دایکاست چیست؟ – دانستنی های مهم درباره ریخته گری تحت فشار
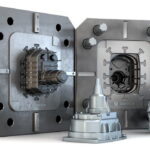
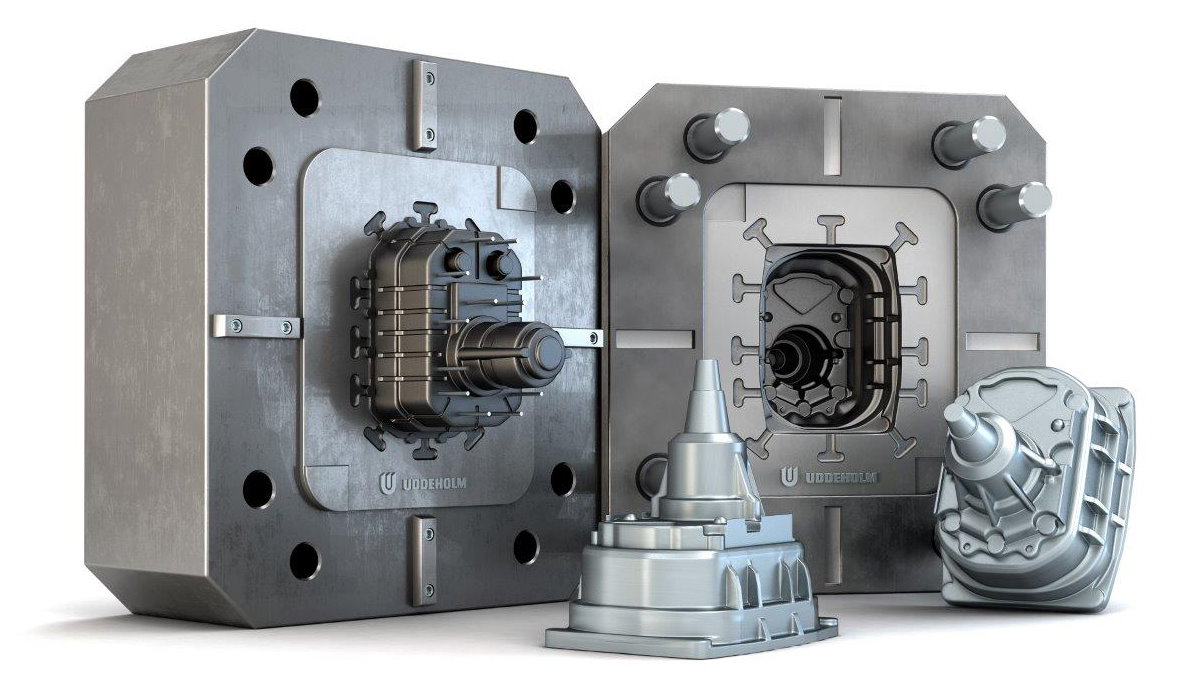
اگر به وسایل و تجهیزات اطراف خود دقت کنید، متوجه خواهید شد که بسیاری از این وسایل از کنار هم قرار گرفتن چندین قطعه تشکیل میشوند. برخی از این قطعات از جنس مواد پلاستیکی و برخی دیگر از جنس مواد فلزی هستند. اغلب قطعات تشکیل دهنده وسایل، ساختار سادهای دارند. این قطعات توسط اتصالات پیچی، جوشی و غیره به قطعات مجاور خود متصل میشوند. با این وجود، تعدادی از قطعات یا حتی وسایل از ساختار پیچیده اما یکپارچه برخوردار هستند. ممکن برایتان این سوال پیش بیاید که ساخت قطعات پیچیده و یکپارچه چگونه انجام میگیرد. دایکاست یا ریخته گری تحت فشار، یکی از پاسخهای احتمالی به این سوال است. در این مقاله، به معرفی تاریخچه، مراحل اجرا، انواع روشها، کاربردها، مزایا، معایب، عیوب، تجهیزات و اصول طراحی قالب های دایکاست میپردازیم.
انواع روش های ریخته گری کدام هستند؟
از پرکاربردترین روشهای ریخته گری و ساخت قطعات فلزی میتوان به روش دایکاست (ریخته گری تحت فشار)، ریخته گری ثقلی در قالب ریژه، ریخته گری ماسه ای و ریخته گری دقیق اشاره کرد.
البته امکان اجرای فرآیند ریخته گری به روشهای دیگری نظیر ریخته گری کم فشار، ریخته گری گریز از مرکز، ریخته گری تحت خلا، ریخته گری کوبشی، ریخته گری لاست فوم و ریخته گری پیوسته نیز وجود دارد.
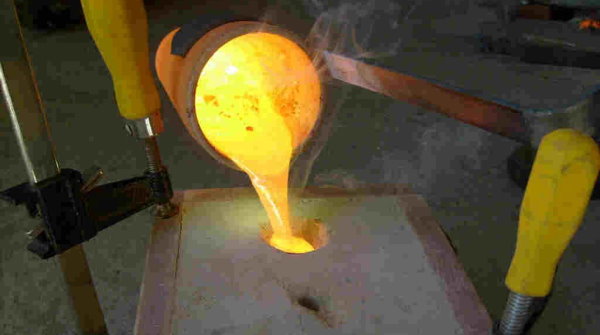
دایکاست یا ریخته گری تحت فشار چیست ؟
ریخته گری تحت فشار یا اصطلاحا دایکاست، از پرکاربردترین روشهای تولید انبوه قطعات فلزی پیچیده در صنایع مختلف است. تولید قطعات فلزی (فلزکاری) به روش دایکاست، از اصول کلی ریخته گری پیروی میکند.
این روش طی فرآیند ذوب، ریختن مواد مذاب به درون قالب (تزریق) و تغییر فاز مواد از مایع به جامد (انجماد) انجام میگیرد. ریخته گری تحت فشار در تولید قطعات ساده تا پیچیده در صنایع مختلف نظیر خودروسازی، هوافضا، ساخت ماشینآلات صنعتی، جواهرسازی، مجسمهسازی و غیره کاربرد دارد.
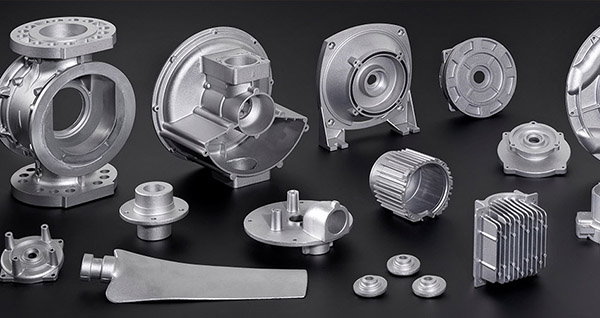
تاریخچه دایکاست
در اواسط قرن 19 میلادی (اوایل قرن 13 شمسی)، قابلیتهای صنعت چاپ با پیشرفت و توسعه زیادی همراه شد. اختراع تجهیزات ریخته گری تحت فشار، یکی از عوامل موثر بر رشد این صنعت بود. در آن دوران، ماشینهای تحریر از قطعات زیادی برای تایپ حروف، علائم نگارشی و اعداد تشکیل میشدند. فرآیند دایکاست، سرعت ساخت این قطعات و کیفیت آنها (از نظر یکنواختی ابعاد) را به میزان قابل توجهی افزایش داد. این فرآیند پیشرفته، کاهش تعداد خطاهای تولید و افزایش سرعت سرهم کردن قطعات را در پی داشت. کاربرد موفقیت آمیز ریخته گری تحت فشار در صنعت چاپ، باعث جلب توجه صنایع دیگر به این روش نوین ساخت و تولید شد.
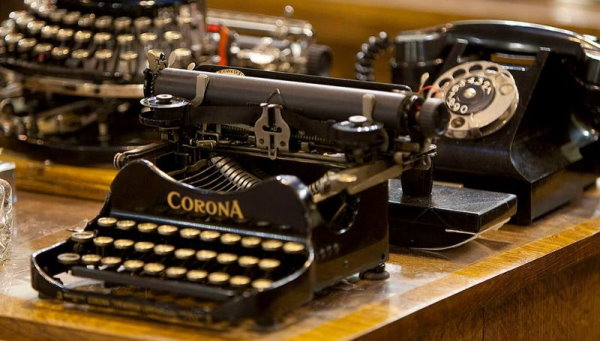
اولین تجهیزات مورد استفاده برای اجرای ریخته گری تحت فشار، دستگاه کوچکی بود که به صورت دستی کار میکرد. این دستگاه در سال 1838 میلادی (1217 شمسی) اختراع شد. فرآیند ریخته گری توسط این دستگاه، با ذوب کردن ترکیبی از قلع و سرب و ریختن آلیاژ مذاب به درون یک قالب فولادی انجام میگرفت. قالب مورد استفاده در این فرآیند با عنوان «دای» (Die) شناخته میشد. پس از سرد شدن و انجماد آلیاژ، قطعهای به شکل حفره قالب به دست میآمد. به قطعه حاصل از این فرآیند، «کَستینگ» (Casting) میگفتند. به همین دلیل، فرآیند ریخته گری تحت فشار با عنوان «دای کستینگ» (Die Casting) شناخته میشود. البته برای اشاره به این فرآیند، کارشناسان و صنعتگران فارسی زبان از اصطلاح دایکاست استفاده میکنند.
