی است. این ماده برای ساخت دوغاب، ملات و بتن مورد استفاده قرار میگیرد. در این مقاله، به معرفی کامل تاریخچه، تعریف، اجزا تشکیل دهنده، مراحل تولید، کاربردها، خواص فیزیکی، خواص شیمیایی و انواع سیمان میپردازیم.
تاریخچه استفاده از سیمان به چه دورانی باز می گردد؟
از زمان ظهور تمدن بشری تا به امروز، سیمان به شکلهای مختلفی مورد استفاده قرار گرفته است. توسعه سیمان از خاکسترهای آتشفشانی، ژیپس (سنگ گچ) سوخته، آهک آبدار و اولین سیمان هیدرولیکی مورد استفاده توسط رومیان در قرون وسطی تا قرن 18 میلادی (قرن 11 شمسی) ادامه داشت. در این قرن، «جیمز پارکر» (James Parker)، حق اختراع سیمان رومی را به نام خود ثبت کرد. این سیمان در آن دوران از شهرت بالایی برخوردار بود. با این وجود، در دهه 1850 میلادی (دهه 1230 شمسی)، محصول جدیدی با نام «سیمان پرتلند» (Portland Cement) جای سیمان رومی را گرفت.
در قرن 19 میلادی (قرن 12 شمسی)، تحقیقات و نوآوریهای زیادی بر روی نحوه ساخت و کاربرد سیمان پرتلند انجام شد. در این دوران، «ویلیام اسپدین» (William Aspdin)، سیمان پرتلند جدیدی را گسترش داد که خیلی زود مورد توجه قرار گرفت. با این وجود، «ایزاک چارلز جانسون» (Isaac Charles Johnson) به عنوان پدر سیمان پرتلند شناخته میشود. این فرد با معرفی روشی برای ساخت سیمان پرتلند در کوره، مشارکت بزرگی در تاریخ سیمان داشته است.
در قرن 19 میلادی، «سیمان رزندیل» (Rosendale Cement) در شهر نیویورک ساخته شد. به دلیل سختی مناسب این سیمان رزندیل، این نوع سیمان در اوایل عرضه با تقاضای بالا مواجه بود اما به دلیل طولانی بودن زمان گیرش آن، سیمان پرتلند بار دیگر به گزینه اول مصرف کنندگان تبدیل شد. امروزه برای ساخت بزرگراه و پل، از ترکیب سیمان رزندیل-پرتلند استفاده میشود. این ترکیب دارای دوام بالا و زمان گیرش پایین است.
سیمانی که اکنون در ساخت سازههای مختلف مورد استفاده قرار میگیرد، نتیجه آزمایشها، تغییرها و پیشرفتهای قابل توجهی است. هدف از تغییر ترکیب سیمان در سالهای گذشته، دستیابی به محصولی مستحکم و بادوام برای ساخت جاده، آزاد، پل و دیگر سازهها بوده است. اکثر سیمانهای امروزی از سیمان پرتلند به عنوان ترکیب اصلی یا یکی از ترکیبات اصلی خود استفاده میکنند.
سیمان چیست؟
سیمان، یکی از مهمترین مصالح ساختمانی ساخته دست بشر است که به منظور اتصال اجزا مختلف یک سازه نظیر سنگ، آجر، کاشی و غیره مورد استفاده قرار میگیرد. علاوه بر این، سیمان یکی از ترکیبات اصلی بتن در ساخت سازههای مختلفی مانند پل، سد، ساختمانهای مسکونی، ساختمانهای تجاری و دیگر سازههای بتنی است. ساختار اصلی سیمان، از مواد معدنی نظیر سنگ آهک، رس یا ماسه، بوکسیت و کانی آهن تشکیل میشود.
کلینکر چیست؟
با حرارت دادن به مواد خام مورد استفاده در تولید سیمان، مادهای به نام «کلینکر» (Clinker) به وجود میآید. با آسیاب کردن این ماده و افزودن ترکیباتی نظیر گچ به آن، سیمان تشکیل میشود. در بخشهای بعدی، به تشریح نحوه ساخت کلینکر خواهیم پرداخت.
مواد اولیه سیمان کدام هستند؟
سیمان، از هشت ماده اصلی آهک، سیلیکا، آلومینا، مگنزیا، اکسید آهن، سولفات کلسیم، سولفور تری اکسید و آلکالین (نمک قلیایی) تشکیل میشود. مواد مورد استفاده برای ساخت سیمان، خواص شیمیایی و فیزکی آن را تعیین میکنند.
از اینرو، آشنایی با این مواد از اهمیت بالایی برخوردار است. به منظور آشنایی با ترکیبات سیمان، باید نقش و عملکرد هر ماده را به خوبی مورد بررسی قرار داد. تغییر میزان مواد اصلی و افزودنیها در حین فرآیند تولید میتواند بر روی کیفیت مورد نظر تاثیر داشته باشد. هشت ماده اصلی تشکیل دهنده سیمان در تصویر زیر نمایش داده شده است.
جدول زیر، درصد استفاده از مواد اصلی در ترکیب سیمانهای معمولی را نمایش میدهد:
ماده | درصد به کار رفته در سیمانهای معمولی |
آهک | 60-65 |
سیلیکا | 17-25 |
آلومینا | 3-8 |
مگنزیا | 1-3 |
اکسید آهن | 0.5-6 |
سولفات کلسیم | 0.-0.5 |
سولفور تری اکسید | 1-3 |
آلکالین | 0-1 |
عملکرد اجزا تشکیل دهنده سیمان چگونه است؟
در این بخش، به معرفی عملکردها، مزایا و معایب هر یک از اجزا اصلی سیمان میپردازیم.
نقش آهک در سیمان چیست؟
ماده کلسیم اکسید (CaO) یا کلسیم هیدروکسید (Ca(OH2)) با عنوان آهک شناخته میشود. این ماده، یکی از اجزا اصلی مورد استفاده در ساخت سیمانهای مختلف است. با اضافه کردن مقدار کافی آهک به درون ترکیب سیمان، سیلیکات و آلومینات کلسیم تشکیل میشود. در صورت کافی نبودن مقدار آهک، مقاومت و زمان گیرش کاهش مییابد. در طرف مقابل، آهک زیاد باعث تورم و کاهش سلامت میشود.
نقش سیلیکا در سیمان چیست؟
سیلیسیم دی اکسید (SiO2) یا سیلیکا، یکی دیگر از مواد مهم در ترکیب سیمانها است. اضافه کردن مقدار مناسبی از این ماده به درون ترکیب باعث تشکیل سیلیکات دی کلسیم و تری کلسیم میشود. ویژگی استحکام سیمان، از سیلیکا موجود در آن نشات میگیرد.