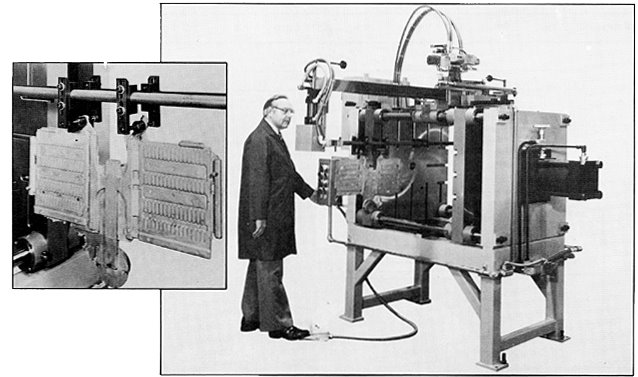
ریخته گری به روش دایکاست به مدت 30 سال فقط در صنعت چاپ مورد استفاده قرار گرفت. تا اینکه در اوایل دهه 1890 میلادی (اوایل دهه 1270 شمسی)، صنایع کوچک و بزرگ دیگر نیز به استفاده از این روش ساخت و تولید روی آوردند. به طوری که قطعات ماشین آلات صنعتی نیز به روش دایکاست تهیه میشدند. در سال 1914 میلادی (1293 شمسی)، آلیاژ آلومینیوم و روی برای ساخت قطعات مقاومتر مورد استفاده قرار گرفت. چندین سال بعد، آلیاژهای مس و منیزیم نیز به فهرست مواد قابل استفاده در ریخته گری تحت فشار اضافه شدند. امروزه، دستگاههای دایکاست میتوانند قطعات متنوعی را از نظر شکل و خواص مکانیکی تولید کنند.
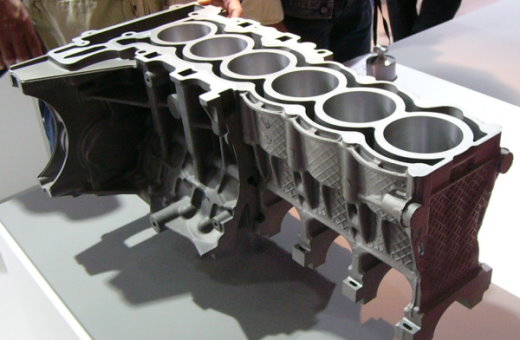
در سالهای اولیه معرفی ریخته گری دایکاست، اجرای این فرآیند با محدودیت فشار قابل اعمال به مواد مذاب همراه بود. در واقع، سیستم تزریق مواد مذاب در فشار پایین انجام میگرفت. پیشرفت ماشینآلات و افزایش مقاومت آنها در برابر فشار و دما، زمینه توسعه روش دایکاست و اجرای تزریق تحت فشار بالا را فراهم کرد. امروزه، ریخته گری با فشار بالا به عنوان یک روش استاندارد و با کیفیت شناخته میشود.
کاربرد دایکاست چیست ؟
ریخته گری تحت فشار یکی از کارآمدترین روشهای ساخت قطعات با شکلهای پیچیده، ساختار یکپارچه، ابعاد دقیق، سطح با کیفیت، مقاومت بالا و سختی مناسب است. به همین دلیل، این روش کاربرد گسترده در تولید قطعات تجهیزات صنعتی و کالاهای مصرفی، مخصوصا قطعات اتومبیل دارد. به طور کلی، حدود 60 درصد از قطعات ساخته شده به روش ریخته گری دایکاست در صنعت اتومبیلسازی مورد استفاده قرار میگیرند. این روش در صنایع هوافضا، تجهیزات الکترونیکی، ساخت لوازم خانگی و جواهرسازی نیز کاربرد دارد.
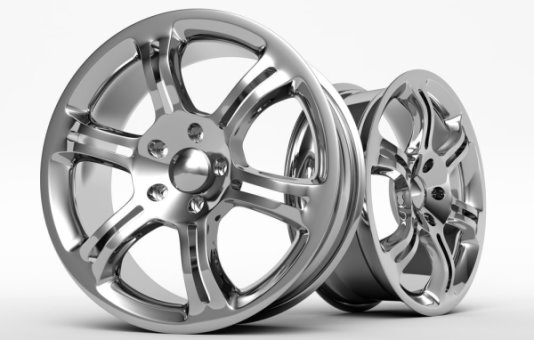
چرخ دایکاست، چراغ دایکاست (چراغهای شهری، لوستر دایکاست)، ظروف دایکاست (مانند قابلمه دایکاست)، رادیاتور دایکاست و بسیاری از قطعات صنعتی و غیر صنعتی فلزی از مواردی هستند که توسط روش ریخته گری تحت فشار ساخته میشوند.
مراحل اجرای ریخته گری دایکاست چه هستند؟
ریخته گری به روش دایکاست طی پنج مرحله اصلی آمادهسازی قالب، تزریق مواد مذاب، خنککاری، باز کردن قالب و برشکاری انجام میگیرد.
تصویر متحرک زیر، فرآیند «تزریق» (Injection)، «انجماد» (Solidification) و «خروج» (Ejection) را نمایش میدهد.
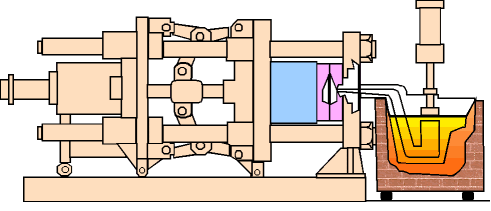
آمادهسازی قالب ریخته گری تحت فشار
اولین مرحله در ساخت قطعه به روش ریخته گری تحت فشار، آمادهسازی قطعات قالب دایکاست است. این قالب، از دو بخش ثابت و متحرک تشکیل میشود. بخش ثابت قالب بر روی صفحه ثابت دستگاه دایکاست و بخش متحرک آن بر روی صفحه متحرک دستگاه قرار میگیرد. از فعالیتهای اصلی در آمادهسازی قالب ریخته گری تحت فشار میتوان به موارد زیر اشاره کرد:
- تمیزکاری: برداشتن مواد باقیمانده بر روی هر بخش از قالب و پاک کردن سطح قطعات پس از هر چرخه ریخته گری به منظور جلوگیری از کاهش کیفیت سطح قطعه
- روانکاری: اعمال مواد روانکننده نظیر گریس یا روغن به قطعات پس از هر دو یا سه چرخه ریخته گری (با توجه به جنس قالب) به منظور سهولت باز و بسته کردن قالب
- بستن قالب: اتصال بخش ثابت و متحرک، محکم کردن آنها و اعمال نیروی مناسب به قالب برای ثابت نگه داشت آن در حین تزریق مواد مذاب
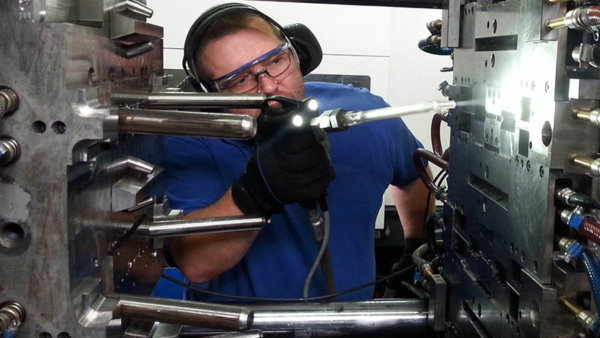
فرآیند آمادهسازی قالب به ابعاد قطعات بستگی دارد. هر چه ابعاد قالب و دستگاه بزرگتر باشد، میزان و زمان مورد نیاز برای تمیزکاری و روانکاری افزایش مییابد. به علاوه، در دستگاههای بزرگ، باز و بسته کردن قالب زمان بیشتر میبرد.
تزریق مواد مذاب به درون قالب
در مرحله بعدی، فلز مذاب از درون کوره به محفظه دستگاه منتقل میشود. نحوه انتقال مواد مذاب، به نوع دستگاه دایکاست (محفظه سرد یا محفظه گرم) بستگی دارد. پس از انجام فرآیند انتقال، تزریق فلز مذاب به درون قالب تحت فشار بالا انجام میگیرد. فشار تزریق در روش دایکاست معمولا بین 70 تا 1400 بار است. این فشار، نیروی مورد نیاز برای ثابت نگه داشتن مواد مذاب حین فرآیند انجماد (تغییر فاز مایع به جامد) را فراهم میکند.
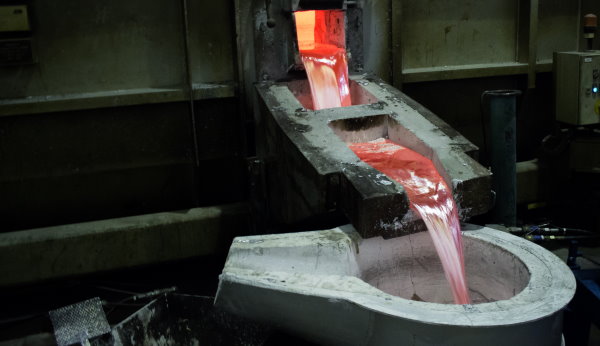
به میزان مواد مذاب تزریق شده به درون قالب، شات میگویند. زمان مورد نیاز برای پر کردن تمام حفرهها و مجراهای قالب نیز با عنوان زمان تزریق شناخته میشود. این زمان بسیار محدود بوده و معمولا کمتر از 0.1 ثانیه است. محدود بودن زمان تزریق، از انجماد غیر یکنواخت بخشهای مختلف جلوگیری میکند. زمان تزریق از پارامترهایی است که در طراحی فرآیند ریخته گری تحت فشار مورد بررسی قرار میگیرد.
طراحی زمان تزریق در دایکاست بر اساس خواص ترمودینامیکی مواد و ضخامت دیواره انجام میگیرد. هر چه ضخامت دیواره بیشتر باشد، زمان مورد نیاز برای تزریق افزایش مییابد. در صورت استفاده از دستگاه محفظه سرد، زمان ریختن دستی مواد مذاب از پاتیل به درون محفظه شات، باید به عنوان یکی از پارامترهای طراحی زمان تزریق در نظر گرفته شود.
خنک کاری
با ورود مواد مذاب به درون حفرههای قالب، این مواد شروع به خنک شدن میکنند و از حالت مایع به جامد تغییر فاز میدهند. کاهش دمای قالب و مواد داخل آن توسط سیستم خنک کننده انجام میگیرد. پس از پر شدن تمام حفرهها و انجماد مواد مذاب، قطعهای با شکل دلخواه تشکیل میشود. امکان باز کردن قالب، پیش از اتمام زمان سرد شدن و انجماد کامل قطعه وجود ندارد. این زمان با توجه به خواص ترمودینامیکی، حداکثر ضخامت دیواره و پیچیدگی قالب تعیین میشود. هرچه ضخامت دیواره قطعه و پیچیدگی هندسی آن بیشتر باشد، زمان مورد نیاز برای خنک شدن کامل نیز بیشتر خواهد بود.
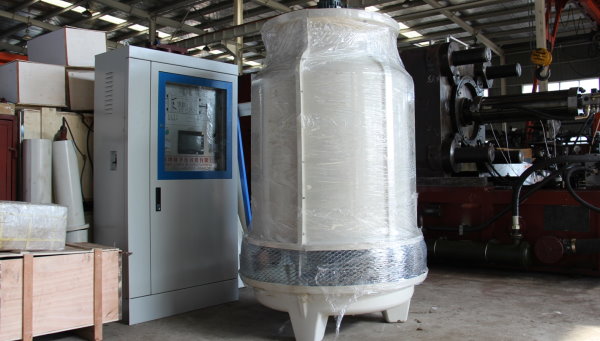
باز کردن قالب و خروج قطعه
پس از گذشت زمان خنک شدن قطعه، امکان باز کردن بخش متحرک قالب و خارج کردن قطعه به کمک مکانیزم خروج یا اصطلاحا سیستم پران فراهم میشود. زمان باز کردن قالب، تابعی از قابلیتهای فنی دستگاه و زمان خروج کامل، تابعی از ابعاد بخش دربرگیرنده قطعه و زمان افتادن آن است. به دلیل انقباض ناشی از جمعشدگی قطعه در فرآیند انجماد و چسبیدن مواد به دیواره قالب، فرآیند خروج با اعمال نیرو توسط پینهای مخصوص انجام میگیرد. پس از خارج شدن قطعه، امکان بستن مجدد قالب و تکرار فرآیند تزریق فراهم میشود.
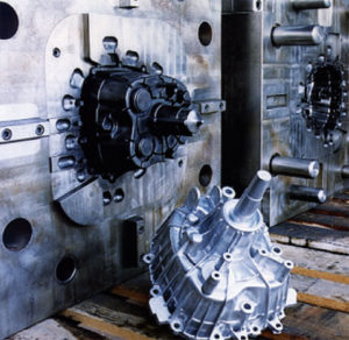
برشکاری قطعه
تزریق مواد مذاب به درون حفرهها، از طریق مجراهای قالب انجام میگیرد. به دلیل باقی ماندن مواد مذاب در این مجراها طی فرآیند خنک شدن، زائدههایی بر روی قطعه ایجاد میشوند. مرحله آخر از ساخت قطعه به روش ریخته گری دایکاست، باید زائدههای سطحی را توسط روشهای دستی یا مکانیکی از بین برد. زمان مورد نیاز برای حذف مواد اضافی به ابعاد قطعه بستگی دارد. مواد جدا شده در این فرآیند به بخش ضایعات یا بازیافت (برای استفاده مجدد) منتقل میشوند.
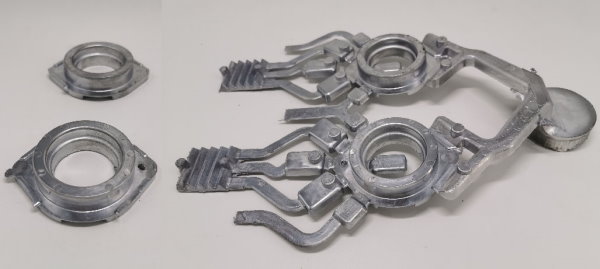
انواع دستگاه دایکاست کدام هستند؟
اجرای فرآیندهای ریخته گری تحت فشار با استفاده از دستگاههای مخصوص انجام میگیرد. به طور کلی، دستگاههای دایکاست به دو نوع دستگاه دایکاست با سیستم تزریق محفظه گرم و دستگاه دایکاست با سیستم تزریق محفظه سرد تقسیم میشوند.
دستگاه دایکاست با سیستم تزریق محفظه گرم
«دستگاه دایکاست با محفظه گرم» (Hot Chamber Die Casting Machine)، از تجهیزات مخصوص ریخته گری تحت فشار است که به منظور ساخت قطعاتی از جنس روی، قلع و سرب (آلیاژهای دارای نقطه ذوب پایین) مورد استفاده قرار میگیرد. تصویر زیر، اجزای مختلف این دستگاه را در وضعیت باز نمایش میدهد.
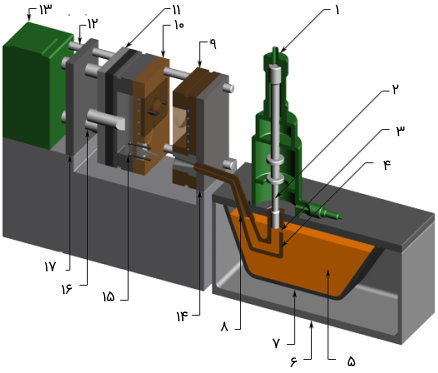
مطابق با تصویر بالا، اجزای دستگاه ریخته گری تحت فشار با محفظه گرم عبارت هستند از:
- سیلندر هیدرولیکی
- پلانجر
- مجرای ورودی
- محفظه شات تزریق
- فلز مذاب
- کوره
- دیگ
- مجرای گردن غازی یا «گوس نک» (Gooseneck)
- بخش ثابت قالب
- بخش متحرک قالب
- صفحه متحرک
- میله افقی نگهدارنده
- واحد باز و بسته کردن قالب یا «کلمپینگ» (Clamping)
- صفحه ثابت
- سیستم پران (جدا کننده قطعه از قالب)
- میله سیستم کلمپینگ
- صفحه پشتی
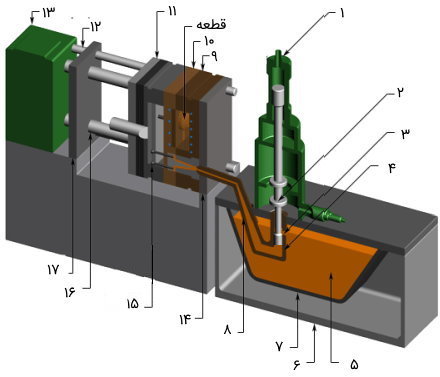
همانطور که مشاهده میکنید، سیستم تزریق محفظه گرم از سیلندر و پلانجر برای تزریق مواد مذاب به درون قالب استفاده میکند. به دلیل تماس مستقیم این تجهیزات با مواد مذاب، بالا رفتن دمای ذوب میتواند باعث آسیب رسیدن به دستگاه شود. فلز مذاب درون دیگ و کوره قرار میگیرد. افزایش دمای کوره، فلز را از حالت جامد به حالت مایع (مذاب) تغییر میدهد. سپس، ماده مذاب از درون مجرای ورودی به محفظه شات تزریق انتقال مییابد. پیش از شروع تزریق، قالب بسته و اصطلاحا جفت میشود.