نقش آلومینا در سیمان چیست؟
آلومینا همان اکسید آلومینیوم با فرمول شیمیایی Al2O3 است. زمان گیرش، به میزان آلومینای موجود در ترکیب سیمانها بستگی دارد. دمای تشکیل کلینکر در حضور مقدار کافی آلومینا کاهش مییابد. استفاده بیش از حد آلومینا باعث کاهش استحکام میشود.
نقش مگنزیا در سیمان چیست؟
اکسید منیزیوم (MgO) با عنوان مگنزیا شناخته میشود. این ماده نیز بر روی استحکام تاثیرگذار است. استفاده بیش از 2 درصد مگزنیا در ترکیب سیمان، کاهش استحکام را به همراه خواهد داشت.
نقش اکسید آهن در سیمان چیست؟
اکسید آهن (Fe2O3) به سیمان رنگ میدهد. این ماده به عنوان یک کمک ذوب در ترکیب سیمانها مورد استفاده قرار میگیرد. در دماهای خیلی بالا، اکسید آهن در واکنش بین کلسیم و آلومینیوم شرکت میکند و باعث تشکیل تری کلسیم آلومینو فریت میشود. محصول این واکنش، بر روی سختی و استحکام تاثیر میگذارد.
نقش سولفات کلسیم در سیمان چیست؟
سولفات کلسیم (CaSO4)، به شکل ژیپس (سنگ گچ) با فرمول شیمیایی CaSO4.2H2O در ترکیب سیمانها ظاهر میشود. تاثیر اصلی سولفات کلسیم بر روی کاهش زمان گیرش است.
نقش سولفور تری اکسید در سیمان چیست؟
سولفور تری اکسید (SO3) با مقادیر کمتر از 2 درصد در ساخت سیمانها مورد استفاده قرار میگیرد. این ماده بر روی مقاومت در برابر اثرات مخرب شیمیایی سولفاتها و همچنین میزان جمع شدگی تاثیر میگذارد. استفاده بیشتر از 2 درصد سولفور تری اکسید میتواند باعث کاهش سلامت سیمان شود.
نقش آلکالین در سیمان چیست؟
آلکالین یا قلیا (نمکهایی مانند Na2O یا K2O)، به منظور کنترل فرآیندهای شیمیایی و همچنین کاهش میزان نفوذیری سیمانها مورد استفاده قرار میگیرد. استفاده بیش از اندازه (بیش از 1 درصد) آلکالین میتواند باعث شوره زدن سطح ملات شود.
سیمان چگونه ساخته می شود؟
سیمان، طی شش مرحله اصلی شامل استخراج مواد خام از معادن، آسیاب کردن (به همراه توزین و مخلوط کردن)، اعمال حرارت اولیه، حرارت دادن در کوره، خنک سازی (به همراه آسیاب نهایی) و بسته بندی (به همراه انتقال به انبار) ساخته میشود. در ادامه، تمام مراحل اصلی ساخت سیمان را توضیح میدهیم.
مرحله اول: استخراج مواد خام سیمان از معادن
مواد خام مورد نیاز برای تولید سیمان، شامل سنگ آهک، ماسه یا رس (سیلیسیم، آلومینیوم، آهن)، شیل، خاکستر بادی، بوکسیت و غیره است. این مواد، سنگهای معدنی هستند که پس از استخراج، توسط سنگ شکن به قطعاتی با ابعاد حدود 15 سانتیمتر تبدیل میشوند. در مرحله بعدی، این قطعات برای رسیدن به ابعاد حدود 7 سانتیمتر در فرآیند سنگ شکنی ثانویه قرار میگیرند. به این ترتیب، قطعات سنگی خرد شده برای مرحله بعدی آماده میشوند.
مرحله دوم: آسیاب، توزین و مخلوط کردن
با آسیاب کردن مواد اولیه خرد شده در مرحله قبل و اضافه کردن مواد شیمیایی و افزودنیهای مورد نظر، یک مخلوط همگن کوچکتر تشکیل میشود. توزین ذرات در این مرحله با توجه به خواص مورد نیاز صورت میگیرد. معمولا 80 درصد این مخلوط از سنگ آهک و 20 درصد باقیمانده آن از رس تشکیل میشود. فرآیند خشک کردن مخلوط مواد خام نیز تا رسیدن رطوبت آن به زیر 1 درصد در کارخانه صورت میگیرد. سپس، غلتکهای بزرگ و میزهای گردان، مخلوط مواد خام را خرد کرده و بهم میزنند. در نهایت، پودر ریزی به دست میآید که برای انتقال به کوره آماده است.
مرحله سوم: اعمال حرارت اولیه به مواد خام
برای اعمال حرارت اولیه، مواد خام به محلی با چندین سیکلون انتقال داده میشوند. این سیکلونها با استفاده از گازهای داغ تولید شده از طرف کوره، حرارت اولیه را به مواد خام انتقال میدهند. هدف از این فرایند، کاهش مصرف انرژی و آلودگی محیط زیستی است. در این مرحله، مواد خام با عبور از سیکلونها به مواد اکسیدی تبدیل شده و آماده پخت در کوره میشوند.
مرحله چهارم: پخت مواد خام در کوره (تشکیل کلینکر)
در فرآیند تولید سیمان، پخت مواد خام در کوره، اصلیترین مرحله به شمار میرود. در این مرحله، طی انجام چندین واکنش شیمیایی بین ترکیبات کلسیم و سیلیسیم دی اکسید، مادهای به نام کلینکر تشکیل میشود.
با وجود پیچیده بودن این فرآیند، مراحل تولید کلینکر را میتوان به صورت زیر خلاصه کرد:
- تبخیر آب آزاد
- تبخیر آب موجود در ترکیبات رسی
- تبدیل کربنات کلسیم (CaCO3) به اکسید کلسیم (CaO) طی فرآیند کلسیناسیون
- تشکیل دی کلسیم سیلیکات بر اثر واکنش CaO با سیلیسیوم
- تشکیل فاز مایع بر اثر واکنش CaO با آلومینیوم و ترکیبات دارای آهن
- تشکیل دانههای کلینکر
- تبخیر مواد فرار (نظیر سدیم، پتاسیم، کلریدها و سولفاتها)
- تشکیل تری کلسیم سیلیکات بر اثر واکنش CaO اضافی با دی کلسیم سیلیکات
فرآیندهای بالا را میتوان بر اساس تغییر دمای درون کوره به چهار بخش تقسیم کرد:
- دمای 100 درجه سانتیگراد: بخار آب آزاد
- دمای 100 تا 430 درجه سانتیگراد: کاهش آب و تشکیل اکسیدهای سیلیسیوم، آلومینیوم و آهن
- دمای 900 تا 982 درجه سانتیگراد: آزاد شدن CO2 و تشکیل CaO بر اثر کلسیناسیون
- دمای 1510 درجه سانتیگراد: تشکیل کلینکر
واکنشهای شیمیایی بین مواد موجود در کوره بعد از بخار آب شروع میشوند. این واکنشها به ترتیب عبارت هستند از:
- تجزیه رس
- تجزیه دولومیت
- تجزیه کلسیت در دمای پایین
- واکنش آلومینا و اکسیژن
- واکنش کلسیت باقی مانده
- «سینترینگ» (Sintering) یا تف جوشی
کوره پخت سیمان، سه درجه نسبت به سطح افق زاویه دارد. این زاویه امکان عبور مواد خام از درون کوره را در مدت 20 تا 30 دقیقه فراهم میکند. با رسیدن مواد خام به پایینترین بخش، دانههای کلینکر با شکلی مشابه قلوه سنگ از درون کوره خارج میشوند.