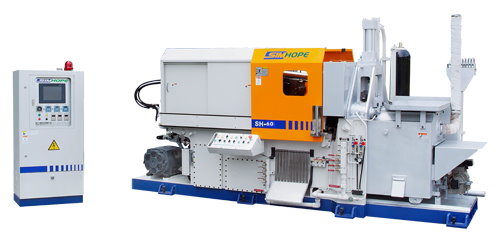
پایین آمدن پلانجر به کمک انرژی هیدرولیکی (پمپ)، فشار مورد نیاز برای تزریق فلز مذاب از درون مجرای گردن غازی به داخل حفره قالب را فراهم میکند. فشار تزریق در این روش معمولا بین 69 تا 345 بار است. پس از تزریق کامل مواد مذاب، پلانجر در وضعیت پایین باقی میماند تا تغییری در فشار سیستم رخ ندهد. با اتمام فرآیند انجماد، پلانجر به سمت بالا جابجا میشود. سپس، بخش متحرک قالب به سمت عقب حرکت کرده و میلههای سیستم پران، با وارد کردن فشار به پشت قطعه، آن را از درون قالب متحرک به بیرون هدایت میکنند. تصویر متحرک زیر، روند کلی ساخت قطعه با استفاده از دستگاه دایکاست محفظه گرم را نمایش میدهد.
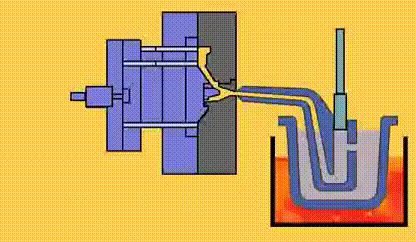
دستگاه دایکاست با سیستم تزریق محفظه سرد
«دستگاه دایکاست با محفظه سرد» (Cold Chamber Die Casting Machine)، یکی دیگر از تجهیزات ریخته گری تحت فشار است که به منظور ساخت قطعاتی از جنس آلومینیوم، برنج و منیزیوم (مواد دارای نقطه ذوب نسبتا بالا) مورد استفاده قرار میگیرد. در واقع، در صورت عدم امکان ذوب مواد در دستگاه دایکاست با محفظه گرم، دستگاه دارای سیستم تزریق محفظه سرد به کار گرفته میشود. بخشهای مختلف این دستگاه در وضعیت باز در تصویر زیر نمایش داده شدهاند.
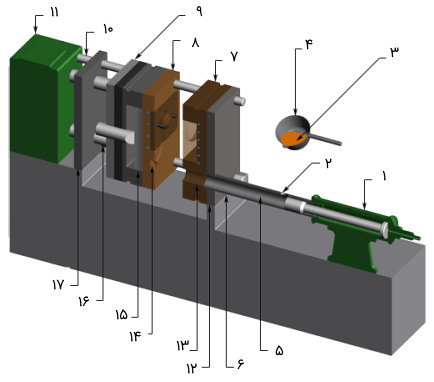
مطابق با تصویر بالا، اجزای دستگاه ریخته گری تحت فشار با محفظه سرد عبارت هستند از:
- سیلندر هیدرولیکی
- حفره ریختن مواد مذاب
- فلز مذاب
- پاتیل
- پلانجر
- محفظه شات
- بخش ثابت قالب
- بخش متحرک قالب
- صفحه متحرک
- میله افقی نگهدارنده
- کلمپینگ
- صفحه ثابت
- غلاف تزریق
- اسپرو یا راهگاه
- سیستم خروج قطعه
- میله کلمپینگ
- صفحه پشتی
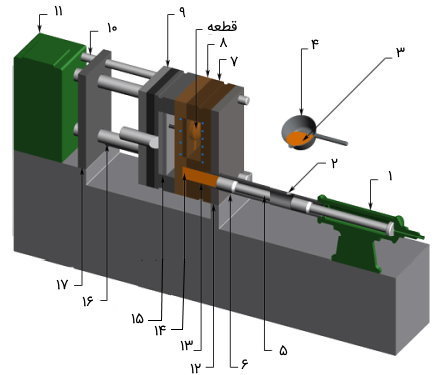
در دستگاه دایکاست محفظه سرد نیز مواد مذاب فلزی درون یک دیگ موجود در کوره نگهداری میشوند. البته در این حالت، دیگ و کوره از دستگاه جدا هستند. به عبارت دیگر، هیچ ارتباط مستقیمی بین اجزای دستگاه و گرمای حاصل از کوره وجود ندارد. انتقال ماده مذاب از دیگ به درون محفظه تزریق، توسط یک پاتیل انجام میگیرد. ماده مذاب از پاتیل به درون حفره ورودی دستگاه و محفظه شات ریخته میشود.
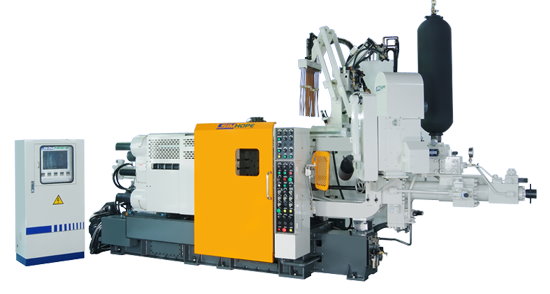
از این مرحله به بعد، مکانیزم عملکرد دایکاست محفظه سرد مشابه با دایکاست محفظه گرم است. با این تفاوت که در این حالت، پلانجر، معمولا در یک مسیر افقی حرکت کرده و فشار مورد نیاز برای تزریق ماده مذاب به درون حفره قالب را فراهم میکند. به علاوه، مجرای گردن غازی در دستگاه محفظه سرد وجود ندارد. فشار تزریق در این دستگاه بین 138 تا 1380 بار است. تصویر متحرک زیر، روند کلی ساخت قطعه با استفاده از دستگاه دایکاست محفظه سرد را نمایش میدهد.
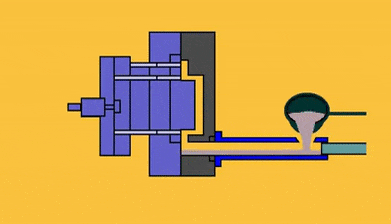
قالب دایکاست چیست ؟
قالب دایکاست، ابزار مخصوص مورد استفاده برای ساخت قطعات در فرآیند ریخته گری تحت فشار است. این قالب از دو بخش ثابت یا «قالب پوششی» (Cover Die) و متحرک یا «قالب پران» (Ejector Die) تشکیل میشود. هر یک از این بخشها، بر روی صفحه مخصوص به خود در دستگاه دایکاست قرار میگیرند. این طراحی، امکان باز و بسته کردن قالب در راستای یک خط جدایش مشخص را فراهم میکند. پس از بسته شدن دو بخش قالب، حفره قالبگیری قطعه تشکیل میشود. تصویر زیر، بخشهای مختلف قالب دایکاست مورد استفاده در دستگاه محفظه گرم در وضعیت باز و بسته را نمایش میدهد.
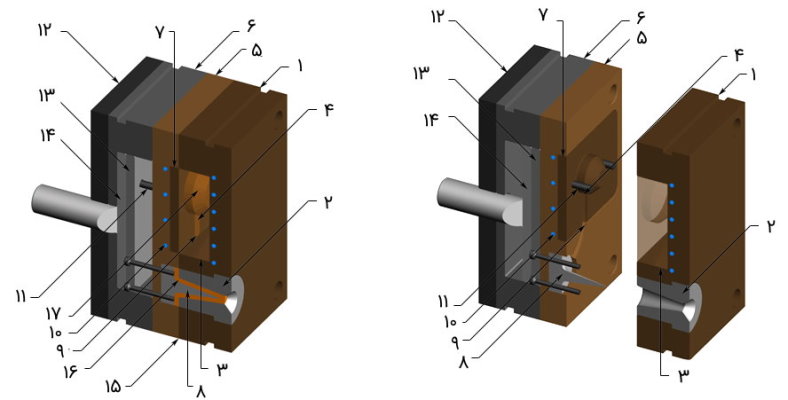
مطابق با تصویر بالا، اجزای قالب ریخته گری برای سیستم تزریق محفظه گرم عبارت هستند از:
- قالب ثابت
- بوش اسپرو یا بوش راهنما
- مغزی حفره
- دریچه
- قالب متحرک
- جعبه پران
- مغزی ماهیچه
- جدا کننده
- راهگاه
- سیستم خنک کننده
- پین پران
- صفحه نگهدارنده
- صفحه حایل
- صفحه پران
- خط جدایش
- اسپرو
- قطعه
اگر قالب بالا را باز کنیم، بخشهای مختلف آن مطابق با تصویر زیر خواهند بود.
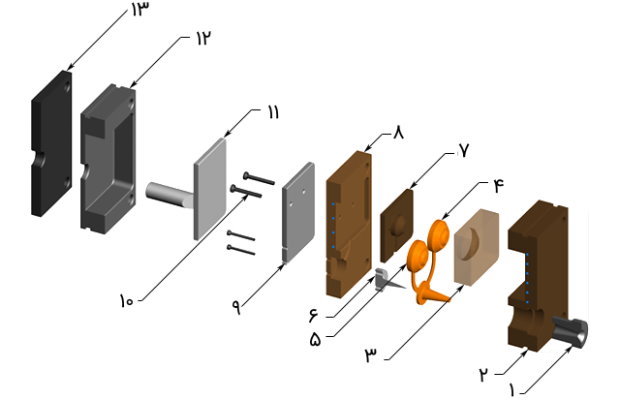
اجزای نمایش داده شده در تصویر بالا عبارت هستند از:
- بوش راهنما
- قالب ثابت
- مغزی حفره
- قطعه A (در این قالب، دو قطعه مشابه به طور همزمان ریخته گری و ساخته میشوند)
- قطعه B
- جدا کننده یا انشعاب مسیر تزریق
- مغزی ماهیچه
- قالب متحرک
- صفحه حائل سیستم پران
- پین پران
- صفحه پران
- جعبه سیستم پران
- صفحه نگهدارنده
در قالب مورد استفاده برای دستگاه دایکاست محفظه سرد، به جای بوش اسپرو، یک غلاف تزریق تعبیه میشود. توجه داشته باشید که قالبهای مورد استفاده برای ساخت قطعات مختلف در ریخته گری تحت فشار دارای اجزای مشترک و متفاوت زیادی هستند. برای قطعاتی با ابعاد و خصوصیات مشابه، اغلب بخشهای قالب بدون تغییر باقی میماند. با این وجود، تفاوت اصلی، بین مغزیهای حفره و ماهیچه در قالب است. این بخشها، شکل قطعه قالب گیری شده و نهایی را تعیین میکنند.
حفره قالب
به فضای خالی بین دو بخش ثابت و متحرک قالب، حفره میگویند. حفره قالب، شکل قطعه مورد نظر را به وجود میآورد. در اغلب موارد، حفره قالب دایکاست از دو مغزی با عنوان «مغزی حفره» (Cavity Insert) و «مغزی ماهیچه» (Core Insert) تشکیل میشود. یکی از این دو بخش درون قالب ثابت و دیگری درون قالب متحرک قرار میگیرد. قالب های صنعتی مورد استفاده در ریخته گری تحت فشار معمولا با در نظر گرفتن دو یا چند حفر طراحی میشوند. این طراحی، امکان ساخت همزمان چندین قطعه مشابه را در یک چرخه فراهم میکند. قالب های دایکاست معمولا دارای 1، 2، 4 یا 8 حفره هستند.
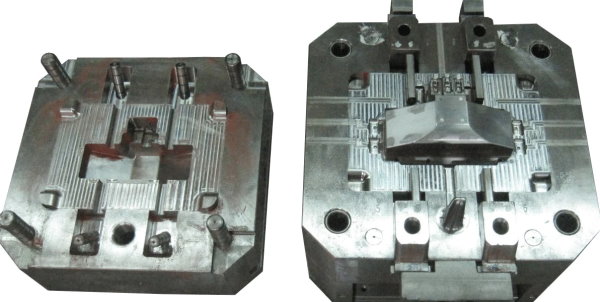
بخش ثابت و متحرک قالب
بخش ثابت قالب ریخته گری تحت فشار، مجموعهای است که امکان جریان یافتن مواد مذاب از طریق سیستم تزریق به درون حفره قالب گیری را فراهم میکند. بخش متحرک قالب، از یک صفحه نگهدارنده و جعبه دربرگیرنده سیستم پران (خروج قطعه پس از انجماد) تشکیل میشود. هنگام جدا شدن نیمههای قالب پس از انجماد مواد مذاب، میلههای افقی، صفحه پران را به سمت جلو هدایت میکنند. حرکت این صفحه به سمت جلو، باعث برخورد پینهای پران به قطعه و جدا شدن آن از درون مغزی میشود.
مجراهای قالب
به منظور حرکت فلز مذاب و ریختن آن به درون حفره، از مجراهای مختلفی در ساختار قالب استفاده میشود. البته مجراهای تزریق مواد در دستگاههای دایکاست محفظه گرم و سرد، با یکدیگر کمی تفاوت دارند. در دستگاههای محفظه گرم، فلز مذاب از بوش اسپرو (بر روی بخش ثابت) به درون قالب وارد میشود. سپس، با جریان در اطراف جدا کننده (بر روی بخش متحرک)، به سمت حفرهها حرکت میکند. به عبارت دیگر، اسپرو، مجرای اصلی ورود مواد مذاب به قالب است. در دستگاه محفظه سرد، ورود فلز مذاب از طریق غلاف تزریق صورت میگیرد. سپس، فلز مذاب از طریق شبکه مجراهای تعبیه شده درون قالب، به سمت حفرهها جریان مییابد. به آخرین مجرای متصل به حفره، دریچه میگویند.
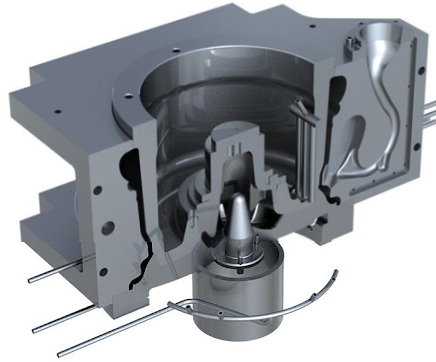
حفرههای قالب، معمولا دارای فضای اضافی یا اصطلاحا «چشمه سریز» (Overflow Well) هستند. طی فرآیند انجماد، حجم قطعه کاهش مییابد. در این شرایط، مواد مذاب اضافی مورد نیاز برای پر کردن فضای خالی ناشی از جمعشدگی قطعه، توسط چشمههای سرریز تامین میشوند. علاوه بر این موارد، تعدادی مجرا در ساختار قالب وجود دارند که به منظور خروج هوا از حفره مورد استفاده قرار میگیرند. مواد مذاب از تمام مجراهای درون ساختار قالب، به غیر از مجراهای سیستم خنک کاری عبور میکنند. درون این سیستم، آب یا روغن جریان دارد.
قطعه
مواد مذاب عبوری از مجراهای قالب به همراه مواد درون حفرهها سرد میشوند. به این ترتیب، زائدههایی بر روی قطعه قالب گیری شده به وجود میآیند. پس از خروج قطعه قالب گیری شده، این زائدهها توسط روشهای ماشینکاری یا برشکاری جدا میشوند. در بخش اصول طراحی قالب دایکاست، به نکات بیشتری در زمینه جزئیات قالبهای مورد استفاده در فرآیند ریخته گری تحت فشار خواهیم پرداخت.