مرحله پنجم: خنک سازی و آسیاب نهایی
با خروج کلینکر از درون کوره و تماس با هوای آزاد، دمای آن به سرعت از 2000 درجه سانتیگراد به 100 تا 200 درجه سانتیگراد میرسد. در این مرحله با آسیاب کردن مجدد کلینکر، چندین ماده مختلف به ترکیب اضافه میشود تا محصول نهایی (سیمان) به دست آید. سنگ گچ به منظور تعدیل زمان گیرش و مقاوم سازی به کلینکر اضافه و به همراه آن آسیاب میشود. به علاوه، این ماده از چسبیدن ترکیب به بدنه و گلولههای آسیاب جلوگیری میکند. مواد دیگری نظیر تری اتانول آمین نیز به منظور ریز شدن بهتر مواد و جلوگیری از گوله شدن آنها مورد استفاده قرار میگیرند.
به منظور صرفه جویی در مصرف انرژی، حرارت ایجاد شده توسط کلینکر به کوره بازمیگردد. آخرین مرحله از تولید سیمان، فرآیند آسیاب کردن نهایی است. در کارخانه سیمان، طبلکهای گردانی به همراه گلولههای فولادی وجود دارند. پس از فرآیند خنک شدن، کلینکر به درون این طبلکها منتقل میشود. با اتمام آسیاب نهایی، پودر ریزی به دست میآید که هر کیلوگرم از آن شامل 75 میلیون ذره است. این پودر، سیمان نام دارد.
مرحله ششم: بسته بندی و انتقال به انبار
در این مرحله، سیمان در بستههای 20 تا 40 کیلوگرمی بستهبندی شده و از محل آسیاب به سیلوهای مخصوص انتقال داده میشود. البته اکثر سیمان تولید شده در مقادیر بالا توسط کامیون، قطار یا کشتی به محلهای مورد نیاز انتقال مییابند و فقط مقدار کمی از آن به صورت بستهبندی شده به مشتریان تحویل داده میشود.
کاربردهای سیمان چه هستند؟
سیمان، ماده بسیار پرکابردی است. ویژگیهای منحصر به فرد این ماده باعث اهیمت بسیار بالای آن در حوزه مهندسی عمران شده است.
از کاربردهای اصلی سیمان، میتوان به موارد زیر اشاره کرد:
- ساخت ملات برای گچ کاری، بنایی، بندکشی و غیره
- استفاده به عنوان درزگیر اتصالات زهکشها و لولهها
- مقاومسازی سازه در برابر آب
- به کارگیری در بتن برای ساخت کف، سقف، نعل درگاه، تیر، پله، ستون و غیره
- ساخت سطوح سخت به منظور جلوگیری از آثار مخرب شیمیایی و دمایی
- ساخت لولههای پیش ساخته پایهها و تیر حصار
- ساخت سازههای مهندسی نظیر پل، آبگذر، سد، تونل، فانوس دریایی و غیره
- اجرای فونداسیون، کف آببند، گذرگاه و غیره
- ساخت چاه، مخزن آب، زمین بازی، تیر چراغ برق، جاده و غیره
خواص سیمان به چند دسته تقسیم می شوند؟
خواص سیمان، به دو گروه اصلی خواص فیزیکی و خواص شیمیایی تقسیم میشوند. در این بخش، به معرفی هر یک از این موارد میپردازیم.
خواص فیزیکی سیمان چه هستند؟
انواع مختلفی از سیمان در ساخت سازهها مورد استفاده قرار میگیرند. وجه تمایز این سیمانها، خواص فیزیکی آنها است. برخی از پارامترهای کلیدی باعث کنترل کیفیت سیمانهای مختلف میشوند. خواص فیزیکی سیمانهای مناسب عبارت هستند از:
- نرمی
- سلامت
- روانی
- استحکام
- حرارت هیدراتاسیون
- افت حرارتی
- چگالی توده ای
- وزن مخصوص (چگالی نسبی)
در ادامه، به معرفی این خواص و آزمایشهای موجود برای تعیین آنها میپردازیم.
نرمی سیمان چیست؟
اندازه ذرات سیمان، با عنوان نرمی آن شناخته میشود. نرمی مورد نیاز برای ساخت سیمانهای با کیفیت از طریق سایش خوب کلینکر در مرحله آخر تولید به دست میآید. نرخ هیدراتاسیون به طور مستقیم به اندازه ذرات بستگی دارد. به همین دلیل، نرمی یکی از خواص بسیار مهم در سیمانهای مختلف محسوب میشود.
سلامت سیمان چیست و چگونه اندازه گیری می شود؟
سلامتی سیمان، توانایی آن در عدم جمع شدگی هنگام سفت شدن است. حجم سیمانهای باکیفیت پس از گیرش تغییری نمیکند. وجود مقدار زیادی از آهک و مگنزیای آزاد در ترکیب، باعث افزایش حجم در گذر زمان میشود. عدم سلامت سیمان، مسئلهای است که پس از چندین سال مشخص میشود. برای اطمینان از سلامت سیمان میتوان آزمایشهایی نظیر آزمایش لوشاتلیه یا آزمایش اتوکلاو را بر روی آن انجام داد.
آزمایش لوشاتلیه چگونه انجام می شود؟
در «آزمایش لوشاتلیه» (Le Chatelier Test)، از تجهیزات مخصوص برای تعیین سلامت سیمان با توجه به میزان آهک به کار رفته در آن استفاده میشود. به این منظور، خمیر سیمانی با اسلامپ معمولی بین دو مقطع شیشهای و به مدت 24 ساعت در دمای 20 تا 21 درجه سانتیگراد زیر آب قرار داده میشود. در مرحله بعد، پس از اندازهگیری فاصله بین مقاطع، نمونه را دوباره به زیر آب برمیگردانند. سپس، با اعمال حرارت به آب، در مدت 25 تا 30 دقیقه آن را به نقطه جوش میرسانند. آب باید به مدت یک ساعت در نقطه جوش باقی بماند. در مرحله بعد، منتظر میمانند تا دستگاه سرد شود. سپس، فاصله بین مقاطع را دوباره اندازهگیری میکنند. در سیمانهای باکیفیت، فاصله بین مقاطع از 10 میلیمتر عبور نمیکند.
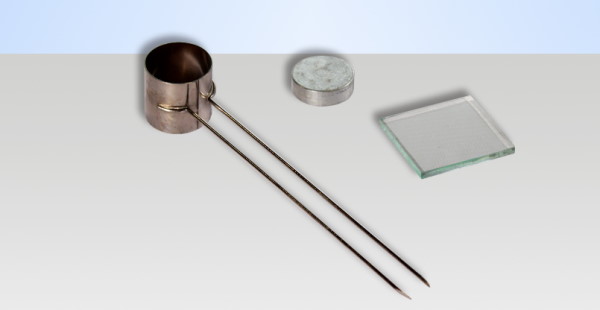
آزمایش اتوکلاو چگونه انجام می شود؟
در «آزمایش اتوکلاو» (Autoclave Test)، خمیر سیمانی با اسلامپ معمولی درون یک اتوکلاو (دستگاهی برای استریل کردن قطعات با دما و فشار بالا) قرار میگیرد. فشار اتوکلاو به آرامی تا مقدار 2.03 مگاپاسکال افزایش داده میشود. سپس، فشار به مدت سه ساعت در همین سطح باقی میماند. پس از بازگرداندن دما و فشار اتوکلاو به شرایط عادی محیط، تغییر طول نمونه اندازهگیری شده و به درصد بیان میشود. میزان تغییر اندازه سیمانهای باکیفیت، حداکثر 0.8 درصد است.
روانی سیمان چیست و چگونه اندازه گیری می شود؟
به میزان جریانپذیری سیمان، روانی آن گفته میشود. این خاصیت فیزیکی معمولا توسط «آزمایش ویکات» (Vicat Test) اندازهگیری میشود.
آزمایش ویکات چگونه انجام می شود؟
آزمایش ویکات، با عناوین دیگری نظیر آزمایش سوزن ویکات، آزمایش نقطه نرمشدگی ویکات و آزمایش سختی ویکات نیز شناخته میشود. در این آزمایش، ابتدا نمونهای از خمیر سیمانی با اسلامپ معمولی را در تجهیزات ویکات قرار میدهند. سپس، پیستون دستگاه را پایین میآورند تا نوک سوزن دستگاه به سطح بالایی سیمان برخورد کند. در مرحله بعد، سوزن با توجه به روانی سیمان، به میزان مشخصی درون آن فرو میرود. اگر عمق فرو رفتن سوزن بین 10 تا 11 میلی متر باشد، کیفیت روانی سیمان تایید میشود.
انواع استحکام سیمان کدام هستند و چگونه اندازه گیری می شوند؟
در ملات سیمانی، سه نوع استحکام فشاری، کششی و خمشی مورد بررسی قرار میگیرند. عوامل مختلفی بر روی میزان استحکام تاثیر دارند. از این عوامل میتوان به نسبت آب به سیمان (W/O)، نسبت سیمان به سنگدانههای ریز، شرایط عمل آوری، اندازه و شکل نمونه، نحوه اختلاط مواد، نحوه بارگذاری و سن اشاره کرد. در هنگام انجام آزمایشهای استحکام، توجه به نکات زیر ضروری است:
- استحکام ملات سیمانی و استحکام بتن ارتباط مستقیمی با هم ندارند. استحکام ملات سیمانی فقط به منظور کنترل کیفیت محصول مورد اندازهگیری قرار میگیرد.
- آزمایشهای استحکام بر روی ملات سیمانی انجام میشوند (نه بر روی خمیر سیمانی).
- استحکام ملات سیمانی با گذشت زمان افزایش مییابد. به همین دلیل، در کنار نتایج آزمایشها باید به سن ملات نیز اشاره کرد.
استحکام فشاری ملات سیمان چگونه اندازه گیری می شود؟
آزمایش استحکام یا مقاومت فشاری سیمان، متداولترین آزمایش برای کنترل کیفیت این ماده است. در این آزمایش، معمولا نمونهای با قطر 50 میلیمتر تا لحظه شکست در معرض بار فشاری قرار میگیرد. بازه افزایش بار در آزمایش مقاومت فشاری بین 20 تا 80 ثانیه است. مراحل انجام انواع مختلف این آزمایش، در استانداردهای ASTM-C-109 و ASTM-C-349 آورده شدهاند.
آیا اندازه گیری استحکام کششی ملات سیمان ضروری است؟
در سالهای اولیه اختراع سیمان، آزمایش استحکام یا مقاومت کششی بر روی ملات سیمانی انجام میگرفت. با این وجود، این آزمایش به دلیل اهمیت پایین و عدم ارائه اطلاعات مورد نیاز بیشتر راجع به ملات، منسوخ شد.
استحکام خمشی ملات سیمان چگونه اندازه گیری می شود؟
آزمایش استحکام یا مقاومت خمشی ملات سیمان، در واقع همان اندازهگیری مقاومت کششی در بارگذاری خمشی است. در این آزمایش، بارگذاری تا لحظه شکست بر روی مرکز نمونهای با ابعاد 160*40*40 میلیمتر (تیر متشکل از ملات سیمانی) انجام میشود. استاندارد ASTM-C-348 به نحوه اجرای آزمایش خمشی ملات سیمانهای هیدرولیکی اختصاص دارد.
زمان گیرش سیمان چیست، چه انواعی دارد و استانداردهای اندازه گیری آن کدام هستند؟
با افزودن آب به ترکیب سیمان، گیرش و سفت شدن آن شروع میشود. زمان گیرش، معیاری برای ارزیابی نرخ هیدراتاسیون است. این زمان به عوامل متعددی نظیر نرمی، W/O، مواد شیمیایی موجود و افزودنیها بستگی دارد. زمان گیرش اولیه سیمانهای مورد استفاده در ساخت و ساز نباید بیش از حد پایین و زمان گیرش نهایی نیز نباید بیش از حد بالا باشد. به این ترتیب، برای ارزیابی مدت گیرش سیمانهای مختلف باید دو زمان را اندازهگیری کرد:
- گیرش اولیه: زمانی که خمیر سیمانی به طور قابل ملاحظه شروع به سفت شدن میکند. این اتفاق معمولا در مدت 30 تا 45 دقیقه پس از افزودن آب رخ میدهد.
- گیرش نهایی: زمانی که ملات سیمانی سفت میشود و قابلیت تحمل بارگذاری را دارد. این اتفاق معمولا در زمانی کمتر از 10 ساعت رخ میدهد.