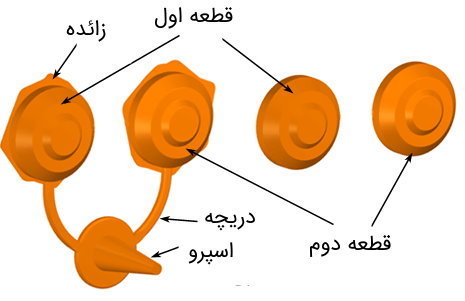
مزایای دایکاست چیست؟
دایکاست، یک فرآیند کارآمد و اقتصادی است که امکان ساخت و تولید قطعات پیچیده و با کیفیت بالا را فراهم میکند. یکپارچگی قطعات ساخته شده توسط این روش، هزینه ماشینکاری و تهیه تجهیزات مربوط به آن را کاهش میدهد. البته صرفه اقتصادی ریخته گری تحت فشار در تولید انبوه قطعات است. از مزیتهای دایکاست میتوان به موارد زیر اشاره کرد:
- ساخت قطعات دارای شکل پیچیده با دقت بالاتر نسبت به دیگر روشهای تولید انبوه
- نرخ تولید بالا و حداقل نیاز یا عدم نیاز به ماشینکاری
- دوام بالا، ابعاد دقیق، کیفیت ساخت و ظاهر مناسب قطعات نهایی
- امکان ساخت قطعات نازکتر نسبت به دیگر روشهای ریخته گری و مقاومتر نسبت به روش تزریق پلاستیک (با ابعاد یکسان)
- قابلیت استفاده مجدد از قالبهای دایکاست به منظور ساخت هزاران قطعه با تلرانس مشخص
- امکان پوششدهی یا پرداخت قطعات ساخته شده توسط دایکاست روی با حداقل آمادهسازی ممکن
- امکان تولید قطعات با بافتهای متنوع
- هزینه پایین نیروی کار
- امکان بازیافت و استفاده مجدد مواد
- خروج راحتتر قطعات به دلیل سطح صاف قالبهای دایکاست نسبت به روشهای ریخته گری دقیق، ماسهای و دائمی
- حفاری حفرههای قطعات دایکاست و ساخت حفره با ابعاد مشخص (مطابق با اتصالات مورد نظر)
- ایجاد آسان روزه بر روی سطح خارجی قطعات
- طراحی المانهای پیچی داخلی و کاهش هزینههای سر و هم کردن تجهیزات
- تزریق فلزات دیگر و مواد غیر فلزی برای ریخته گری تحت فشار برجا
- مقاومت خوب تا عالی در برابر خوردگی
- یکپارچگی بالا (امکان ساخت چندین قطعه متصل به هم با کاربردهای متفاوت به صورت یک قطعه یکپارچه)
معایب دایکاست چیست؟
با وجود مزایای متعدد ریخته گری تحت فشار، این روش از محدودیتهایی نیز برخوردار است که از مهمترین آنها عبارت هستند از:
- عدم کاربری مناسب برای فلزات و آلیاژهای دارای نقطه ذوب بالا مانند فولاد
- دشوار بودن قالبگیری و ساخت قطعات بزرگ
- هزینه بالای سرمایهگذاری و تهیه قالب
- زمان نسبتا زیاد چرخه تولید (از دریافت سفارش تا تحویل قطعات به مشتری)
- امکان گیر افتادن گازهای حاصل از مواد مذاب و تشکیل حباب درون قطعه
- غیر اقتصادی بودن روش برای تولید قطعات در تعداد کم
- وابستگی روش به جریانپذیری مواد در حالت مذاب
عیوب ریخته گری دایکاست چه هستند؟
ایجاد زائدههای ناخواسته بر روی قطعه، پر نشدن کامل حفرههای قالب، ایجاد حباب، تشکیل ترکهای گرم (ترکهای ناشی از جمع شدگی) و باقی ماندن اثر پین پران بر روی قطعه از عیب و نقصهای احتمالی در فرآیند ریخته گری تحت فشار هستند. روش دایکاست مانند تمام روشهای ساخت و تولید، نیازمند نظارت کافی برای دستیابی به قطعهای با کیفیت است. در صورت عدم رعایت مسائل فنی و اجرایی، احتمال ایجاد عیب و نقصهای مذکور در قطعه افزایش مییابد.
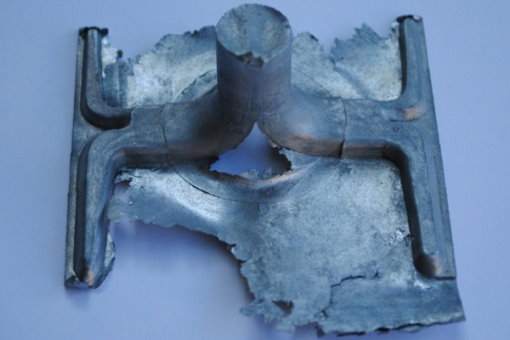
عوامل به وجود آورنده هر یک از این عیب و نقصهای دایکاست عبارت هستند از:
- زائدههای ناشی از بیرونزدگی مواد مذاب: زیاد بودن فشار تزریق و یا کم بودن نیروی لازم برای بسته نگه داشتن بخش متحرک قالب
- عدم پر شدن کامل حفرهها: کافی نبودن حجم شات تزریق، کم بودن سرعت تزریق و یا پایین بودن دمای مواد در حین تزریق
- تشکیل حباب در ساختار قطعه: بالا بودن دمای مواد در حین تزریق و یا عدم یکنواختی نرخ خنک شدن
- ایجاد ترک گرم: یکنواخت نبودن نرخ خنک شدن
- ایجاد علامت در حین خروج قطعه: کم بودن زمان خنک شدن و یا بالا بودن نیروی خروج
بسیاری از عیوب ریخته گری تحت فشار به نرخ خنک شدن مواد مذاب و میزان یکنواختی این نرخ بستگی دارند. عواملی نظیر یکنواختی ضخامت دیواره و یکنواختی دمای قالب به طور مستقیم بر روی این پارامتر تاثیر میگذارند.
اصول طراحی قالب دایکاست چه هستند؟
طراحی قالب های ریخته گری باید با توجه به قابلیت ساخت، وزن قالب، ضخامت دیوارهها، یکنواختی ضخامت، زاویه خروج، شکل گوشهها و بهینهسازی فرآیند انجام گیرد. نکات متعددی در طراحی قالبهای دایکاست وجود دارند که در این بخش، به معرفی مهمترین آنها میپردازیم.
قواعد کلی در طراحی قالب دایکاست
در طراحی قالب های صنعتی برای ریخته گری تحت فشار، توجه به نکات و قواعد زیر میتواند نتیجه کار را به میزان قابل توجهی بهبود بخشد:
- حداکثر ضخامت دیواره: هر چه ضخامت قطعه کمتر باشد، چرخه ریخته گری (زمان تزریق و خنک کردن) کوتاهتر میشود. این پارامتر بر روی حجم قطعه و مواد مذاب مورد نیاز برای ساخت آن تاثیر میگذارد. از اینرو، ضخامت قطعه باید در جهت بهینه کردن زمان و مواد مصرفی طراحی شود.
- یکپارچگی ضخامت دیواره: یکپارچگی از عوامل بسیار مهم در خنک شدن یکسان تمام بخشهای قطعه و کاهش عیبهای احتمالی است.
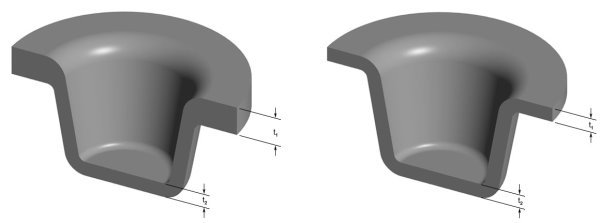
- شکل گوشه: هر چه گوشههای قطعه با شعاع انحنای مناسبتری طراحی شده باشند، احتمال ایجاد تمرکز تنش و رخ دادن شکستگی در قطعه کمتر میشود. شعاع انحنای داخلی گوشههای قطعه باید حداقل برابر با ضخامت دیواره آن باشد.
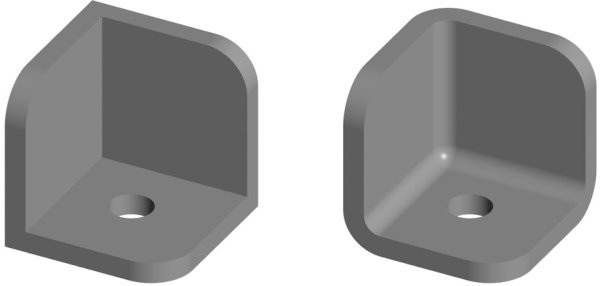
- زاویه خروج: طراحی زاویه مناسب برای تمامی دیوارهها، فرآیند خارج کردن قطعه پس از انجماد را سادهتر میکند. زاویه خروج پیشنهادی برای فلزات مختلف عبارت هستند از:
- زاویه خروج آلومینیوم: 1 درجه برای دیوارهها و 2 درجه برای ماهیچههای داخلی
- زاویه خروج منیزیوم: 0.75 درجه برای دیوارهها و 1.5 درجه برای ماهیچههای داخلی
- زاویه خروج روی: 0.5 درجه برای دیوارهها و 1 درجه برای ماهیچههای داخلی

- آندرکات: باید از حداقل آندرکات خارجی ممکن برای کنترل حرکت قطعه در حین تزریق و خنک شدن استفاده کرد. افزایش تعداد آندرکاتهای خارجی، افزایش ماهیچههای کناری و هزینه ماشینکاری بیشتر را در پی دارد. طراحی مناسب قالب و بهرهگیری از خط جدایش آن میتواند این مسئله را برطرف کند. علاوه بر این، توجه به آندرکاتهای داخلی و احتمال گیر کردن قطعه پس از انجماد نیز از مسائل مهم طراحی به شمار میرود. جهت باز و بسته کردن قالب، پارامتر اصلی در این مورد است.