از استانداردهای موجود برای ارزیابی زمان گیرش سیمان، میتوان به موارد زیر اشاره کرد:
- استانداردهای AASHTO-T-131 و ASTM-C-191: تعیین زمان گیرش سیمانهای هیدرولیکی به وسیله سوزن ویکات
- استاندارد AASHTO-T-154: تعیین زمان گیرش سیمانهای هیدرولیکی به وسیله سوزن گیلرمو
- استاندارد ASTM-C-266: تعیین زمان گیرش خمیر سیمانهای هیدرولیکی به وسیله سوزن گیلرمو
حرارت هیدراتاسیون سیمان چیست و چگونه اندازه گیری می شود؟
پس از اضافه کردن آب به سیمان، واکنش شیمیایی هیدراتاسیون شروع میشود. این واکنش با افزایش دما همراه است. میزان حرارت ناشی از هیدراتاسیون بر روی کیفیت سیمان و همچنین کنترل دمای عمل آوری در آب و هوای هوای سرد تاثیر میگذارد. در صورت بالا بودن دمای هیدراتاسیون، احتمال رخ دادن تنشهای نامطلوب (مخصوصا در سازههای بزرگ) وجود خواهد داشت. حرارت هیدراتاسیون به میزان تری کلسیم سیلیکات (C3S)، تری کلسیم آلومینات (C3A)، نسبت W/O، نرمی و دمای عمل آوری نیز بستگی دارد. دمای هیدراتاسیون سیمانهای پرتلند با محاسبه اختلاف بین دمای 7 روزه و 28 روزه اندازهگیری میشود. روند این کار در استاندارد ASTM-C-186 توضیح داده شده است.
افت حرارتی سیمان چیست؟
اعمال حرارت 900 تا 1000 درجه سانتیگرادی به یک نمونه سیمانی باعث کاهش وزن نمونه میشود. به کاهش وزن ناشی از اعمال حرارت، افت حرارتی میگویند. نگهداری نامناسب و طولانی مدت یا استفاده از تجهیزات نامناسب در حین انتقال میتواند باعث شروع زودتر هیدراتاسیون و کربناتاسیون شود. این موارد از دلایل اصلی افت حرارتی هستند. اندازهگیری افت حرارتی توسط آنالیزهای شیمیایی و مطابق با استانداردهای AASHTO-T-105 و AASTM-C-114 صورت میگیرد.
چگالی توده ای سیمان چند است؟
هنگام مخلوط کردن آب با سیمان، آب جای هوا را میگیرد. به همین دلیل، چگالی توده ای سیمان، اهمیت زیادی در درک رفتار فیزیکی ملات سیمانی ندارد. چگالی توده ای سیمان، با توجه به درصد ترکیبات سازنده آن تغییر میکند. این چگالی معمولا بین 1000 تا 1250 کیلوگرم بر متر مکعب است. چگالی خمیر سیمانی، بر روی مقدار نهایی چگالی بتن اثر میگذارد.
وزن مخصوص سیمان چند است و چه کاربردی دارد؟
وزن مخصوص سیمان، معمولا در محاسبات مربوط به طرح اختلاط مورد استفاده قرار میگیرد. وزن مخصوص سیمانهای پرتلند برابر با 3.15 و وزن مخصوص سیمانهای دیگر (سرباره ای، پوزولانی و غیره) حدود 2.9 است.
خواص شیمیایی سیمان چه هستند؟
سنگ آهک (کلسیم)، ماسه یا رس (سیلیسیم)، بوکسیت (آلومینیوم)، کانی آهن، شیل، گچ، مارن، سرباره و اسلیت از مواد خام مورد استفاده برای ساخت سیمان هستند. آنالیز شیمیایی این مواد باعث آشنایی بهتر با خواص شیمیایی سیمانهای مختلف میشود. در بخش مربوط به اجزا تشکیل دهنده سیمان، به معرفی برخی از این خواص پرداختیم. در ادامه، خواص شیمیایی را با جزئیات بیشتری مورد بررسی قرار میدهیم.
تاثیر تری کلسیم آلومینات (C3A) بر روی خواص شیمیایی سیمان چیست؟
کم بودن مقدار C3A باعث مقاومت سیمان در برابر اثرات مخرب سولفات میشود. سنگ گچ، هیدارتاسیون C3A را کاهش داده و میزان حرارت آزاد شده در مراحل اولیه گیرش را افزایش میدهد. C3A تاثیر زیادی بر روی استحکام ندارد.
تاثیر تری کلسیم سیلیکات (C3S) بر روی خواص شیمیایی سیمان چیست؟
C3A باعث افزایش سرعت هیدراتاسیون و سفت شدن میشود. این ماده تاثیر بسزایی بر روی بهبود نرخ افزایش استحکام در طی مدت زمان گیرش اولیه دارد.
تاثیر دی کلسیم سیلیکات (C2S) بر روی خواص شیمیایی سیمان چیست؟
برخلاف تری کلسیم سیلیکات، C2A پس از یک هفته بر روی بهبود نرخ افزایش استحکام تاثیر میگذارد.
تاثیر فریت (C4AF) بر روی خواص شیمیایی سیمان چیست؟
فریت، یک نوع ماده کمک ذوب است. این ماده، دمای ذوب مواد خام موجود در کوره را از 3000 درجه فارنهایت (1650 درجه سانتیگراد) به 2000 درجه فارنهایت (1100 درجه سانتیگراد) میرساند. با وجود افزایش سرعت هیدارتاسیون به دلیل حضور فریت، استحکام تغییر زیادی نمیکند.
تاثیر مگنزیا (MgO) بر روی خواص شیمیایی سیمان چیست؟
در فرآیند ساخت سیمانهای پرتلند، از مگنزیا به عنوان یک ماده خام در مراحل ترکیب مواد خشک استفاده میشود. مصرف بیش از اندازه مگنزیا بر روی سلامت، افزایش حجم و استحکام مخلوط تاثیر منفی میگذارد. با این وجود، استفاده کم از آن میتواند استحکام را افزایش دهد. در صورت به کارگیری مگنزیا، میزان کربن دی اکسید (CO2) تولید شده نیز کاهش مییابد. حداکثر میزان MgO مورد استفاده در تمام سیمانها، 6 درصد است.
تاثیر سولفور تری اکسید (SO3) بر روی خواص شیمیایی سیمان چیست؟
مصرف بیش از اندازه SO3 باعث عدم سلامت سیمانها میشود.
تاثیر سولفور اکسید آهن یا اکسید فریک بر روی خواص شیمیایی سیمان چگونه است؟
اکسید آهن یا اکسید فریک، علاوه بر تقویت استحکام و سختی، تاثیر مستقیمی بر روی رنگ سیمانها دارد.
تاثیر نمک های قلیایی بر روی خواص شیمیایی سیمان چگونه است؟
اکسید پتاسیم (K2O) و اکسید سدیم (Na2O) موجود در سیمان، میزان نمکهای قلیایی یا آلکاین ترکیب را تعیین میکنند. سیمانهای دارای نمکهای قلیایی زیاد، در هنگام گیرش با مشکل مواجه میشوند. در صورت استفاده کم از آلکالین به همراه کلسیم کلراید، احتمال بیرنگ شدن ترکیب وجود دارد. افزودن نمکهای قلیایی به سیمان سربارهای، ویژگی هیدرولیکی مواد سربارهای را فعال میکند. حداکثر میزان آلکالین مورد استفاده در سیمانها 0.6 درصد است که طبق رابطه Na2O+0.658K2O محاسبه میشود.
تاثیر آهک آزاد بر روی خواص شیمیایی سیمان چگونه است؟
در برخی از مواقع، مقداری آهک آزاد درون سیمانهای مختلف وجود خواهد داشت. این ماده بر روی انبساط ترکیب تاثیر میگذارد.
تاثیر سیلیکا فوم بر روی خواص شیمیایی سیمان چگونه است؟
سیلیکا فوم، مادهای است که برای بهبود بسیاری از خواص سیمان نظیر مقاومت فشاری، مقاومت در برابر خوردگی و پیوند بین ذرات مورد استفاده قرار میگیرد. این ماده زمان گیرش را افزایش میدهد و با این وجود، تاثیر آن بر روی افزایش استحکام منحصر به فرد است. از اینرو، برای پروژهایی که نیازمند مقاومت بالا هستند، معمولا 5 تا 20 درصد سیلیکا فوم به ترکیب سیمان پرتلند اضافه میشود.
تاثیر آلومینا بر روی خواص شیمیایی سیمان چگونه است؟
آلومینا یک ماده مقاوم در برابر اثرات مخرب مواد شیمیایی نظیر خوردگی است. استفاده زیاد از این ماده درون سیمان، مقاومت در برابر هوای بسیار سرد را افزایش میدهد. آلومینا باعث سرعت بخشیدن به زمان گیرش میشود اما استحکام را تضعیف میکند.
ویژگی یک سیمان خوب چیست؟
هنگام اجرای یک پروژه، همیشه اولویت با استفاده از بهترین مصالح است. به همین دلیل، باید خواص سیمانهای مورد استفاده را بررسی و کیفیت آنها را کنترل کرد. در بخش قبلی، خواص فیزیکی و شیمیایی سیمان را به طور کامل مورد بررسی قرار دادیم. ویژگیهای یک سیمان خوب با توجه به نیازهای پروژه تغییر میکند. با این وجود، از خواص زیر میتوان به عنوان معیارهای کلی سیمانهای خوب نام برد:
- استحکام کافی برای بنایی
- سختی و سفت شدن سریع
- پلاستیسیته (روانی) مناسب
- کارایی آسان
- مقاومت خوب در برابر رطوبت
انواع سیمان کدام هستند؟
با گذشت زمان و پیشرفت تکنولوژی، کیفیت و انواع سیمانهای مورد استفاده در ساخت سازهها نیز گسترش یافت. امروزه، سیمانهای متنوعی در سازههای مختلف مورد استفاده قرار میگیرند.
انواع اصلی سیمان از نظر مکانیزم گیرش و سفت شدن به دو دسته زیر تقسیم میشوند:
- «سیمان هیدورلیکی» (Hydraulic Cement)
- «سیمان غیر هیدرولیکی» (Non-Hydraulic Cement)
بر اساس ترکیبات و خواص آنها نیز میتوان انواع سیمانهای پرکابرد در سازهها را به موارد زیر تقسیم کرد:
- «سیمان پرتلند معمولی» (Ordinary Portland Cement) یا OPC
- «سیمان پرتلند پوزولانی» (Portland Pozzolana Cement) یا PPC
- «سیمان سخت شونده» (Rapid Hardening Cement)
- «سیمان زودگیر» (Quick Setting Cement)
- «سیمان کم حرارت» (Low Heat Cement)
- «سیمان ضد سولفات» (Sulphate Resisting Cement)
- «سیمان سرباره ای» (Blast Furnace Cement)
- «سیمان آلومینا» (High Alumina Cement)
- «سیمان رنگی» (Colored Cement)
- «سیمان هوادار» (Air Entraining Cement)
- «سیمان انبساطی» (Expansive Cement)
- «سیمان ضد آب» (Hydrophobic Cement)
سیمان هیدرولیکی چیست؟
سیمانهای هیدرولیکی طی واکنش شیمیایی «هیدراتاسیون» (Hydration) یا آبپوشی سفت میشوند. سنگ آهک، رس و سنگ گچ، مواد اصلی سیمانهای غیر هیدرولیکی را تشکیل میدهند. با اعمال حرارت بالا به ترکیب این مواد، سیمانهای هیدرولیکی به دست میآیند. با وجود تاثیر مستقیم آب در گیرش سیمانهای هیدرولیکی، این مواد در برابر آب مقاوم هستند.
سیمان غیر هیدرولیکی چیست؟
سیمانهای غیر هیدرولیکی برای سفت شدن به آب نیاز ندارند. گیرش این نوع از سیمانها در شرایط خشک صورت میگیرد. سیمانهای غیر هیدرولیکی از موادی نظیر آهک، گچ و اکسید کلراید ساخته میشوند. آهک هیدراته (آهک مرده)، یکی از انواع سیمانهای غیر هیدرولیکی است.
تفاوت سیمان هیدرولیکی و سیمان غیر هیدرولیکی در چیست؟
همان طور که اشاره کردیم، سیمان بر اساس نحوه سفت شدن به دو نوع هیدرولیکی و غیر هیدرولیکی تقسیم میشود. سیمان هیدرولیکی، پس از اضافه کردن آب و طی واکنش شیمیایی هیدراتاسیون یا آبپوشی سفت میشود. در طرف مقابل، سفت شدن سیمان غیر هیدرولیکی طی واکنشی به نام «کربوناتسیون» (Carbonatation) یا کربناته شدن صورت میگیرد. برای درک بهتر تفاوت بین سیمان هیدرولیکی و سیمان غیرهیدرولیکی باید با ترکیب شیمیایی این دو آشنا شد.
مراحل شیمیایی سفت شدن سیمان غیر هیدرولیکی چه هستند؟
سیمان غیر هیدرولیکی طی مراحل زیر (چرخه آهک) سفت میشود:
- «کلسیناسیون» (Calcination) یا تکلیس: با اعمال حرارت بالای 825 درجه به سنگ آهک به مدت 10 ساعت، آهک زنده به دست میآید (CaCO3→CaO+CO2).
- «شکفتن» (Slaking): از ترکیب آب با اکسید کلسیم، آهک هیدراته تشکیل میشود (CaO+H2O→Ca(OH)2).
- «گیرش» (Setting): آب به طور کامل تبخیر میشود.
- سیمان در معرض هوای قرار میگیرد و پس از چندین واکنش شیمیایی زمانبر، سفت میشود (Ca(OH)2+CO2→CaCO3+H2O).