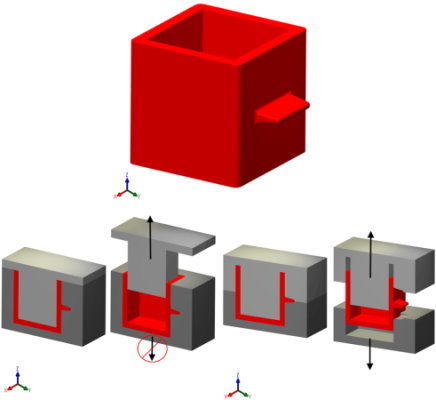
رعایت موارد بالا میتواند عملکرد صحیح مکانیزم دایکاست و کیفیت ساخت قطعه را تا حد قابل قبولی تضمین کند. با این وجود، نکات و قواعد طراحی قالب های صنعتی مورد استفاده در فرآیند ریخته گری تحت فشار به موارد معرفی شده محدود نمیشوند. برخی دیگر از موارد قابل ذکر عبارت هستند از:
- قالب ریخته گری تحت فشار باید امکان حرکت راحت فلز مذاب را درون تمام کانالها و حفرههای موجود فراهم کند.
- توجه به باز و بسته شدن راحت قالب و عدم تداخل بخشهای مختلف قطعه با اجزای قالب از دیگر نکات مهم طراحی است.
- جنس مواد مورد استفاده برای ساخت قالب، بر روی عمر مفید و تعداد چرخههای استفاده از آن تاثیر میگذارد. قالبهای فولادی با عیار بالا برای 100 تا 150000 چرخه ساخت قابل استفاده هستند. البته در صورت به کارگیری قالبهای فولادی با کربن پایینتر، تعداد چرخههای ساخت به حدود 1 میلیون میرسد.
از دیگر عوامل موثر بر طراحی دایکاست، مشخصات دستگاه مورد استفاده در این فرآیند است. در بخش بعدی به معرفی این مورد میپردازیم.
مشخصات دستگاه دایکاست محفظه سرد و گرم
کلاسهای مختلف دستگاههای دایکاست با سیستم تزریق محفظه گرم و سرد، معمولا با توجه به میزان نیروی قابل تامین برای بسته نگه داشتن قالب تقسیمبندی میشوند. هر چه ابعاد قطعه مورد نظر بزرگتر باشد، توانایی دستگاه در تامین این نیرو بیشتر خواهد بود.در صورت نیاز به فشار بیشتر برای تزریق مواد خاص، احتمال نیاز به نیروی بیشتر برای بسته نگه داشتن قالب افزایش مییابد. علاوه بر این موارد، ابعاد قطعه باید با مشخصات دیگر دستگاه نظیر حداکثر حجم قابل تزریق (شات)، فاصله بین دو بخش قالب در حالت باز، حداقل ضخامت قالب و ابعاد صفحات نگهدارنده قالب همخوانی داشته باشد.
ابعاد قطعات قابل ساخت توسط ریخته گری تحت فشار متفاوت است. از اینرو، هر یک از دستگاههای دایکاست برای پوشش دادن بازه مشخصی از این ابعاد طراحی میشوند. مشخصات برخی از انواع متداول این دستگاهها مطابق با جدول زیر هستند.
نوع | محفظه گرم | محفظه سرد |
نیروی فشردگی قالب (نیروی بسته نگه داشتن دو بخش) بر حسب تن متریک | 90 - 180 - 360 | 90 - 180 - 360 - 720 - 1450 - 1800 |
حداکثر حجم هر شات تزریق بر حسب لیتر | 2.18 - 3.43 - 7.51 | 1.04 - 4.91 - 11.68 - 31.29 - 44.86 |
حداکثر فاصله بین قالب ثابت و متحرک بر حسب سانتیمتر | 30 - 40 - 55 | 30 - 55 - 76 - 100 - 130 |
حداقل ضخامت دیواره قالب بر حسب سانتیمتر | 15 - 25 - 30 | 15 - 30 - 40 - 50 - 65 |
ابعاد صفحه نگهدارنده قالب بر حسب سانتیمتر در سانتیمتر | 61*61 - 73*73 - 96*96 | 58*58 - 73*73 - 139*139 - 188**200 - 210*210 |
همانطور که از جدول بالا مشخص است؛ ابعاد و توان مدلهای رایج دستگاه دایکاست با محفظه سرد بیشتر از دستگاه دایکاست با محفظه گرم است.
مواد مورد استفاده در دایکاست چه هستند؟
ریخته گری تحت فشار معمولا به منظور ساخت قطعاتی از جنس آلیاژهای غیر آهنی مورد استفاده قرار میگیرد. آلیاژهای آلومینیوم، مس، منیزیم و روی از متدوالترین مواد مورد استفاده در این روش ریخته گری هستند. البته دایکاست برای ساخت قطعات چدنی نیز کاربرد دارد. طبیعتا جنس مواد مورد استفاده در کاربریهای مختلف با یکدیگر تفاوت دارند. از اینرو، عنوان دایکاست در صنایع مختلف به همراه عبارت مواد مصرفی در آنها (نظیر دایکاست آلومینیوم یا دایکاست زاماک) شناخته میشود.
کاربرد آلومینیوم در دایکاست چیست؟
دایکاست آلومینیوم از پرکاربردترین روشهای ریخته گری تحت فشار است که در صنایع مختلف مورد استفاده قرار میگیرد. قطعات آلومینیومی جایگزین قطعات آهنی و فولادی در صنعت خودروسازی هستند. این مواد به دلیل وزن پایینتر، مصرف سوخت خودروها را کاهش میدهند. قطعات لوازم خانگی و کانکتورهای الکترونیکی نیز معمولا به روش دایکاست آلومینیوم ساخته میشوند. چارچوب پنجره، چوب پرده، پارتیشن، اتصالات لولهکشی (پایپینگ و تاسیسات بهداشتی ساختمان) و نمای آلومینیومی ساختمانها نیز توسط روشهای ریخته گری تحت فشار ساخته میشوند.
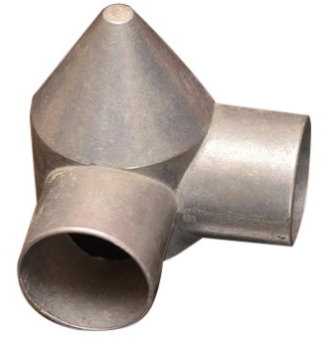
کاربرد زاماک در دایکاست چیست؟
«زاماک» (ZAMAK)، یکی از آلیاژهای فلز روی با آلومینیوم، منیزیوم و مس است که به عنوان زیر مجموعه آلیاژ روی و آلومینیوم در نظر گرفته میشود. زاماک، کاربرد بسیار گستردهای در صنایع اتومبیلسازی دارد. مقاومت و سختی بالای این آلیاژ، آن را به یک گزینه مناسب برای ساخت قطعات به روش ریخته گری تحت فشار تبدیل میکند. دایکاست روی در ساخت سیستمهای سوخترسانی، سیستمهای ترمز و سیستمهای سرمایشی خودروها کاربرد دارد. ساخت قطعات الکترونیکی و قطعات پیچیده از دیگر قابلیتهای دایکاست زاماک هستند.
کاربرد منیزیوم در دایکاست چیست؟
منیزیوم، هشتمین عنصر فراوان بر روی کره زمین است. فراوانی این فلز، هزینه ساخت قطعات منیزیمی نسبت به فلزات دیگر را کاهش میدهد. قطعات ساخته شده به روش دایکاست منیزیوم از وزن پایین بهره میبرند. به همین دلیل، این روش در صنایع تولید لوازم خانگی، بدنه قطعات الکترونیکی، اجزای خودروها مسابقهای و تجهیزات هوافضا به کار برده میشود.
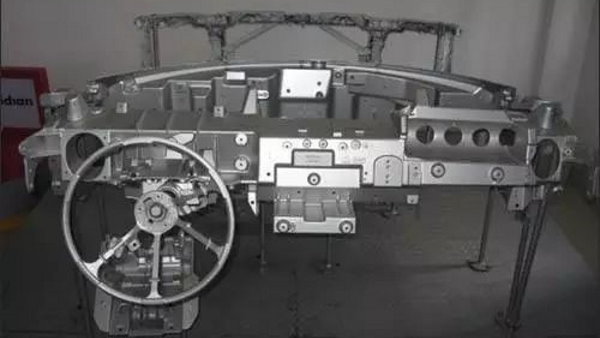
کاربرد قلع در دایکاست چیست؟
قلع، فلزی با دمای ذوب پایین، روانگرایی بالا در حالت مذاب و جمع شدگی پایین در حین فرآیند انجماد است. مشخصات مکانیکی و غیر سمی قلع، این فلز را به گزینه مناسب برای دایکاست قطعات با دقت بسیار بالا تبدیل کردهاند. دایکاست قلع معمولا به منظور ساخت وسایل تزئینی و جواهرات مورد استفاده قرار میگیرد. قطعات کوچک و حساس لوازم خانگی، موتورها، ژنراتورها، توربینها و تجهیزات حمل مواد غذایی نیز به وسیله این روش ساخته میشوند.