سیمان هیدرولیکی از چه موادی تشکیل میشود؟
در طرف مقابل، سیمان هیدرولیکی از سیلیکاتها و اکسیدها تشکیل میشود. چهار جز اصلی تشکیل دهنده سیمانهای هیدورلیکی عبارت هستند از:
- «بلیت» (Belite) با ترکیب شیمیایی 2CaO.SiO2
- «آلیت» (Alite) با ترکیب شیمیایی 3CaO.SiO2
- «سلیت» (Celite) یا تریکلسیم آلومینات با ترکیب شیمیایی 3CaO.Al2O3
- «براون میلریت» (Brownmillerite) با ترکیب شیمیایی 4CaO.AlO3.Fe2O3
خواص مکانیکی سیمانهای هیدرولیکی توسط سیلیکاتهای آن (بلیت و آلیت) کنترل میشود. به علاوه، رفتار این نوع سیمانها در فاز مایع (هنگام قرارگیری ترکیب در کوره) نیز به دو ماده دیگر (سلیت و براون میلریت) بستگی دارد. به منظور دستیابی به خواص ویژهای نظیر زمان گیرش بسیار پایین، جلوگیری از جمعشدگی، قابلیت استفاده در زیر آب و غیره میتوان از افزودنیهای شیمیایی یا معدنی در ترکیب سیمانها استفاده کرد.
سیمان پرتلند معمولی چیست و چه کاربردی دارد؟
سیمان پرتلند معمولی، کاربرد زیادی در ساخت و ساز دارد. کلینکر سیمانهای پرتلند، یک ماده هیدرولیک است که حداقل دو سوم از وزن آن را سیلیکات کلسیم تشکیل میدهد. باقی وزن این کلینکر از آلومینیوم، آهن و مواد دیگر تشکیل میشود. نسبت CaO به SiO2 در سیمانهای پرتلند معمولی نباید بیشتر از 2 باشد. به علاوه، مقدار اکسید منیزیم مورد استفاده نیز نباید از 5 درصد وزن کل عبور کند. ترکیب سیمان پرتلند معمولی عبارت است از:
- خاک رسی یا سیلیکات آلومینا (حاوی رس و شیل)
- خاک کربناته یا کربنات کلسیم (حاوی سنگ آهک، گچ و مارن)
از کاربردهای اصلی سیمانهای پرتلند معمولی میتوان به موارد زیر اشاره کرد:
- استفاده در ساخت و سازهای عادی
- کاربرد زیاد در بنایی
سیمان پرتلند پوزولانی چیست و چه کاربردی دارد؟
پوزولان، مادهای حاوی سیلیکا (سیلیسیم دی اکسید) در حالت واکنش پذیر است. این ماده هم به صورت طبیعی یافت شده و هم به صورت مصنوعی ساخته میشود. پوزولان با کلسیم هیدرواکسید تولید شده در سیمان در حال گیرش واکنش میدهد. محصول این واکنش، چند ماده سیمانی اضافی است. ترکیب سیمانپرتلند پوزولانی عبارت هستند از:
- کلینکر سیمان پرتلند معمولی
- سنگ گچ
- مواد پوزولانی (خاکستر بادی، خاکستر آتشفشانی و خاک رس تکلیس شده یا سیلیکا فوم)
از کاربردهای اصلی سیمان پرتلند پوزولانی میتوان به موارد زیر اشاره کرد:
- ساخت سازههای هیدرولیکی، دریایی، زیرآبی، سد و غیره
- ساخت عضوهای بتنی پیش تنیده و پس تنیده
- آثار هنری و تزئینی (به دلیل قابلیت پرداخت بهتر)
- ساخت لولههای فاضلاب پیش ساخته
سیمان زود سخت شونده چیست و چه کاربردی دارد؟
با بیشتر کردن مقدار سیلیکات تری کلسیم با دانهبندی بسیار ریز در سیمانهای پرتلند معمولی، نرخ بهبود مقاومت فشاری افزایش مییابد. این نوع از سیمانهای پرتلند معمولی با عنوان سیمان زود سخت شونده شناخته میشوند. زمان گیرش اولیه سیمانهای زود سخت شونده برابر با 30 دقیقه و زمان گیرش نهایی آنها برابر با 600 دقیقه است. از کاربردهای اصلی سیمانهای زود سخت شونده میتوان به موارد زیر اشاره کرد:
- ساخت سریع سازه به دلیل نبودن زمان کافی برای گیرش (مانند پیادهرو)
- ساخت سازههایی با مقاومت بالاتر از مقاومت بتن معمولی
سیمان زودگیر چیست و چه کاربردی دارد؟
سیمان زودگیر، زمان گیرش بسیار پایینی دارد. زمان گیرش اولیه در این نوع از سیمانها، 5 دقیقه و زمان گیرش نهایی آنها، حدود 30 دقیقه است. ترکیب سیمانهای زودگیر عبارت است از:
- کلینکر
- سولفات آلومینیوم (1 تا 3 درصد وزن کلینکر) برای افزایش نرخ هیدارتاسیون سیلیکات
کاربرد اصلی سیمانهای زودگیر در موارد زیر است:
- ساخت سازههای زیرآبی
- ساخت سازه در آب و هوای بارانی و سرد
- ساخت سازه در هوای گرم با سرعت تبخیر بالای آب
- استفاده به عنوان راک بولت (پیچ سنگ) در تونلسازی و معدنکاری
سیمان کم حرارت چیست و چه کاربردی دارد؟
سیمانهای کم حرارت در حین واکنش هیدراتاسیون، دمای کمی تولید میکنند. این ویژگی با تغییر خاصیت شیمیایی برخی از ترکیبات سیمانهای پرتلند معمولی به دست میآید. ترکیب شیمیایی سیمانهای کم حرارت عبارت است از:
- تریکلسیم آلومینات با درصد کم (حدود 5 درصد)
- دیکلسیم سیلیکات با درصد بالا (حدود 46 درصد)
از کاربردهای سیمانهای کم حرارت میتوان به موارد زیر اشاره کرد:
- ساخت پیهای بزرگ سد، دالهای بتنی بزرگ و پایه ستون توربینهای بادی
- ساخت کارخانههای شیمیایی
سیمان ضد سولفات چیست و چه کاربردی دارد؟
سیمان ضد سولفات، به منظور مقاومت در برابر عاملهای مخرب سولفاتی ساخته شده است. به دلیل درصد پایین تریکلسیم آلومینات به کار رفته در این سیمانها، میزان سولفو آلومینات کلسیم کاهش مییابد. کاربردهای اصلی سیمانهای ضد سولفات عبارت هستند از:
- ساخت سازههایی که با خاک یا آب دارای نمکهای سولفیدی در ارتباط هستند (وجود بیشتر از 0.2 درصد یا 0.3 درصد گرم بر لیتر).
- سازههایی که به طور مداوم خیس و خشک میشوند (پایه پل، سازههای موجود در نواحی جزر و مد و غیره).
- ساخت فاضلاب، شومینه، کارخانههای تولید مواد شیمیایی، منبع آب، آبگیر، برج خنک کننده و سازههای دیگری که احتمال تولید مواد شیمیایی در آنها وجود دارد.
سیمان سرباره ای چیست و چه کاربردی دارد؟
از ترکیب کلینکر سیمانهای پرتلند با سرباره کوره آهن گدازی، سیمان سرباره ای ساخته میشود. حداکثر 65 درصد از ترکیب این نوع از سیمانها را سرباره تشکیل میدهد. به کارگیری سیمانهای سرباره ای در موارد زیر مناسب است:
- ساخت سازههایی با مقاومت بالا در برابر سولفات
- ساخت سازههای نزدیک به آب
سیمان آلومینا چیست و چه کاربردی دارد؟
سیمان آلومینا از ترکیب بوکسیت کلسینه (یکی از کانیهای آلومینیوم) و آهک معمولی به همراه کلینکر در حین ساخت سیمان پرتلند معمولی به دست میآید. در این نوع سیمان، میزان آلومینیوم نباید کمتر از 32 درصد و نسبت وزنی آلومینیوم به آهک باید بین 0.85 تا 1.3 باشد.
از کاربردهای اصلی سیمانهای آلومینا میتوان به موارد زیر اشاره کرد:
- ساخت سازههایی که در معرض دمای بالا قرار دارند.
- ساخت سازههایی کع در معرض یخزدگی و واکنشهای اسیدی قرار دارند.
سیمان سفید چیست و چه کاربردی دارد؟
سیمان سفید، مشابه سیمانهای پرتلند معمولی اما به رنگ سفید است. در سیمانهای سفید، اکسیدهای آهن و منگنز کمتری مورد استفاده قرار میگیرد. به دلیل قیمت بالاتر این نوع از سیمانها نسبت به سیمانهای پرتلند معمولی، استفاده آنها در ساخت و سازهای معمولی به صرفه نخواهد بود. سیمانهای سفید در موارد زیر کاربرد دارند:
- ساخت آثار تزئینی
- ساخت حفاظهای جادهای، کاشیکاری، ساخت استخر و غیره
سیمان رنگی چیست و چه کاربردی دارد؟
به منظور ساخت سیمانهای رنگی، 5 تا 10 درصد از ترکیب سیمانهای پرتلند معمولی با رنگدانههای مناسب مخلوط میشود. نوع رنگدانههای به کار رفته در سیمانهای رنگی به نیاز اثر یا سازه در حال ساخت بستگی دارد. کاربرد اصلی این نوع سیمانها در ساخت آثار تزئینی متنوع است.
سیمان هوادار چیست و چه کاربردی دارد؟
تحقیقات نشان دادهاند که اضافه کردن هوا یا تشکیل حباب در هنگام به کارگیری سیمانها باعث افزایش مقاومت در برابر یخزدگی، آتش، پوسته پوسته شدن و آسیبهای مشابه دیگر میشود. سیمان هوادار، نوع مخصوصی از سیمانها است که حبابهای ریز هوا را درون خود محبوس میکند. هوادار کردن سیمان، با ترکیب مواد هوادار با کلینکر (افزودن مواد رزینی به سیمانهای پرتلند معمولی) صورت میگیرد.
یخ زدن آب درون بتن در دماهای پایین، باعث انبساط میشود. وجود حبابهای هوا، از ترک خوردن بتن در حین انبساط آب جلوگیری میکند. البته، این ویژگی تاثیری بر روی افزایش مقاومت بتن ندارد. از کاربردهای اصلی سیمانهای هوادار میتوان به موارد زیر اشاره کرد:
- ساخت سازههای مختلف در آب و هوای هوای بسیار سرد
- افزایش مقاومت در برابر اثرات مخرب سولفات
- استفاده در ترکیبات دارای مواد شیمیایی یخ زدا
سیمان انبساطی چیست و چه کاربردی دارد؟
حجم سیمانهای انبساطی در حین فرآیند هیدراتاسیون افزایش مییابد. این ویژگی به منظور جلوگیری از جمع شدگی مورد استفاده قرار میگیرد. کاربردهای اصلی سیمانهای انبساطی عبارت هستند از:
- ساخت سازههایی با عضوهای بتنی پیش تنیده
- درزگیری و پر کردن راک بولتهای دوغابی
- ساخت سازههای مختلف هیدرولیکی (سد، کانالهای انتقال آب و غیره)
سیمانهای انبساطی دارای سه نوع هستند:
- سیمان انبساطی نوع K
- سیمان انبساطی نوع M
- سیمان انبساطی نوع S
سیمان انبساطی نوع K از چه موادی تشکیل میشود؟
مواد تشکیل دهنده سیمانهای انبساطی نوع K عبارت هستند از:
- سیمان پرتلند
- سولفات تترا کلسیم تری آلومینات بدون آب (C4A3S)
- سولفات کلسیم (CaSO4)
- آهک (CaO)
سیمان انبساطی نوع M از چه موادی تشکیل میشود؟
ترکیبات اصلی سیمانهای انبساطی نوع M عبارت هستند از:
- کلینکرهای سیمان پرتلند
- سولفات کلسیم
سیمان انبساطی نوع S از چه موادی تشکیل میشود؟
سیمانهای انبساطی نوع S از مواد زیر تشکیل میشود:
- کلینکرهای سیمان پرتلند
- سولفات کلسیم (به مقدار زیاد)
- تری کلسیم آلومینات (به مقدار زیاد)
سیمان ضد آب چیست و چه کاربردی دارد؟
به منظور جلوگیری از شروع فرآیند هیدراتاسیون در هنگام عملیاتهای انتقال یا نگهداری، موادی با غشا دافع آب مانند اسید اولئیک یا اسید استئاریک به کلینکر اضافه میشوند. این مواد شیمیایی، لایهای را بر روی ذرات تشکیل میدهند که از ترکیب آب و شروع هیدراتاسیون جلوگیری میکند. هنگام مخلوط کردن سیمان و سنگدانه (شن و ماسه) در میکسر، لایه محافظ شکسته شده و فرآیند هیدراتاسیون شروع میشود. این فرآیند، مقداری حباب هوا را درون ترکیب اضافه میکند. به این ترتیب، کارایی نیز افزایش مییابد. از کاربردهای اصلی سیمانهای ضد آب میتوان به موارد زیر اشاره کرد:
- ساخت سازههای آب نظیر سد، سرریز و سازهای زیرآبی
- ساخت سازههای زیرزمینی نظیر تونلها
سلام ممنون از اطلاعات بسیار جامع. و خواندنی در باره سیمان مدت ها بود میخواستم بدونم که سیمان چگونه تهیه میشود و شما توضیح کامل را دادید ممنون از شما موفق و موید باشید
سلام ارادت
خیلی مطالب جامع و کاربردی بود ممنونم
سلام و عرض ادب
مقاله کاملی برای صنعت سیمان نوشته اید.
ممنونم
باسلام.
مطالب بسیار مفید و جامع بودند
لطفا منابع رو هم ذکر کنید
سپاسگزارم
سلام، وقت شما بخیر؛
منبع تمامی مطالب مجله فرادرس در انتهای آنها ذکر شده است.
از همراهی و بازخورد شما بسیار سپاسگزاریم.