علاوه بر موارد ذکر شده، دایکاست برنج و دایکاست چدن نیز کاربرد فراوانی در ساخت و تولید قطعات مختلف دارند. در واقع، ویژگیهای مکانیکی، خواص ترمودینامیکی و پارامترهای اقتصادی، عواملی هستند که باعث انتخاب مواد مناسب در فرآیند ریخته گری تحت فشار برای کاربردهای متفاوت میشوند.
مقایسه دایکاست و قالب گیری تزریقی
تفاوت اصلی ریخته گری تحت فشار و قالب گیری تزریقی در ماده مورد استفاده برای ساخت قطعات است. دایکاست به عنوان یکی از متداولترین روشهای تولید انبوه قطعات فلزی (مخصوصا قطعات آلومینیومی) با ابعاد کوچک تا متوسط شناخته میشود.
در صورتی که قالبگیری تزریقی، رایجترین روش ساخت قطعات پلاستیکی در صنایع مختلف است. با این وجود، شباهتهای زیادی در مکانیزم قالبگیری و ساخت قطعه توسط این دو روش وجود دارد. تصویر متحرک زیر، عملکرد دستگاه قالبگیری تزریق پلاستیک را نمایش میدهد.
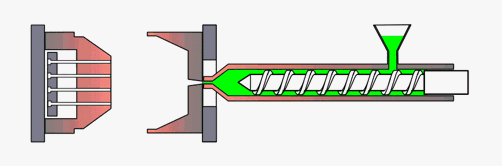
همانطور که مشاهده میکنید، مراحل ساخت قطعه به روش قالبگیری تزریقی، شباهت زیادی به روش دایکاست دارند. با این وجود، ممکن است برایتان این سوال پیش بیاید که چرا باید از این روشها به جای یکدیگر استفاده کرد. جواب این سوال به پارامترهای اقتصادی و قابلیت ساخت ارتباط دارد. هزینه تولید انبوه قطعات فلزی بسیار بیشتر از قطعات پلاستیکی و وزن قطعات پلاستیکی کمتر از قطعات فلزی است.
در طرف مقابل، قطعات ساخته شده توسط روش دایکاست، از دقت و کیفیت بالایی برخوردار هستند. علاوه بر این، ریخته گری تحت فشار، امکان تولید انبوه قطعات پیچیده در مدت زمان کوتاه را فراهم میکند. با در نظر گرفتن این ویژگیها میتوان مناسبترین گزینه از میان این دو روش و دیگر روشهای ساخت و تولید را انتخاب کرد.
انواع روش های اجرای دایکاست کدام هستند؟
ریخته گری تحت فشار بالا به عنوان روش استاندارد اجرای دایکاست شناخته میشود. با این حال، امکان اجرای دایکاست توسط روشهای دیگری نظیر ریخته گری تحت فشار پایین، ریخته گری تحت فشار در خلا، ریخته گری تحت فشار کوبشی و ریخته گری تحت فشار نیمه جامد وجود دارد. هر یک از این روشها برای کاربریهای مختص به خود مناسب هستند.
ریخته گری تحت فشار پایین
ریخته گری تحت فشار پایین، فرآیند اصلی مورد استفاده در دستگاههای دایکاست با سیستم تزریق محفظه گرم است. این فرآیند، به منظور ساخت قطعاتی با وزن 2 تا 150 کیلوگرم مورد استفاده قرار میگیرد. دایکاست فشار پایین، امکان ساخت قطعات پیچیده با مقاومت بالا را فراهم میکند. به علاوه، این فرآیند، دقت ابعادی قطعه و کنترل مواد مذاب مصرفی را افزایش میدهد. حداقل ضخامت دیواره قابل ساخت با ریخته گری تحت فشار پایین برابر 30 میلیمتر است.
ریخته گری تحت فشار بالا
ریخته گری تحت فشار بالا، از روشهای اصلی دایکاست توسط دستگاههای دارای سیستم تزریق محفظه گرم به شمار میرود. فرآیند اجرای این روش در بخشهای قبلی به طور کامل مورد بررسی قرار گرفته است.
ریخته گری تحت فشار در خلا
از روشهای جدید دایکاست میتوان به ریخته گری تحت فشار در خلا اشاره کرد. قطعات ساخته شده با این روش، از مقاومت بالا و تخلخل پایین بهره میبرند. مکانیزم دایکاست در خلا به مکانیزم ریخته تحت فشار پایین شباهت دارد. البته پیکربندی قالب و مخزن فلز مذاب متفاوت است. در این روش، سیلندر خلا، اختلاف فشار مورد نیاز برای انتقال مواد مذاب به درون حفرهها را فراهم میکند. ریخته گری تحت فشار در خلا به منظور ساخت قطعات نیازمند عملیات حرارتی مورد استفاده قرار میگیرد.
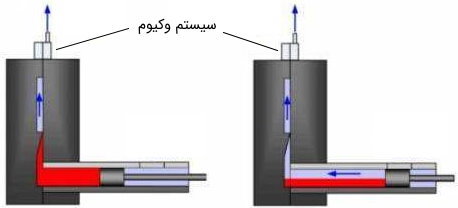
ریخته گری تحت فشار کوبشی
جریانپذیری و روانگرایی فلزها و آلیاژهای مذاب، از پارامترهای مهم در قابلیت ساخت قطعات به روش دایکاست است. ریخته گری تحت فشار کوبشی، امکان دایکاست فلزاتی با جریانپذیری پایین را فراهم میکند. در این روش، فلز مذاب درون یک قالب باز ریخته میشود. با اعمال فشار بر روی مواد مذاب، این مواد به درون حفره جریان مییابند. ریخته گری تحت فشار کوبشی در تقویت مواد الیافی و آلومینیوم مذاب کاربرد دارد. چگالی قطعه ساخته شده توسط این روش، بالا است.
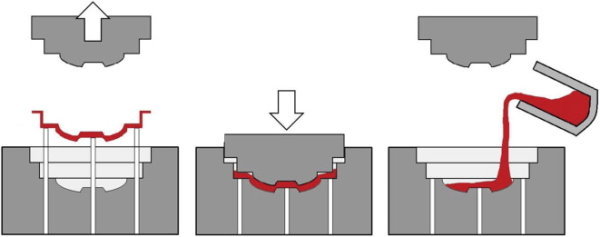
ریخته گری تحت فشار نیمه جامد
از دیگر روشهای اجرای دایکاست میتوان به ریخته گری تحت فشار نیمه جامد اشاره کرد. این روش با عنوان شکل دهی حرارتی نیز شناخته میشود. دایکاست نیمه جامد نیز مانند دایکاست کوبشی، امکان دستیابی به حداکثر چگالی ممکن و حداقل تخلخل ممکن را فراهم میکند. در این روش، فلزات پیش از قرارگیری در کوره به قطعات کوچک برش داده میشوند. پس از اعمال حرارت، تزریق مواد در میانه فرآیند تغییر فاز جامد به مایع صورت میگیرد. در واقع، مواد نیمه جامد با فشار بالا به درون حفرههای قالب تزریق میشوند. ریخته گری تحت فشار نیمه جامد به منظور ساخت قطعات منیزیمی و آلیاژهای آلومینیومی مورد استفاده قرار میگیرد.
سلام عالی بود،فقط اگه کاملترتوضیح میدادیدبرای اونایی که تازه کارهستن بهتربود،یه سئوال،برای دایکست باآلومینیوم بهترین جنس برای ساخت پیستون داخل سیلندربرای تزریق چیه؟واینکه برای تراش پیستون داخل سیلندرتزریق اندازه پبستون چقدکمترازسیلندرباشه که پیستون راحت ورون کارکنه واینکه بارازپشت پیستون نپاشه بیرون،ممنون ازشما.
عالی.تشکر از توضیح جامع
برای ارایه مطالب زحمت زیادی کشیده شده است.بسیار ممنونیم.
خصوصا اگر دوستان موارد ایراد مطالب را ذکر کنند.
سلام تشکر خیلی زحمت برای تهیه مطلب کشیده شده است ولی اشتباهات ناجوری نیز در آن است بهتر است قبل از انتشار مطلب آن مقاله توسط کارشناس با تجربه مورد بررسی قرار گیرد
سلام و وقت بخیر؛
از این که نظر خود را با ما به اشتراک گذاشتید، بسیار سپاسگزاریم. ممنون میشویم اگر اشتباهات و اشکالات مورد نظر خود را بیان کنید تا در صورت صحت نظر شما، آنها را برطرف کنیم.
با تشکر.